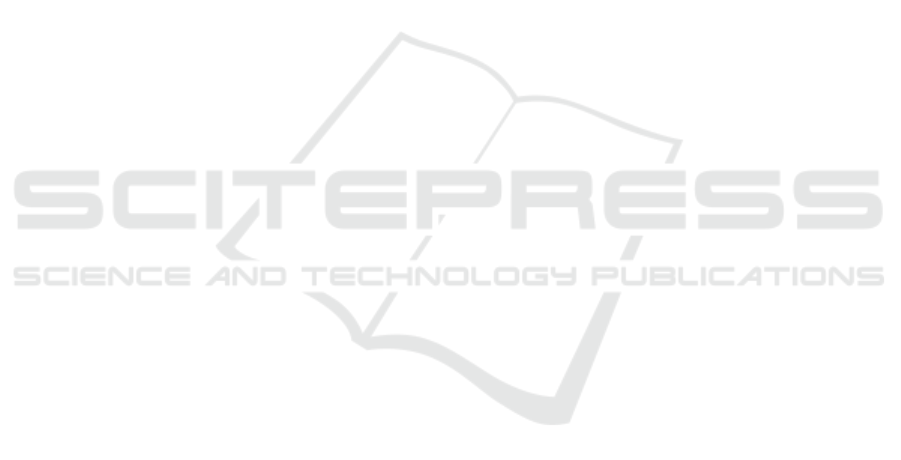
perception-driven autonomy with modular robots. Sci-
ence Robotics, 3(23).
Garrido-Jurado, S., Munoz-Salinas, R., Madrid-Cuevas,
F. J., and Medina-Carnicer, R. (2016). Generation of
fiducial marker dictionaries using mixed integer linear
programming. Pattern Recognition, 51:481–491.
Hornung, A., Wurm, K. M., Bennewitz, M., Stachniss,
C., and Burgard, W. (2013). OctoMap: An effi-
cient probabilistic 3D mapping framework based on
octrees. Autonomous Robots. Software available at
http://octomap.github.com.
Jain, K. P. and Mueller, M. W. (2020). Flying batter-
ies: In-flight battery switching to increase multirotor
flight time. In 2020 IEEE International Conference on
Robotics and Automation (ICRA), pages 3510–3516.
IEEE.
Jain, K. P., Park, M., and Mueller, M. W. (2020). Docking
two multirotors in midair using relative vision mea-
surements. arXiv preprint arXiv:2011.05565.
Kamel, M., Burri, M., and Siegwart, R. (2016). Linear
vs Nonlinear MPC for Trajectory Tracking Applied to
Rotary Wing Micro Aerial Vehicles. ArXiv e-prints.
Kamel, M., Stastny, T., Alexis, K., and Siegwart, R. (2017).
Model predictive control for trajectory tracking of un-
manned aerial vehicles using robot operating system.
In Koubaa, A., editor, Robot Operating System (ROS)
The Complete Reference, Volume 2. Springer.
Lee, T., Leok, M., and McClamroch, N. H. (2010). Geo-
metric tracking control of a quadrotor uav on se (3). In
49th IEEE conference on decision and control (CDC),
pages 5420–5425. IEEE.
Lin, Y., Gao, F., Qin, T., Gao, W., Liu, T., Wu, W., Yang,
Z., and Shen, S. (2018). Autonomous aerial naviga-
tion using monocular visual-inertial fusion. Journal
of Field Robotics, 35(1):23–51.
Lin, Y.-C., Cheng, Y.-T., Zhou, T., Ravi, R., Hasheminasab,
S. M., Flatt, J. E., Troy, C., and Habib, A. (2019).
Evaluation of uav lidar for mapping coastal environ-
ments. Remote Sensing, 11(24):2893.
Loianno, G., Spurny, V., Thomas, J., Baca, T., Thakur, D.,
Hert, D., Penicka, R., Krajnik, T., Zhou, A., Cho, A.,
et al. (2018). Localization, grasping, and transporta-
tion of magnetic objects by a team of mavs in chal-
lenging desert-like environments. IEEE Robotics and
Automation Letters, 3(3):1576–1583.
Lutz, P., M
¨
uller, M. G., Maier, M., Stoneman, S., Tomi
´
c, T.,
von Bargen, I., Schuster, M. J., Steidle, F., Wedler,
A., St
¨
urzl, W., et al. (2020). Ardea—an mav with
skills for future planetary missions. Journal of Field
Robotics, 37(4):515–551.
