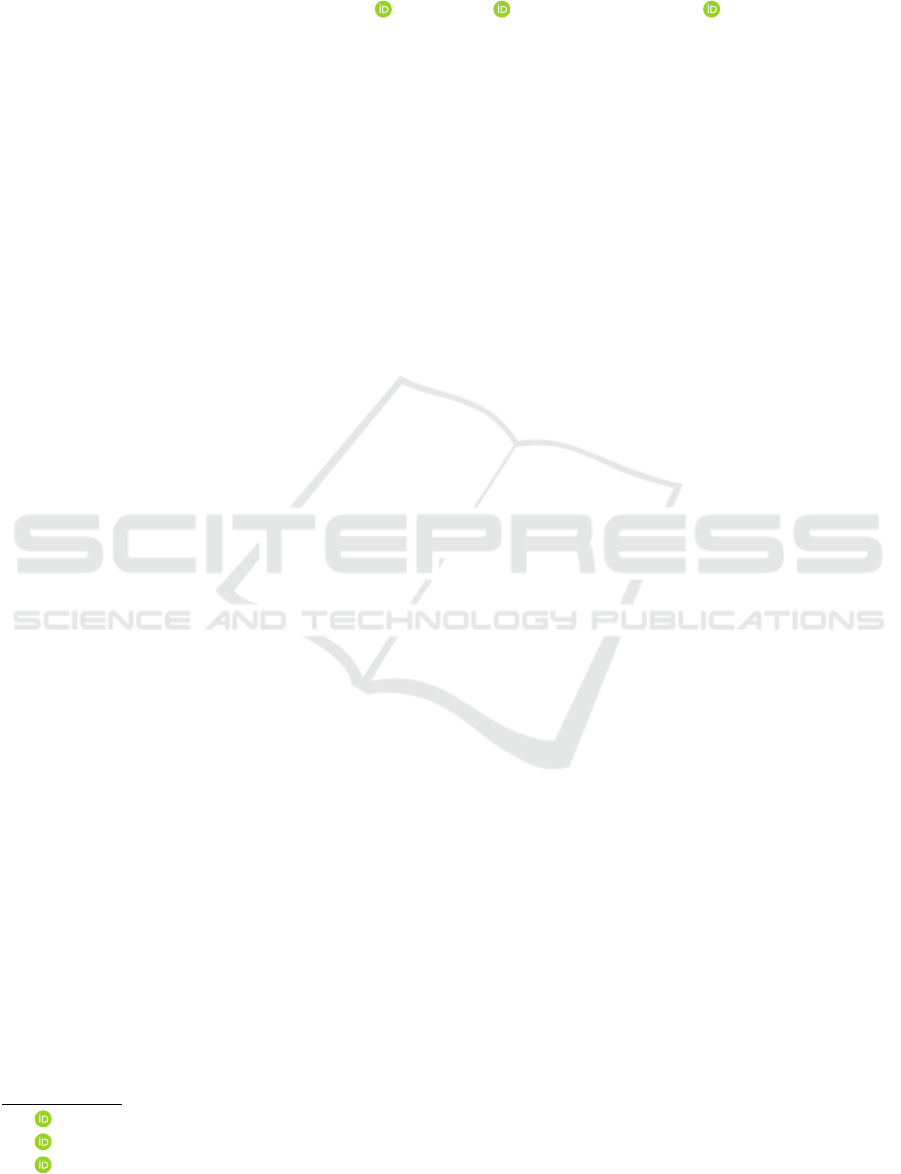
Touch Detection with Low-cost Visual-based Sensor
Julio Casta
˜
no-Amoros
a
, Pablo Gil
b
and Santiago Puente
c
AUROVA Lab, Computer Science Research Institute, University of Alicante, Alicante 03690, Spain
Keywords:
Tactile Sensing, Robotic Grasping, DIGIT Sensor, Convolutional Neural Networks.
