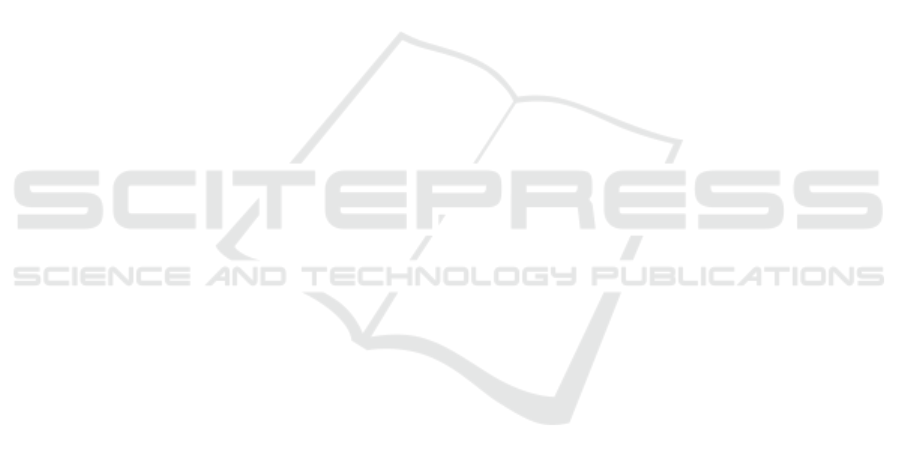
ACKNOWLEDGEMENTS
The authors acknowledge the support by the Deutsche
Forschungsgemeinschaft (DFG) under grant number
341489206. MATLAB Code to reproduce the results
is available at GitHub under free license at https://
github.com/SchapplM/robotics-paper_icinco2021.
REFERENCES
Agarwal, A., Nasa, C., and Bandyopadhyay, S. (2016). Dy-
namic singularity avoidance for parallel manipulators
using a task-priority based control scheme. Mecha-
nism and Machine Theory, 96:107–126.
Chiaverini, S., Oriolo, G., and Walker, I. D. (2008). Kine-
matically redundant manipulators. In Springer Hand-
book of Robotics, pages 245–268. Springer.
Corinaldi, D., Angeles, J., and Callegari, M. (2016). Pos-
ture optimization of a functionally redundant parallel
robot. In Advances in Robot Kinematics 2016, pages
101–108. Springer.
De Luca, A., Oriolo, G., and Siciliano, B. (1992). Robot
redundancy resolution at the acceleration level. Labo-
ratory Robotics and Automation, 4:97–97.
Gao, Y., Chen, K., Gao, H., Xiao, P., and Wang, L. (2019).
Small-angle perturbation method for moving platform
orientation to avoid singularity of asymmetrical 3-
RRR planner parallel manipulator. Journal of The
Brazilian Society of Mechanical Sciences and Engi-
neering, 41:1–18.
Gosselin, C. and Schreiber, L.-T. (2016). Kinematically
redundant spatial parallel mechanisms for singularity
avoidance and large orientational workspace. IEEE
Transactions on Robotics, 32(2):286–300.
Gosselin, C. and Schreiber, L.-T. (2018). Redundancy in
Parallel Mechanisms: A Review. Applied Mechanics
Reviews, 70(1).
Guo, Y., Dong, H., and Ke, Y. (2015). Stiffness-oriented
posture optimization in robotic machining applica-
tions. Robotics and Computer-Integrated Manufac-
turing, 27(2):367–376.
Huo, L. and Baron, L. (2008). The joint-limits and singu-
larity avoidance in robotic welding. Industrial Robot:
An International Journal, 35(5):456–464.
Kotlarski, J., Do Thanh, T., Heimann, B., and Ortmaier,
T. (2010). Optimization strategies for additional ac-
tuators of kinematically redundant parallel kinematic
machines. In 2010 IEEE International Conference on
Robotics and Automation (ICRA), pages 656–661.
Žlajpah, L. (2017). On orientation control of functional
redundant robots. In 2017 IEEE International Con-
ference on Robotics and Automation (ICRA), pages
2475–2482.
Léger, J. and Angeles, J. (2016). Off-line programming
of six-axis robots for optimum five-dimensional tasks.
Mechanism and Machine Theory, 100:155–169.
Lillo, P. D., Chiaverini, S., and Antonelli, G. (2019). Han-
dling robot constraints within a set-based multi-task
priority inverse kinematics framework. In 2019 IEEE
International Conference on Robotics and Automation
(ICRA), pages 7477–7483.
Luces, M., Mills, J. K., and Benhabib, B. (2017). A review
of redundant parallel kinematic mechanisms. Journal
of Intelligent & Robotic Systems, 86:175–198.
Merlet, J.-P. (2006). Jacobian, manipulability, condition
number, and accuracy of parallel robots. Journal of
Mechanical Design, 128(1):199–206.
Merlet, J.-P., Perng, M.-W., and Daney, D. (2000). Optimal
trajectory planning of a 5-axis machine-tool based on
a 6-axis parallel manipulator. In Advances in Robot
Kinematics, pages 315–322. Springer.
Mousavi, S., Gagnol, V., Bouzgarrou, B. C., and
Ray, P. (2018). Stability optimization in robotic
milling through the control of functional redundan-
cies. Robotics and Computer-Integrated Manufactur-
ing, 50:181–192.
Nakamura, Y., Hanafusa, H., and Yoshikawa, T. (1987).
Task-priority based redundancy control of robot ma-
nipulators. The International Journal of Robotics Re-
search, 6(2):3–15.
Oen, K.-T. and Wang, L.-C. T. (2007). Optimal dynamic
trajectory planning for linearly actuated platform type
parallel manipulators having task space redundant de-
gree of freedom. Mechanism and Machine Theory,
42(6):727–750.
Ozgoren, M. K. (2013). Optimal inverse kinematic solu-
tions for redundant manipulators by using analytical
methods to minimize position and velocity measures.
Journal of Mechanisms and Robotics, 5(3).
Reiter, A., Müller, A., and Gattringer, H. (2018). On higher
order inverse kinematics methods in time-optimal tra-
jectory planning for kinematically redundant manipu-
lators. IEEE Transactions on Industrial Informatics,
14(4):1681–1690.
Santos, J. C. and da Silva, M. M. (2017). Redundancy res-
olution of kinematically redundant parallel manipula-
tors via differential dynamic programing. Journal of
Mechanisms and Robotics, 9(4).
Schappler, M., Tappe, S., and Ortmaier, T. (2019).
Modeling parallel robot kinematics for 3T2R and
3T3R tasks using reciprocal sets of Euler angles.
MDPI Robotics, 8(3). Open access journal. Online:
https://doi.org/10.3390/robotics8030068.
Shaw, D. and Chen, Y.-S. (2001). Cutting path generation
of the stewart-platform-based milling machine using
an end-mill. International Journal of Production Re-
search, 39(7):1367–1383.
Smirnov, V., Plyusnin, V., and Mirzaeva, G. (2013). Energy
efficient trajectories of industrial machine tools with
parallel kinematics. In 2013 IEEE International Con-
ference on Industrial Technology (ICIT), pages 1267–
1272.
Zhu, W., Qu, W., Cao, L., Yang, D., and Ke, Y. (2013).
An off-line programming system for robotic drilling
in aerospace manufacturing. The International Jour-
nal of Advanced Manufacturing Technology, 68(9-
12):2535–2545.
Singularity Avoidance of Task-redundant Robots in Pointing Tasks: On Nullspace Projection and Cardan Angles as Orientation Coordinates
349