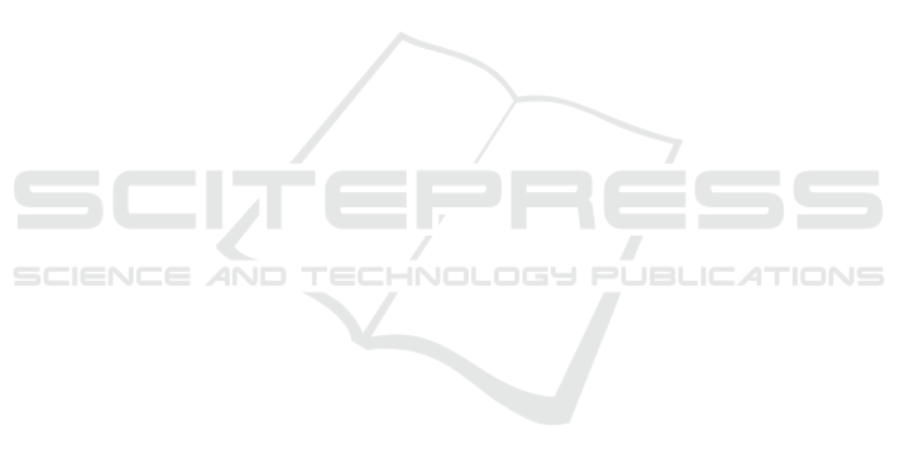
ence on Automation Science and Engineering (CASE),
197:Taipei, Taiwan.
Graham, R.-L., Lawler, E.-L., Lenstra, J.-K., and Kan, A.-
R. (1979). Optimization and approximation in deter-
ministic sequencing and scheduling: a survey. Annals
of discrete mathematics, 5:287–326.
Ham, A. (2020). ransfer-robot task scheduling in job shop.
International Journal of Production Research, DOI:
10.1080/00207543.2019.1709671.
Hauder, V.-A., Beham, A., Raggl, S., Parraghb, S.-N., and
Affenzeller, M. (2020). Resource-constrained multi-
project scheduling with activity and time fexibility.
IComputers and Industrial Engineering.
J. Kinable, W.-J. v. H. and Smith, S.-F. (2021). Snow
plow route optimization: A constraint programming
approach. IISE Transactions, 53:6:685–703.
Kan, A.-R. (1976). Machine scheduling problems: classifi-
cation, complexity and computations. Springer.
Kress, D. and M
¨
uller, D. (2019). Shop scheduling problem
with machine operator constraints. IFAC PapersOn-
Line, pages 94–99.
Laborie, P. (2009). Ibm ilog cp optimizer for de-
tailed scheduling illustrated on three prob-
lems. Lecture Notes in Computer Science,
https://doi.org/10.1007/978-3-642-01929-6-12.
Laborie, P., Rogerie, J., Shaw, P., and Vilim, P. (2018).
Ibm ilog cp optimizer for scheduling: 20+ years of
scheduling with constraints at ibm/ilog. Constraints,
https://doi.org/10.1007/s10601-018-9281-x.
Lee, C.-Y. and Liman, S.-D. (1992). Single machine flow-
time scheduling with scheduled maintenance. Acta In-
formatica, 29:375–382.
Liu, M., Wang, S., Chu, C., and Chu, F. (2015). An im-
proved exact algorithm for single-machine scheduling
to minimise the number of tardy jobs with periodic
maintenance. International Journal of Production Re-
search, DOI:10.1080/00207543.2015.1108535.
Low, C., Ji, M., Hsu, C.-J., and Su, C.-T. (2010). Mini-
mizing the makespan in a single machine scheduling
problems with flexible and periodic maintenance. Ap-
plied Mathematical Modelling, 34:334–342.
Lunardi, W.-T., Birgin, E.-G., Laborie, P., Ronconi,
D.-P., and Voos, H. (2020). Mixed integer lin-
ear programming and constraint programming mod-
els for the online printing shop scheduling prob-
lem. Optimization and Control (math.OC), DOI:
10.1016/j.cor.2020.105020.
Luo, A., Cheng, T.-C.-E., and Ji, M. (2015). Single-
machine scheduling with a variable maintenance ac-
tivity wenchang. Computers and Industrial Engineer-
ing, 79:168–174.
Mashkani, O. and Moslehi, G. (2016). Minimising the total
completion time in a single machine scheduling prob-
lem under bimodal flexible periodic availability con-
straints. International Journal of Computer Integrated
Manufacturing, 29:323–341.
Mokhtarzadeh, M., Tavakkoli-Moghaddam, R., Vahedi-
Nouri, B., and Farsi, A. (2020). Scheduling of
human-robot collaboration in assembly of printed cir-
cuit boards: a constraint programming approach. In-
ternational Journal of Computer Integrated Manufac-
turing, DOI: 10.1080/0951192X.2020.1736713.
Ornek, M.-A., Ozturk, C., and Sugut, I. (2020). Inte-
ger and constraint programming model formulations
for flight-gate assignment problem. Operational Re-
search, https://doi.org/10.1007/s12351-020-00563-9.
Polo-Mej
´
ıa, O., Artigues, C., Lopez, P., and Basini, V.
(2019). Mixed-integer/linear and constraint program-
ming approaches for activity scheduling in a nuclear
research facility. International Journal of Production
Research, DOI:10.1080/00207543.2019.1693654.
Qin, T., Du, Y., Chen, J.-H., and Sha, M. (2020). Combining
mixed integer programming and constraint program-
ming to solve the integrate d scheduling problem of
container handling operations of a single vessel. Euro-
pean Journal of Operational Research, 285:884–901.
Touat, M., Benbouzid, F., and Benhamou, B. (2021). Exact
and metaheuristic approaches for the single-machine
scheduling problem with flexible maintenance under
human resource constraints. International Journal of
Manufacturing Research.
Touat, M., Bouzidi-Hassini, S., Benbouzid-Sitayeb, F., and
Benhamou, B. (2017). A hybridization of genetic
algorithms and fuzzy logic for the single-machine
scheduling with flexible maintenance problem under
human resource constraints. Applied Soft Computing,
59:556–573.
Touat, M., Tayeb, F. B.-S., and Benhamou, B. (2018).
An effective heuristic for the single-machine schedul-
ing problem with flexible maintenance under human
resource constraints. Procedia Computer Science,
126:1395–1404.
Yang, S.-L., Maa, Y., Xu, D.-L., and Yang, J.-B. (2011).
Minimizing total completion time on a single machine
with a flexible maintenance activity. Computers and
Operations Research, 38:755–770.
Yazdani, M., Khalili, S.-M., Babagolzadeh, M., and Jolai,
F. (2017). A single-machine scheduling problem with
multiple unavailability constraints: A mathematical
model and an enhanced variable neighborhood search
approach. Journal of Computational Design and En-
gineering, 4:46–59.
Zammori, F., Braglia, M., and Castellano, D. (2014). Har-
mony search algorithm for single-machine scheduling
problem with planned maintenance. Computers I&
Industrial Engineering, 76:333–346.
ICAART 2022 - 14th International Conference on Agents and Artificial Intelligence
202