Abstract:
Robotic manipulation continues being an unsolved problem. It involves many complex aspects, for example,
perception tactile of different objects and materials, grasping control to plan the robotic hand pose, etc. Most
of previous works on this topic used expensive sensors. This fact makes difficult the application in the industry.
In this work, we propose a grip detection system using a low-cost visual-based tactile sensor known as DIGIT,
mounted on a ROBOTIQ gripper 2F-140. We proved that a Deep Convolutional Network is able to detect
contact or no contact. Capturing almost 12000 images with contact and no contact from different objects, we
achieve 99% accuracy with never seen samples, in the best scenario. As a result, this system will allow us to
implement a grasping controller for the gripper.
1 INTRODUCTION
Tactile perception is becoming more and more essen-
tial in robotic manipulation tasks as shown in (Kap-
passov et al., 2015) and (Li et al., 2020). Touch data
are often used to obtain information about manipu-
lated objects such as shape, rigidity or texture of the
material (Luo et al., 2017). This can be used for ob-
ject recognition tasks, when visual information from
eye-to-hand systems is not sufficient for a successful
recognition.
Besides, touch data can be used to adapt the ob-
ject grasping by correcting the opening or closing of
the robotic hand or gripper (Delgado Rodr
´
ıguez et al.,
2017). Sometimes, it is used to plan finger move-
ments in order to ensure a better grasp (Calandra et al.,
2018), avoiding slipping or falling of the manipulated
objects.
With the aim of controlling the gripper opening,
or making a stable grasp with a robotic hand, state of
art works showed methods based on machine learn-
ing techniques (Cockbum et al., 2017) and (Bekiroglu
et al., 2011). Later, other methods used deep learning
techniques (Kwiatkowski et al., 2017) and (Ni et al.,
2019). Both types of approaches rely on the tactile
sensor technology. A review of tactile technologies
can be found in (Yi et al., 2018). They can be piezo-
resistive, capacitive, optical, magnetic, with baromet-
a
https://orcid.org/0000-0001-9789-1628
b
https://orcid.org/0000-0001-9288-0161
c
https://orcid.org/0000-0002-6175-600X
ric transducers, etc. Therefore, the neural architec-
tures proposed to solve this problem are very differ-
ent. For example, in (Zapata-Impata et al., 2018), a
simple Convolutional Neural Network (CNN) is de-
signed to detect stability in a virtual tactile image
created from the electrode values of a BioTac sensor
SP. This virtual tactile image was used to represent
the connectivity among neighboring electrodes. In
(Garcia-Garcia et al., 2019), a Graph Convolutional
Network (GCN) was created to avoid building an in-
termediate representation like a virtual tactile image.
GCN also keeps the connectivity among neighbors.
The results of both methodologies were compared in
(Zapata-Impata et al., 2019).
In this work, we present a first approach for the
detection of tactile contact between the robot and ob-
ject. We plan to use it as a part of a controller that al-
lows the robot to manipulate an object in-hand with-
out slipping. To do this, we used a novel low-cost
visual-based tactile sensor known as DIGIT (Lambeta
et al., 2020), instead of BioTac SP. DIGIT is based on
an optical image whereas BioTac SP is based on baro-
metric transducers, and is much more expensive.
This paper is organised as follows: first, we will
describe the robotic grasping system consisting of
a gripper with DIGIT tactile sensors mounted on
the parallel fingertips. Second, we will present our
methodology for contact detection with DIGIT sen-
sor and artificial intelligence. Finally, we will show
our results and conclusions, as well as future works.
136
Castaño-Amoros, J., Gil, P. and Puente, S.
Touch Detection with Low-cost Visual-based Sensor.
DOI: 10.5220/0010699800003061
In Proceedings of the 2nd International Conference on Robotics, Computer Vision and Intelligent Systems (ROBOVIS 2021), pages 136-142
ISBN: 978-989-758-537-1
Copyright
c
2021 by SCITEPRESS – Science and Technology Publications, Lda. All rights reserved