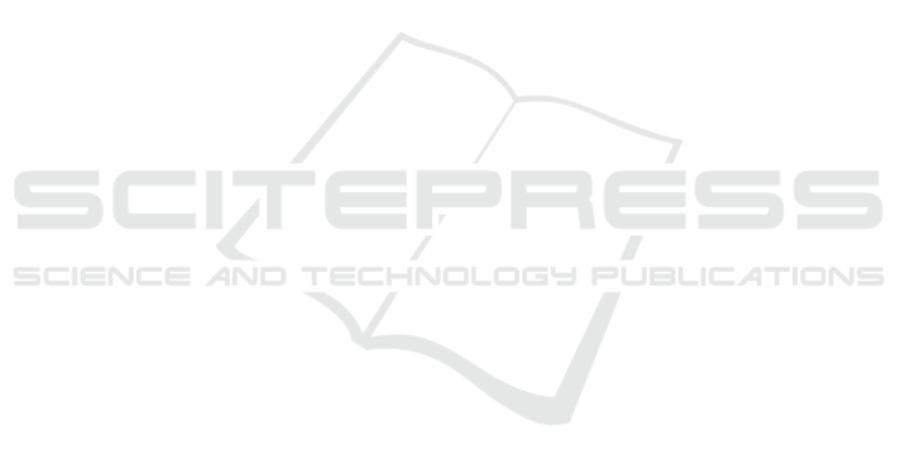
Robots and Systems, pp. 307-314, Nov. 2013, doi:
10.1109/IROS.2013.6696369.
D. Sun, Y.H. Liu, Position and force tracking of a two-
manipulator system manipulating a flexible beam, J.
Robot. Syst., vol. 18, no. 4, pp. 197-212, March 2001.
S. Hirai, T. Wada, Indirect simultaneous positioning of de-
formable objects with multi-pinching fingers based on
an uncertain model, Robotica, vol. 18, no. 1, pp. 3–11,
Jan. 2000, doi: 10.1017/S0263574799002362.
A. Tavasoli, M. Eghtesad, and H. Jafarian, Two-time
scale control and observer design for trajectory track-
ing of two cooperating robot manipulators mov-
ing a fexible beam, Robotics and Autonomous
Systems, vol. 57, no. 2, pp. 212 - 221, 2009,
https://doi.org/10.1016/j.robot.2008.04.003.
J. Smolen and A. Patriciu, Deformation Planning for
Robotic Soft Tissue Manipulation, in 2009 Second
International Conferences on Advances in Computer-
Human Interactions, pp. 199–204, Feb. 2009.
T. Wada, S. Hirai, S. Kawarnura, and N. Karniji, Robust
manipulation of deformable objects by a simple PID
feedback, in Proc. IEEE International Conference on
Robotics and Automation (ICRA), pp. 85–90, 2001.
D. Navarro-Alarcon et al., Automatic 3-D Manipulation
of Soft Objects by Robotic Arms With an Adap-
tive Deformation Model, in IEEE Transactions on
Robotics, vol. 32, no. 2, pp. 429-441, April 2016, doi
: 10.1109/TRO.2016.2533639
D. Berenson, Manipulation of deformable objects with-
out modeling and simulating deformation, 2013
IEEE/RSJ International Conference on Intelligent
Robots and Systems, Tokyo, pp. 4525-4532, 2013.
doi: 10.1109/IROS.2013.6697007.
B. Jia, Z. Hu, J. Pan and D. Manocha, Manipulating
Highly Deformable Materials Using a Visual Feed-
back Dictionary, 2018 IEEE International Conference
on Robotics and Automation (ICRA), Brisbane, QLD,
pp. 239-246, 2018. doi: 10.1109/ICRA.2018.8461264
F. Bertelsmeier, T. Detert, T.
¨
Ubelh
¨
or, R. Schmitt and
B. Corves, Cooperating Robot Force Control for Posi-
tioning and Untwisting of Thin Walled Components,
Advances in Robotics and Automation, vol. 3, no. 6,
Nov. 2017, doi: 10.4172/2168-9695.1000179.
A.S. Al-Yahmadi, and T.C. Hsia, Modeling and Control of
Two Manipulators handling a Flexible Beam, Interna-
tional Journal of Electrical and Computer Engineer-
ing, vol. 1, no. 6, pp. 934-937, Nov. 2007.
S. Garrido-Jurado, R. Mu
˜
noz-Salinas, F.J. Madrid-Cuevas,
and M.J. Mar
`
ın-Jim
´
enez. 2014. Automatic generation
and detection of highly reliable fiducial markers under
occlusion. Pattern Recogn. vol. 47, no. 6, pp. 2280-
2292, June 2014. DOI=10.1016/j.patcog.2014.01.005
S. Caro, N. Binaud, and P. Wenger, Sensitivity Analy-
sis of 3-RPR Planar Parallel Manipulators, ASME
Journal of Mechanical Design, vol. 131, pp. 121005-
1–121005-13, 2009.
S. Miller et al., Technical Paper at Mathworks, Modeling
Flexible Bodies with Simscape Multibody Software,
2006.
F. Chaumette, P. Rives, and B. Espiau, Positioning of a
robot with respect to an object, tracking it and esti-
mating its velocity by visual servoing, Proceedings.
1991 IEEE International Conference on Robotics and
Automation, Sacramento, CA, USA, vol. 3, pp. 2248-
2253, 1991.
Z. Zake, F. Chaumette, N. Pedemonte, and S. Caro, Vision-
Based Control and Stability Analysis of a Cable-
Driven Parallel Robot, in the IEEE Robotics and Au-
tomation Letters (RA-L), vol. 4, no. 2, pp. 1029-1036,
2019
Z. Zake, S. Caro, A.S. Roos, F. Chaumette and N. Pede-
monte, Stability Analysis of Pose-Based Visual Servo-
ing Control of Cable-Driven Parallel Robots. In: Pott
A., Bruckmann T. (eds) Cable-Driven Parallel Robots.
CableCon 2019. Mechanisms and Machine Science,
vol. 74. Springer, Cham.
A. Sintov, S. Macenski, A. Borum, T. Bretl, Motion Plan-
ning for Dual-Arm Manipulation of Elastic Rods.
IEEE Robotics and Automation Letters, vol. 5, N° 4,
October 2020.
T. Bretl, Z. McCarthy, ”Quasi-static manipulation of a
Kirchhoff elastic rod based on a geometric analysis of
equilibrium configurations”, Int. J. Robot. Res., vol.
33, no. 1, pp. 48-68, 2014.
R. Lagneau, A. Krupa and M. Marchal, Automatic Shape
Control of Deformable Wires based on Model-
Free Visual Servoing. IEEE Robotics and Automa-
tion Letters, IEEE 2020, 5 (4), pp. 5252-5259.
10.1109/LRA.2020.3007114
ROBOVIS 2021 - 2nd International Conference on Robotics, Computer Vision and Intelligent Systems
56