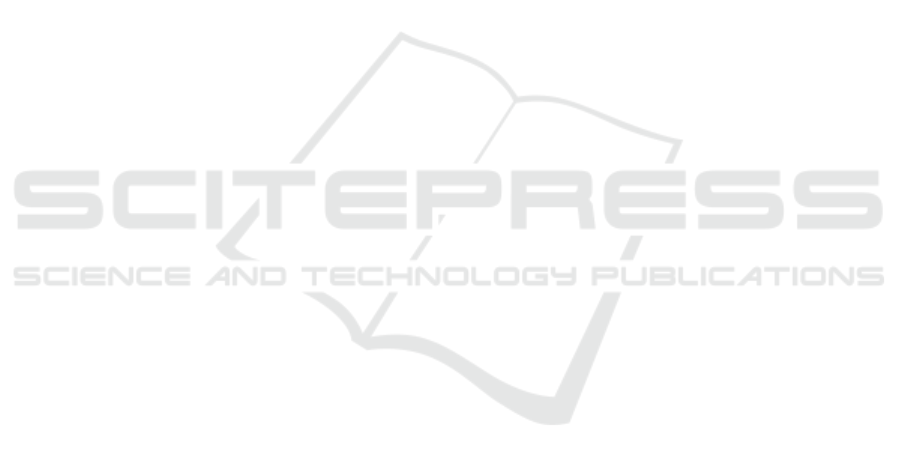
Cheng, C., Ma, G., Zhang, Y., Sun, M., Teng, F., Ding,
H., and Yuan, Y. (2020). A deep learning-based re-
maining useful life prediction approach for bearings.
IEEE/ASME Transactions on Mechatronics, PP.
Cristianini, N. and Shawe-Taylor, J. (2000). Support Vector
Machines. Cambridge University Press.
Fan, Y., Nowaczyk, S., and Rognvaldsson, T. (2015). Eval-
uation of self-organized approach for predicting com-
pressor faults in a city bus fleet. Procedia Computer
Science, 53:447–456.
Geurts, P., Ernst, D., and Wehenkel, L. (2006). Extremely
randomized trees. Machine Learning, 63(1):3–42.
Goldberg, K., Roeder, T., Gupta, D., and Perkins, C. (2001).
Eigentaste: A constant time collaborative filtering al-
gorithm. Information Retrieval, 4:133–151.
Jardine, A. K., Lin, D., and Banjevic, D. (2006). A re-
view on machinery diagnostics and prognostics im-
plementing condition-based maintenance. Mechani-
cal Systems and Signal Processing, 20(7):1483–1510.
Kang, Z., Catal, C., and Tekinerdogan, B. (2021). Remain-
ing useful life (rul) prediction of equipment in pro-
duction lines using artificial neural networks. Sensors,
21(3).
Ke, G., Meng, Q., Finley, T., Wang, T., Chen, W., Ma, W.,
Ye, Q., and Liu, T.-Y. (2017). Lightgbm: A highly
efficient gradient boosting decision tree. In Proceed-
ings of the 31st International Conference on Neu-
ral Information Processing Systems, NIPS’17, page
3149–3157, Red Hook, NY, USA. Curran Associates
Inc.
Lee, S. M., Lee, D., and Kim, Y. S. (2019). The quality
management ecosystem for predictive maintenance in
the industry 4.0 era. International Journal of Quality
Innovation, 5(1):1–11.
Li, X., Zhang, W., Ma, H., Luo, Z., and Li, X. (2020).
Data alignments in machinery remaining useful life
prediction using deep adversarial neural networks.
Knowledge-Based Systems, 197:105843.
Lundberg, S. and Lee, S. (2017a). A unified approach to in-
terpreting model predictions. CoRR, abs/1705.07874.
Lundberg, S. M. and Lee, S. (2017b). A unified approach
to interpreting model predictions. In Guyon, I., von
Luxburg, U., Bengio, S., Wallach, H. M., Fergus, R.,
Vishwanathan, S. V. N., and Garnett, R., editors, Ad-
vances in Neural Information Processing Systems 30:
Annual Conference on Neural Information Processing
Systems 2017, December 4-9, 2017, Long Beach, CA,
USA, pages 4765–4774.
Matos, L. M., Cortez, P., Mendes, R., and Moreau, A.
(2018). A comparison of data-driven approaches for
mobile marketing user conversion prediction. In 2018
International Conference on Intelligent Systems (IS),
pages 140–146.
Matos, L. M., Cortez, P., Mendes, R., and Moreau, A.
(2019). Using deep learning for mobile marketing
user conversion prediction. In 2019 International
Joint Conference on Neural Networks (IJCNN), pages
1–8.
Matos, L. M., Cortez, P., and Mendes, R. C. (2020). Cane -
categorical attribute transformation environment.
Okoh, C., Roy, R., Mehnen, J., and Redding, L. (2014).
Overview of remaining useful life prediction tech-
niques in through-life engineering services. Proce-
dia CIRP, 16:158–163. Product Services Systems and
Value Creation. Proceedings of the 6th CIRP Confer-
ence on Industrial Product-Service Systems.
Oliveira, N., Cortez, P., and Areal, N. (2017). The impact of
microblogging data for stock market prediction: Us-
ing twitter to predict returns, volatility, trading vol-
ume and survey sentiment indices. Expert Syst. Appl.,
73:125–144.
Rauch, E., Linder, C., and Dallasega, P. (2020). Anthro-
pocentric perspective of production before and within
industry 4.0. Computers & Industrial Engineering,
139:105644.
Sahakyan, M., Aung, Z., and Rahwan, T. (2021). Explain-
able artificial intelligence for tabular data: A survey.
IEEE Access, 9:135392–135422.
Shalev-Shwartz, S. and Ben-David, S. (2014). Understand-
ing Machine Learning: From Theory to Algorithms.
Cambridge University Press.
Shapiro, N. Z. and Shapley, L. S. (1978). Values of large
games, I: A limit theorem. Math. Oper. Res., 3(1):1–
9.
Susto, G. A., Beghi, A., and Luca, C. (2012). A predic-
tive maintenance system for epitaxy processes based
on filtering and prediction techniques. Semiconductor
Manufacturing, IEEE Transactions on, 25:638–649.
Susto, G. A., Schirru, A., Pampuri, S., McLoone, S., and
Beghi, A. (2015). Machine learning for predictive
maintenance: A multiple classifier approach. IEEE
Transactions on Industrial Informatics, 11(3):812–
820.
Tashman, L. J. (2000). Out-of-sample tests of forecasting
accuracy: an analysis and review. International Jour-
nal of Forecasting, 16(4):437–450. The M3- Compe-
tition.
Wang, B., Lei, Y., Yan, T., Li, N., and Guo, L. (2020). Re-
current convolutional neural network: A new frame-
work for remaining useful life prediction of machin-
ery. Neurocomputing, 379:117–129.
Wang, W. (2012). An overview of the recent advances in
delay-time-based maintenance modelling. Reliability
Engineering & System Safety, 106:165–178.
Wright, S. (1921). Correlation and causation. Journal of
Agricultural Research., 20(3):557–585.
Wu, D., Jennings, C., Terpenny, J., Gao, R. X., and Kumara,
S. (2017). A Comparative Study on Machine Learn-
ing Algorithms for Smart Manufacturing: Tool Wear
Prediction Using Random Forests. Journal of Manu-
facturing Science and Engineering, 139(7). 071018.
ICAART 2022 - 14th International Conference on Agents and Artificial Intelligence
772