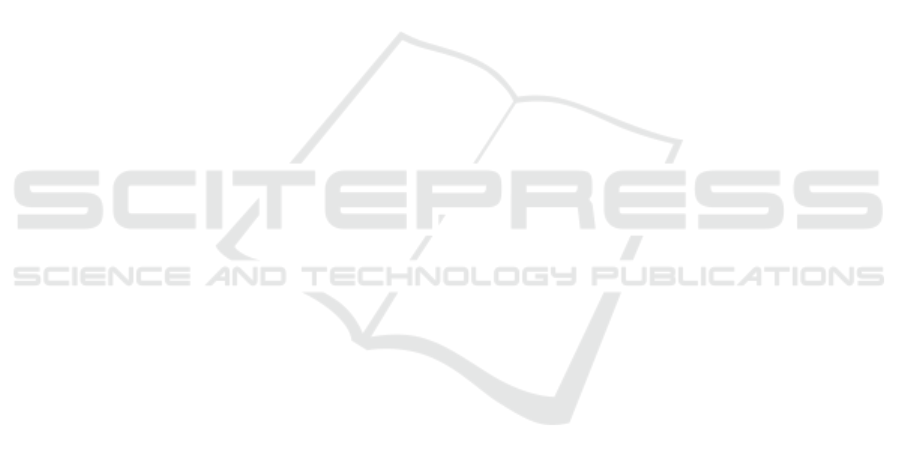
ACKNOWLEDGEMENTS
This work is funded by the ITEA3 project eXcellence
in Variant Testing (XIVT). See also https://itea4.org/
project/xivt.html.
REFERENCES
Awad, R., Heppner, G., Roennau, A., and Bordignon, M.
(2016). ROS engineering workbench based on seman-
tically enriched app models for improved reusabil-
ity. In 2016 IEEE 21st International Conference
on Emerging Technologies and Factory Automation
(ETFA), pages 1–9.
Bruyninckx, H., Klotzbücher, M., Hochgeschwender, N.,
Kraetzschmar, G., Gherardi, L., and Brugali, D.
(2013). The BRICS component model: a model-based
development paradigm for complex robotics software
systems. In Proceedings of the 28th Annual ACM
Symposium on Applied Computing, SAC ’13, pages
1758–1764, New York, NY, USA. Association for
Computing Machinery.
Bubeck, A., Weisshardt, F., and Verl, A. (2014). BRIDE - A
toolchain for framework-independent development of
industrial service robot applications. In ISR/Robotik
2014; 41st International Symposium on Robotics,
pages 1–6.
Chitta, S., Marder-Eppstein, E., Meeussen, W., Pradeep, V.,
Rodríguez Tsouroukdissian, A., Bohren, J., Coleman,
D., Magyar, B., Raiola, G., Lüdtke, M., and Fernan-
dez Perdomo, E. (2017). ros_control: A generic and
simple control framework for ROS. The Journal of
Open Source Software, 2(20):456.
Coleman, D., Sucan, I., Chitta, S., and Correll, N. (2014).
Reducing the Barrier to Entry of Complex Robotic
Software: a MoveIt! Case Study. arXiv:1404.3785
[cs]. Publisher: Università degli studi di Bergamo.
Estefo, P., Robbes, R., and Fabry, J. (2015). Code dupli-
cation in ROS launchfiles. In 2015 34th International
Conference of the Chilean Computer Science Society
(SCCC), pages 1–6, Santiago, Chile. IEEE.
Hammoudeh Garcia, N., Lüdtke, M., Kortik, S., Kahl, B.,
and Bordignon, M. (2019). Bootstrapping MDE De-
velopment from ROS Manual Code - Part 1: Meta-
modeling. In 2019 Third IEEE International Confer-
ence on Robotic Computing (IRC), pages 329–336.
Hammoudeh García, N., Deshpande, H., Santos, A., Kahl,
B., and Bordignon, M. (2021). Bootstrapping MDE
development from ROS manual code: Part 2—Model
generation and leveraging models at runtime. Soft-
ware and Systems Modeling.
Koenig, N. and Howard, A. (2004). Design and use
paradigms for Gazebo, an open-source multi-robot
simulator. In 2004 IEEE/RSJ International Confer-
ence on Intelligent Robots and Systems (IROS) (IEEE
Cat. No.04CH37566), volume 3, pages 2149–2154
vol.3.
Schlegel, C. and Worz, R. (1999). The software frame-
work SMARTSOFT for implementing sensorimotor
systems. In Proceedings 1999 IEEE/RSJ Interna-
tional Conference on Intelligent Robots and Sys-
tems. Human and Environment Friendly Robots with
High Intelligence and Emotional Quotients (Cat.
No.99CH36289), volume 3, pages 1610–1616 vol.3.
Schlingloff, H., Kruse, P. M., and Saadatmand, M. (2020).
Excellence in variant testing. In Proceedings of the
14th International Working Conference on Variabil-
ity Modelling of Software-Intensive Systems, VAMOS
’20, pages 1–2, New York, NY, USA. Association for
Computing Machinery.
Stampfer, D., Lotz, A., Lutz, M., and Schlegel, C. (2016).
The SmartMDSD Toolchain: An Integrated MDSD
Workflow and Integrated Development Environment
(IDE) for Robotics Software. Journal of Software En-
gineering for Robotics, page 18.
The Object Management Group (2012). Robotic Technol-
ogy Component (RTC).
The Object Management Group (2016). Hardware Abstrac-
tion Layer for Robotic Technology, v1.0 Beta.
Zamalloa, I., Muguruza, I., Hernández, A., Kojcev, R., and
Mayoral, V. (2018). An information model for mod-
ular robots: the Hardware Robot Information Model
(HRIM). arXiv:1802.01459 [cs]. arXiv: 1802.01459.
MODELSWARD 2022 - 10th International Conference on Model-Driven Engineering and Software Development
270