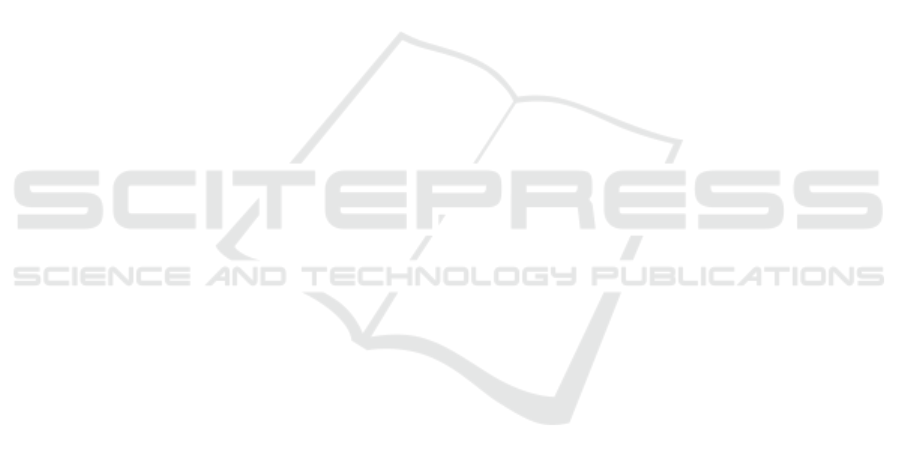
that supports the collaborative execution of produc-
tion processes introduced in this paper will be sys-
tematically evaluated and tested on a case study com-
mon for VOs with a non-hierarchical structure. Fur-
thermore, we plan to improve the possibilities of CE-
MultiProLan for modeling collaborative production
processes by expanding the set of concepts available
on the interface process level. For example, advanced
concepts already present on the private process level,
like sub-processes and unordered steps, should also
be available on the interface level. The support for
the newly introduced concepts should also be imple-
mented in the software that generates smart contracts.
In addition, we plan to investigate the possibility of
utilizing enterprise modeling constructs defined in the
newly introduced ISO standard for Enterprise Mod-
elling and Architecture (ISO 19440:2020, 2020). This
standard focuses on engineering and the integration of
manufacturing and related services in the enterprise.
We plan to analyze the possibility of using those con-
structs for production process modeling. Even though
the standard is rather new, there have already been at-
tempts to utilize it in the production modeling context.
For example, authors in (Wu et al., 2021) utilize it for
extracting object classes for a meta-model used to de-
scribe Cyber-Physical Production Systems(CPPS).
Even though our solution introduces a tamper-
proof and immutable way for storing production data,
the issue of when a malicious partner tries to submit
incorrect data about process execution persists. Al-
though the production process automation somewhat
mitigates this issue by decreasing the space for man-
ual data input, there is still a real possibility that a ma-
licious collaboration partner could try to submit the
wrong data. For this reason, we plan to investigate the
possibility of detecting such behavior with a compo-
nent that would perform smart contract execution log
analysis. As a part of this investigation, we published
a paper that expands further on the topic of finding
discrepancies between contracted and executed pro-
duction processes (Ivkovi
´
c and Lukovi
´
c, 2021).
The expected value of our approach for parties in-
volved in a VO is increased structural transparency
during the enactment of collaboration as contracts are
automated and tamper-proof. In addition, the ex-
pected scientific implication is a novel methodolog-
ical approach for the integration of VO participant’s
information systems that would create conditions for
trustworthy and traceable production execution.
ACKNOWLEDGEMENTS
This paper is supported by the Ministry of Education,
Science and Technological Development through the
project no. 451-03-68/2020-14/200156: “Innovative
scientific and artistic research from the FTS domain”.
REFERENCES
Eclipse sirius documentation. https://www.eclipse.
org/sirius/doc/. Accessed: 2021-07-29.
Berre, A. J., Elvesæter, B., Figay, N., Guglielmina, C.,
Johnsen, S. G., Karlsen, D., Knothe, T., and Lippe,
S. (2007). The athena interoperability framework. In
Enterprise Interoperability II, pages 569–580.
Carneiro, L., Shamsuzzoha, A., Almeida, R., Azevedo, A.,
Fornasiero, R., and Ferreira, P. S. (2014). Reference
model for collaborative manufacturing of customised
products: applications in the fashion industry. Pro-
duction Planning & Control, 25(13-14):1135–1155.
Carneiro, L. M., Almeida, R., Azevedo, A. L., Kankaanpaa,
T., and Shamsuzzoha, A. H. M. (2010). An Innovative
Framework Supporting SME Networks for Complex
Product Manufacturing. In Collaborative Networks
for a Sustainable World, volume 336.
Chen, D. and Doumeingts, G. (2003). European initia-
tives to develop interoperability of enterprise applica-
tions—basic concepts, framework and roadmap. An-
nual Reviews in Control, 27(2):153–162.
Chowdhury, M. J. M., Ferdous, M. S., Biswas, K., Chowd-
hury, N., Kayes, A. S. M., Alazab, M., and Wat-
ters, P. (2019). A Comparative Analysis of Dis-
tributed Ledger Technology Platforms. IEEE Access,
7:167930–167943. Conference Name: IEEE Access.
France, R. and Rumpe, B. (2007). Model-driven Devel-
opment of Complex Software: A Research Roadmap.
In Future of Software Engineering (FOSE ’07), pages
37–54.
Gorenflo, C., Lee, S., Golab, L., and Keshav, S. (2019).
FastFabric: Scaling Hyperledger Fabric to 20,000
Transactions per Second. arXiv:1901.00910 [cs].
arXiv: 1901.00910.
Hileman, G. and Rauchs, M. (2017). 2017 Global
Blockchain Benchmarking Study. SSRN Electronic
Journal.
ISO 19440:2020 (2020). Enterprise modelling and architec-
ture — constructs for enterprise modelling. Standard,
International Organization for Standardization.
Ivkovi
´
c, V. and Lukovi
´
c, I. (2021). An approach to vali-
dation of business-oriented smart contracts based on
process mining. Bellatreche L. et al. (eds) New Trends
in Database and Information Systems. ADBIS 2021.
Communications in Computer and Information Sci-
ence, 1450:303–309.
Klinger, P. and Bodendorf, F. (2020). Blockchain-based
Cross-Organizational Execution Framework for Dy-
namic Integration of Process Collaborations. In
WI2020 Zentrale Tracks, pages 893–908.
A Novel Approach and a Language for Facilitating Collaborative Production Processes in Virtual Organizations Based on DLT Networks
207