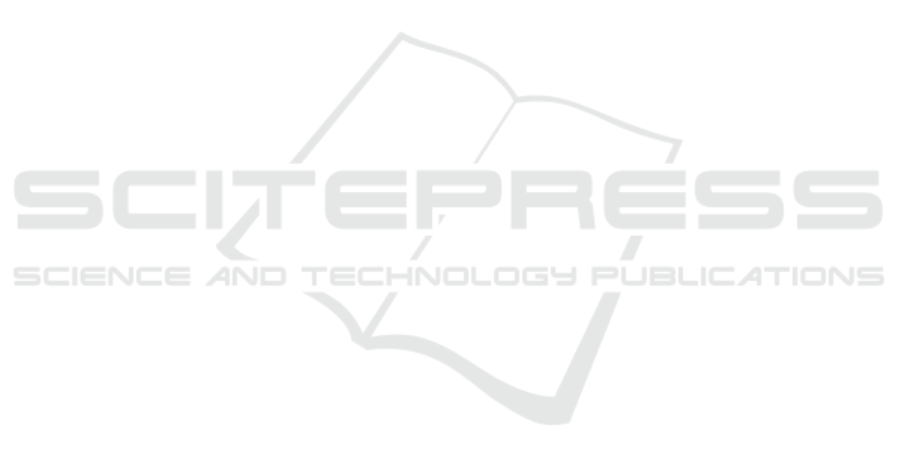
pletely hosted on-premises. To realize the full poten-
tial of a hybrid cloud co-simulation solution based on
the HUBCAP platform the following need to be ad-
dressed in future work:
First and foremost, automated orchestration of the
cloud environment via an API or a federated cloud
approach where users can add their private resources
as computation nodes (virtual machines) to a particu-
lar HUBCAP sandbox would ease the dataflow of our
experiment that could be automated instead of a man-
ual data iteration (upload new timing settings from a
configuration file, run experiment, download result...)
Also, the improvement of intellectual property protec-
tion and licensing makes the platform more suitable
for adoption by industrial partners. The co-simulation
data and environment shared between TTS and VV
was protected under existing contractual agreements
between the two partners. To be useful, the coupling
of the private resources and hybrid cloud should also
be available to be used by other partners in the MBD
community without any legal binding. Both by guar-
anteeing the privacy of the platform user data and by
allowing external partners to host their IP protected
components locally.
ACKNOWLEDGEMENTS
The work presented here is partially supported by the
HUBCAP Innovation Action funded by the European
Commission’s Horizon 2020 Programme under Grant
Agreement 872698.
The publication was partly written at Virtual Ve-
hicle Research GmbH in Graz, Austria. The au-
thors would like to acknowledge the financial support
within the COMET K2 Competence Centres for Ex-
cellent Technologies from the Austrian Federal Min-
istry for Climate Action (BMK), the Austrian Federal
Ministry for Digital and Economic Affairs (BMDW),
the Province of Styria (Dept. 12) and the Styrian
Business Promotion Agency (SFG). The Austrian Re-
search Promotion Agency (FFG) has been authorised
for the programme management.
REFERENCES
Atzeni, G., Vignali, G., Tebaldi, L., and Bottani, E. (2021).
A bibliometric analysis on collaborative robots in lo-
gistics 4.0 environments. Procedia Computer Science,
180:686–695.
Badicu, A., Iordache, G., Suciu, G., Macedo, H. D., Sas-
sanelli, C., Terzi, S., and Larsen, P. G. (2021). De-
ploying the Smart Energy Tool for Investment Simu-
lation inside the HUBCAP Sandbox. To appear at the
9th International Workshop on Simulation for Energy,
Sustainable Development and Environment.
Braun, S., Bartelt, C., Obermeier, M., Rausch, A., and
Vogel-Heuser, B. (2012). Requirements on evolution
management of product lines in automation engineer-
ing. IFAC Proceedings Volumes, 45(2):340–345.
Fitzgerald, J., Larsen, P. G., and Verhoef, M., editors
(2014). Collaborative Design for Embedded Systems
– Co-modelling and Co-simulation. Springer.
Hasselbring, W., Henning, S., Latte, B., M
¨
obius, A.,
Richter, T., Schalk, S., and Wojcieszak, M. (2019).
Industrial devops. In 2019 IEEE International Confer-
ence on Software Architecture Companion (ICSA-C),
pages 123–126. IEEE.
Kulik, T., Macedo, H. D., Talasila, P., and Larsen, P. G.
(2021). Modelling the HUBCAP sandbox architec-
ture in VDM: A study in security. John Fitzgerald,
Tomohiro Oda, and Hugo Daniel Macedo (Editors),
page 20.
Larsen, P. G., Macedo, H. D., Fitzgerald, J., Pfeifer, H.,
Benedikt, M., Tonetta, S., Marguglio, A., Gusmeroli,
S., and Jr., G. S. (2020). A Cloud-based Collaboration
Platform for Model-based Design of Cyber-Physical
Systems. pages 263–270. INSTICC, Proceedings of
the 10th International Conference on Simulation and
Modeling Methodologies, Technologies and Applica-
tions - Volume 1: SIMULTECH.
Lee, J., Bagheri, B., and Kao, H.-A. (2015). A cyber-
physical systems architecture for industry 4.0-based
manufacturing systems. Manufacturing letters, 3:18–
23.
Macedo, H. D., Rasmussen, M. B., Thule, C., and Larsen,
P. G. (2020). Migrating the into-cps application to
the cloud. In Sekerinski, E., Moreira, N., Oliveira,
J. N., Ratiu, D., Guidotti, R., Farrell, M., Luckcuck,
M., Marmsoler, D., Campos, J., Astarte, T., Gonnord,
L., Cerone, A., Couto, L., Dongol, B., Kutrib, M.,
Monteiro, P., and Delmas, D., editors, Formal Meth-
ods. FM 2019 International Workshops, pages 254–
271, Cham. Springer International Publishing.
Macedo, H. D., Sassanelli, C., Larsen, P. G., and Terzi,
S. (2021). Facilitating model-based design of cyber-
manufacturing systems. To appear in the proceedings
of the 54th CIRP Conference on Manufacturing Sys-
tems.
Porter, M. E. and Heppelmann, J. E. (2014). How
smart, connected products are transforming competi-
tion. Harvard business review, 92(11):64–88.
Rask, J. K., Madsen, F. P., Battle, N., Macedo, H. D., and
Larsen, P. G. (2020). Visual Studio Code VDM Sup-
port. In Fitzgerald, J. S. and Oda, T., editors, Pro-
ceedings of the 18th International Overture Workshop,
pages 35–49. Overture.
Rask, J. K., Madsen, F. P., Battle, N., Macedo, H. D., and
Larsen, P. G. (2021). The Specification Language
Server Protocol: A Proposal for Standardised LSP
Extensions. In Proenc¸a, J. and Paskevich, A., edi-
tors, Proceedings of the 6th Workshop on Formal In-
tegrated Development Environment, Held online, 24-
25th May 2021, volume 338 of Electronic Proceed-
Manufacturing Process Simulation in a Hybrid Cloud Setup
57