Narv
´
aez, E., Ravankar, A. A., Ravankar, A., Emaru, T., and
Kobayashi, Y. (2020). Autonomous vtol-uav dock-
ing system for heterogeneous multirobot team. IEEE
Transactions on Instrumentation and Measurement,
70:1–18.
Narv
´
aez, E., Ravankar, A. A., Ravankar, A., Kobayashi,
Y., and Emaru, T. (2017). Vision based autonomous
docking of vtol uav using a mobile robot manipula-
tor. In 2017 IEEE/SICE International Symposium on
System Integration (SII), pages 157–163. IEEE.
Peng, K., Du, J., Lu, F., Sun, Q., Dong, Y., Zhou, P., and
Hu, M. (2019). A hybrid genetic algorithm on routing
and scheduling for vehicle-assisted multi-drone parcel
delivery. IEEE Access, 7:49191–49200.
Perez-Grau, F. J., Caballero, F., Merino, L., and Viguria,
A. (2017). Multi-modal mapping and localization
of unmanned aerial robots based on ultra-wideband
and rgb-d sensing. In 2017 IEEE/RSJ International
Conference on Intelligent Robots and Systems (IROS),
pages 3495–3502. IEEE.
Qin, T., Li, P., and Shen, S. (2018). Vins-mono: A robust
and versatile monocular visual-inertial state estimator.
IEEE Transactions on Robotics, 34(4):1004–1020.
Qin, T. and Shen, S. (2018). Online temporal calibration for
monocular visual-inertial systems. In 2018 IEEE/RSJ
International Conference on Intelligent Robots and
Systems (IROS), pages 3662–3669. IEEE.
Rocha, R. and Robinson, S. K. (2020). Toward autonomous
in-flight docking of unmanned multi-rotor aerial vehi-
cles. In AIAA Scitech 2020 Forum, page 1486.
Romero-Ramire, F. J., Munoz-Salinas, R., and Medina-
Carnicer, R. (2019). Fractal markers: a new approach
for long-range marker pose estimation under occlu-
sion. IEEE Access, 7:169908–169919.
Romero-Ramirez, F. J., Mu
˜
noz-Salinas, R., and Medina-
Carnicer, R. (2018). Speeded up detection of squared
fiducial markers. Image and vision Computing,
76:38–47.
Sa, I., Kamel, M., Khanna, R., Popovi
´
c, M., Nieto, J., and
Siegwart, R. (2018). Dynamic system identification,
and control for a cost-effective and open-source multi-
rotor mav. In Field and Service Robotics, pages 605–
620. Springer.
Sani, M. F. and Karimian, G. (2017). Automatic naviga-
tion and landing of an indoor ar. drone quadrotor us-
ing aruco marker and inertial sensors. In 2017 interna-
tional conference on computer and drone applications
(IConDA), pages 102–107. IEEE.
Tzoumanikas, D., Li, W., Grimm, M., Zhang, K., Kovac,
M., and Leutenegger, S. (2019). Fully autonomous
micro air vehicle flight and landing on a moving target
using visual–inertial estimation and model-predictive
control. Journal of Field Robotics, 36(1):49–77.
Ullah, N., Mehmood, Y., Aslam, J., Ali, A., and Iqbal, J.
(2021). Uavs-ugv leader follower formation using
adaptive non-singular terminal super twisting sliding
mode control. IEEE Access, 9:74385–74405.
Wasim, M., Ullah, M., and Iqbal, J. (2019). Gain-scheduled
proportional integral derivative control of taxi model
of unmanned aerial vehicles. Revue Roumaine des
Sciences Techniques-Serie Electrotechnique et Ener-
getique, 64(1):75–80.
Yang, S., Scherer, S. A., Schauwecker, K., and Zell, A.
(2014). Autonomous landing of mavs on an arbitrarily
textured landing site using onboard monocular vision.
Journal of Intelligent & Robotic Systems, 74(1):27–
43.
Yu, C., Cai, J., and Chen, Q. (2017). Multi-resolution visual
fiducial and assistant navigation system for unmanned
An Unmanned Aerial Carrier and Anchoring Mechanism for Transporting Companion UAVs
111