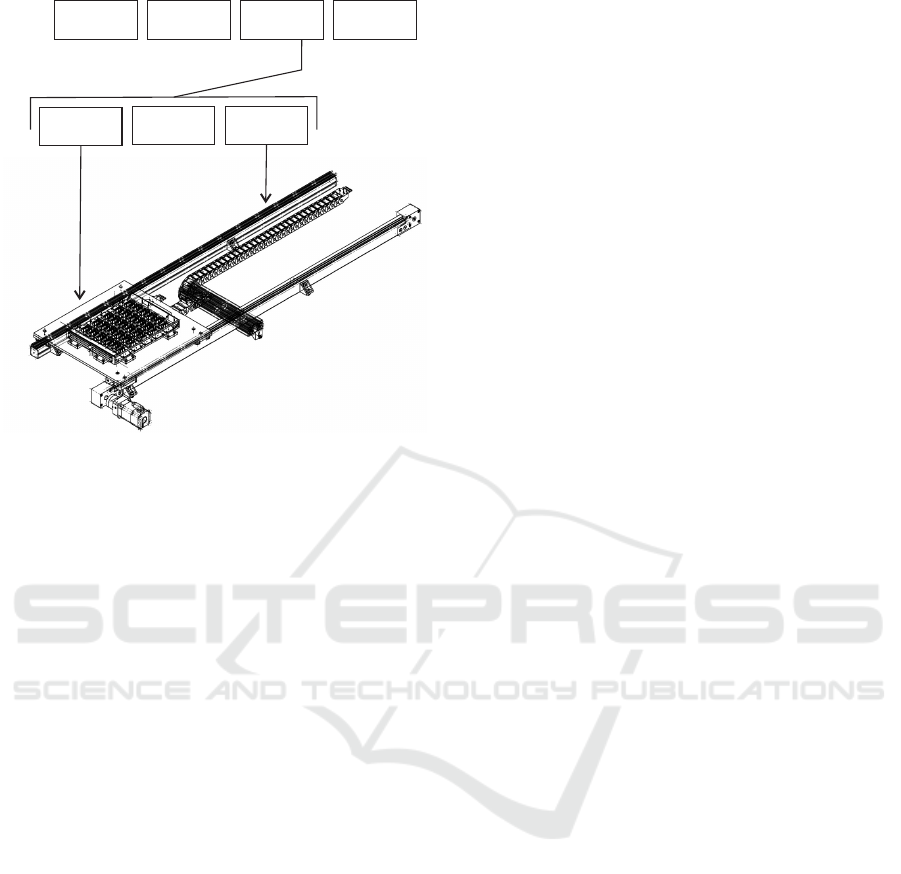
* excerpt
Bring-/
Pick up
Pallet
handling
Pallet
delivery
Sor!ng
Pallet
fixing
Posi!oning
unit
Pallet
carrier
Figure 3: Subscheme - pallet delivery (excerpt).
In the use case, the functions have already been
encapsulated on the PLC, so that the functions are
used as assets on the AAS. All abilities or groupings
of abilities are also to be synchronized at the AAS
level. For this purpose, a Pack ML state machine is
to be established for each controller and process or
subprocess. In the case that several subprocesses are
implemented on one controller, an additional higher-
level Pack ML state machine is used.
3 APPROACH
3.1 Existing Plant & Asset
Administration Shells
In order to successfully convert a plant into an I4.0-
based solution, the plant description and the programs
used must be documented in a proper manner. In the
use case, the project planning of the existing plant was
carried out with PLCs, which were programmed with
domain-specific programming languages such as IEC
61131-3. The ”Codesys” platform was used, which is
popular and is based on a PLCopen compliant notation.
In this platform, a large number of libraries and vari-
ous communication protocols can be used. (Rayment,
2004) However, there are still no solutions that allow
easy integration into an I4.0 environment via Asset
Administration shells (AAS).
The challenge is the effort-reduced realization of
Digital Twins (Koulamas and Kalogeras, 2018) as I4.0
components. These can be designed as Asset Adminis-
tration shells (AAS). AASs can be separated into three
types based on a unified information metamodel. (Bun-
desministerium f
¨
ur Wirtschaft und Energie (BMWi),
2020) Type 1 AAS represents a passive AAS, which
consists of an asset description. Type 2 AAS repre-
sents a reactive AAS, which in addition to the asset
description, also contains a communication channel.
Only Type 3 AAS is a proactive AAS and is capable of
independently communicating with other AAS. Sub-
model templates are provided for modeling frequently
used asset aspects. They are equivalent to the profiles
for fieldbuses.
One tool for the description of AAS is the AASX
Package Explorer. (Belyaev et al., 2021) This enables
a structured description to be implemented using sub-
models and other structural elements. The AASX Pack-
age Explorer supports extensive export/import func-
tions. The entire asset descriptions or individual sub-
models can be exported for further processing in an
XML or JSON format, and node sets for the assets can
be imported. Detailed and further information can be
found on the AASX Package Explorer GitHub website.
(Github Repository - AASX Package Explorer, 2021)
3.2 Challenge
The SDK BaSyx 4.2 (Eclipse BaSyx Platform, 2021)
was used in the project to implement the representa-
tive. It offers the possibility of implementing AAS in
different programming environments (Java, C++, C#).
AASs can be configured manually by using SDK
according to the general description of the structure
and its submodels in the C#. However, this means that
an IT expert has to take over the engineering sector
in the company. In many cases, however, appropriate
employees with the required knowledge are not avail-
able in the company. However, automation engineers
are already employed for the existing machinery and
equipment, who are responsible for the support of the
plant. Their knowledge and skills can be drawn upon
with regard to the design of solutions.
The mentioned method of manual project engineer-
ing of AAS is established and will not be considered
further. The question arises of how the user of indus-
trial control is enabled to use AAS in the industrial
environment. A solution is the generic preparation of
AAS without knowledge of the SDK. For this, only the
description of the Type 1 AAS asset and the modifica-
tion of the PLC program should be as requirements.
In the research project ”OpenBasys 4.0” (Bun-
desministerium f
¨
ur Bildung und Forschung (BMBF),
2019), an environment for generic generation of AAS
was implemented. Type 2 AAS can be implemented
in this environment without knowledge of the SDK.
Design and Deployment of Digital Twins for Programmable Logic Controllers in Existing Plants
147