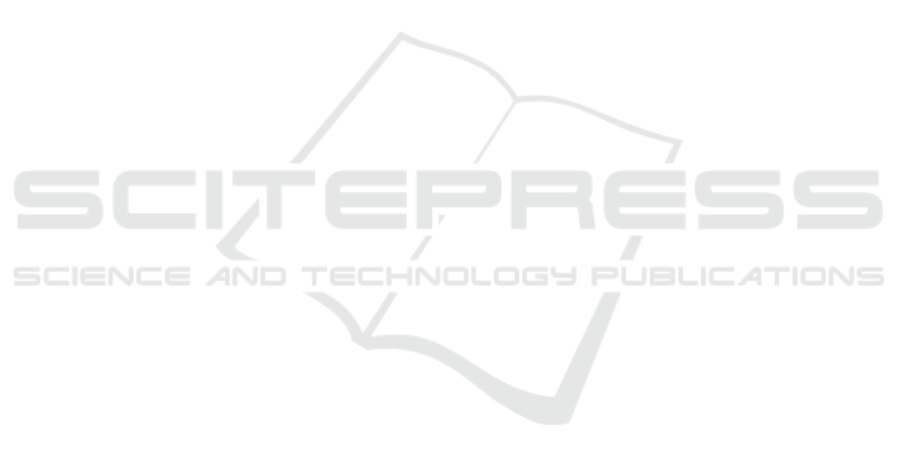
Barner, S., Diewald, A., Migge, J., Syed, A., Fohler, G.,
Faug
`
ere, M., and Gracia P
´
erez, D. (2017). DREAMS
Toolchain: Model-Driven Engineering of Mixed-
Criticality Systems. In Proceedings of the ACM/IEEE
20
th
International Conference on Model Driven En-
gineering Languages and Systems (MODELS ’17),
pages 259–269. IEEE.
Belmonte, F. and Soubiran, E. (2012). A model based ap-
proach for safety analysis. In Ortmeier, F. and Daniel,
P., editors, Computer Safety, Reliability, and Secu-
rity - SAFECOMP 2012 Workshops: Sassur, ASCoMS,
DESEC4LCCI, ERCIM/EWICS, IWDE, Magdeburg,
Germany, September 25-28, 2012. Proceedings, vol-
ume 7613 of Lecture Notes in Computer Science,
pages 50–63. Springer.
Biondi, A., Nesti, F., Cicero, G., Casini, D., and Buttazzo,
G. C. (2020). A safe, secure, and predictable soft-
ware architecture for deep learning in safety-critical
systems. IEEE Embed. Syst. Lett., 12(3):78–82.
Dantas, Y. G., Kondeva, A., and Nigam, V. (2020). Less
manual work for safety engineers: Towards an auto-
mated safety reasoning with safety patterns. In ICLP.
de Moura, L. M. and Bjørner, N. (2008). Z3: An Efficient
SMT Solver. In Ramakrishnan, C. R. and Rehof, J.,
editors, TACAS 2008, volume 4963 of Lecture Notes
in Computer Science, pages 337–340. Springer.
Douglass, B. P. (2012). Real-Time Design Patterns: Robust
Scalable Architecture for Real-Time Systems.
Eder, J., Bahya, A., Voss, S., Ipatiov, A., and Khalil, M.
(2018a). From deployment to platform exploration:
Automatic synthesis of distributed automotive hard-
ware architectures. In MODELS 2018, MODELS ’18,
page 438–446.
Eder, J., Bayha, A., Voss, S., Ipatiov, A., and Khalil,
M. (2018b). From deployment to platform explo-
ration: Automatic synthesis of distributed automo-
tive hardware architectures. In Wasowski, A., Paige,
R. F., and Haugen, Ø., editors, Proceedings of the
21th ACM/IEEE International Conference on Model
Driven Engineering Languages and Systems, MOD-
ELS 2018, pages 438–446. ACM.
Eder, J., Voss, S., Bayha, A., Ipatiov, A., and Khalil, M.
(2020). Hardware architecture exploration: automatic
exploration of distributed automotive hardware archi-
tectures. Software and Systems Modeling.
Eder, J., Zverlov, S., Voss, S., Khalil, M., and Ipatiov, A.
(2017). Bringing DSE to Life: Exploring the Design
Space of an Industrial Automotive Use Case. In MOD-
ELS 2017, pages 270–280. IEEE Computer Society.
EmbASP (2018). EmbASP. Available at https://www.
mat.unical.it/calimeri/projects/embasp/.
fortiss GmbH (2020). AutoFOCUS 2.19. Available at
https://www.fortiss.org/en/publications/software/
autofocus-3.
IEC61508 (2010). IEC 61508, Functional safety of
electrical/electronic/programmable electronic safe-
tyrelated systems – Part 7: Overview of tech-
niques and measures. Available at http://www.
cechina.cn/eletter/standard/safety/iec61508-7.pdf.
ISO26262 (2018). ISO 26262, road vehicles —
functional safety — part 6: Product de-
velopment: software level. Available at
https://www.iso.org/standard/43464.html.
Leone, N., Pfeifer, G., Faber, W., Eiter, T., Gottlob, G.,
Perri, S., and Scarcello, F. (2006). The DLV system
for knowledge representation and reasoning. ACM
Trans. Comput. Log., 7(3):499–562.
Martin, H., Ma, Z., Schmittner, C., Winkler, B., Kram-
mer, M., Schneider, D., Amorim, T., Macher, G., and
Kreiner, C. (2020). Combined automotive safety and
security pattern engineering approach. Reliab. Eng.
Syst. Saf., 198:106773.
Papadopoulos, Y., Walker, M., Parker, D., Ruede, E.,
Hamann, R., Uhlig, A., Graetz, U., and Lien, R.
(2011). Engineering failure analysis and design op-
timisation with HiP-HOPS. Journal of Engineering
Failure Analysis, 18(2):590–608.
Preschern, C., Kajtazovic, N., and Kreiner, C. (2013a).
Building a safety architecture pattern system. In van
Heesch, U. and Kohls, C., editors, Proceedings of the
18th European Conference on Pattern Languages of
Program, EuroPLoP 2013, pages 17:1–17:55. ACM.
Preschern, C., Kajtazovic, N., and Kreiner, C. (2013b). Se-
curity analysis of safety patterns. PLoP, pages 12:1–
12:38.
SAEJ3061 (2012). SAE J3061: Cybersecurity guidebook
for cyber-physical vehicle systems. Available from
https://www.sae.org/standards/content/j3061/.
Safety Pattern Synthesis (2021). Safety Pattern Synthe-
sis. Available at https://download.fortiss.org/ pub-
lic/MODELSWARD2022/SafetyPatternSynthesis.zip.
Sljivo, I., Uriagereka, G. J., Puri, S., and Gallina, B. (2020).
Guiding assurance of architectural design patterns for
critical applications. J. Syst. Archit., 110:101765.
A Model-based System Engineering Plugin for Safety Architecture Pattern Synthesis
47