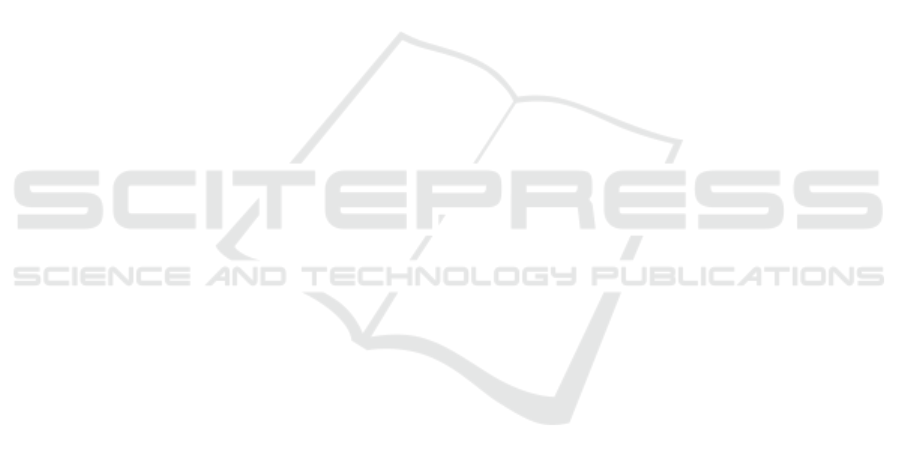
ACKNOWLEDGEMENTS
This study was financed in part by the Coordenac¸
˜
ao
de Aperfeic¸oamento de Pessoal de N
´
ıvel Superior -
Brasil (CAPES) - Finance Code 001.
REFERENCES
Abadi, M. et al. (2015). TensorFlow: Large-scale machine
learning on heterogeneous systems. Software avail-
able from tensorflow.org.
Abdullah, A., Al Enazi, S., and Damaj, I. (2016). Agrisys:
A smart and ubiquitous controlled-environment agri-
culture system. In 2016 3rd MEC International Con-
ference on Big Data and Smart City (ICBDSC), pages
1–6. IEEE.
Alliance, L. (2015). What is LoRaWAN - A
technical overview of Lora and LoRaWAN.
https://lora-alliance.org/resource\textunderscorehub/
what-is-lorawan/. Acessed in 25/07/2021.
Baller, S. P., Jindal, A., Chadha, M., and Gerndt, M.
(2021). DeepEdgeBench: Benchmarking deep neural
networks on edge devices. CoRR, abs/2108.09457.
Bonomi, F., Milito, R., Zhu, J., and Addepalli, S. (2012).
Fog computing and its role in the internet of things. In
Proceedings of the First Edition of the MCC Workshop
on Mobile Cloud Computing, MCC ’12, pages 13–16,
New York, NY, USA. ACM.
Byers, C. C. (2017). Architectural imperatives for fog
computing: Use cases, requirements, and architectural
techniques for fog-enabled iot networks. IEEE Com-
munications Magazine, 55(8):14–20.
Chollet, F. et al. (2015). Keras. https://github.com/fchollet/
keras.
de Toledo, G. R. A. (2019). Electrophysiological charac-
terization of beans (Phaseolus vulgaris L.) cv. BRS-
Expedit under different water availabilities (In Por-
tuguese). PhD thesis, UFPel, Pelotas.
Gia, T. N., Qingqing, L., Queralta, J. P., Zou, Z., Tenhunen,
H., and Westerlund, T. (2019). Edge AI in smart farm-
ing IoT: CNNs at the edge and fog computing with
LoRa. IEEE AFRICON-2019.
Imran, H. A., Mujahid, U., Wazir, S., Latif, U., and
Mehmood, K. (2020). Embedded development boards
for Edge-AI: A comprehensive report.
Kamilaris, A., Gao, F., Prenafeta-Boldu, F. X., and Ali,
M. I. (2016). Agri-IoT: A semantic framework for
internet of things-enabled smart farming applications.
In 2016 IEEE 3rd World Forum on Internet of Things
(WF-IoT), pages 442–447. IEEE.
Kamilaris, A. and Prenafeta-Bold
´
u, F. X. (2018). Deep
learning in agriculture: A survey. Computers and elec-
tronics in agriculture, 147:70–90.
Kawai, T. and Mineno, H. (2020). Evaluation environment
using edge computing for artificial intelligence-based
irrigation system. In 2020 16th International Con-
ference on Mobility, Sensing and Networking (MSN),
pages 214–219.
Li, H., Ota, K., and Dong, M. (2018). Learning iot in
edge: Deep learning for the internet of things with
edge computing. IEEE Network, 32(1):96–101.
Liakos, K. G., Busato, P., Moshou, D., Pearson, S., and
Bochtis, D. (2018). Machine learning in agriculture:
A review. Sensors, 18(8):2674.
Maffei, M. and Bossi, S. (2006). Electrophysiology and
plant responses to biotic stress. In Plant Electrophys-
iology, pages 461–481. Springer.
Misra, N. N., Dixit, Y., Al-Mallahi, A., Bhullar, M. S.,
Upadhyay, R., and Martynenko, A. (2020). IoT, big
data and artificial intelligence in agriculture and food
industry. IEEE Internet of Things Journal, pages 1–1.
Nvidia, C. (2021). Jetson Nano. https://www.nvidia.com/
jetson-nano. Acessed in 16/07/2021.
Oliveira Jr, M. A. d., Sedrez, G., Monteiro, A., Puntel, F. E.,
and Cavalheiro, G. G. H. (2021). Effects of agro-
sensor time series approximation on plant stress de-
tection: An experimental study. In 2021 XIII Brazilian
Congress on Agroinformatics (SBIAGRO).
Pandas Development Team, T. (2020). pandas-dev/pandas:
Pandas.
Pedregosa, F., Varoquaux, G., Gramfort, A., Michel, V.,
Thirion, B., Grisel, O., Blondel, M., Prettenhofer,
P., Weiss, R., Dubourg, V., Vanderplas, J., Passos,
A., Cournapeau, D., Brucher, M., Perrot, M., and
Duchesnay, E. (2011). Scikit-learn: Machine learning
in Python. Journal of Machine Learning Research,
12:2825–2830.
Pereira, D. R., Papa, J. P., Saraiva, G. F. R., and Souza,
G. M. (2018). Automatic classification of plant elec-
trophysiological responses to environmental stimuli
using machine learning and interval arithmetic. Com-
puters and Electronics in Agriculture, 145:35–42.
Proietti, M., Bianchi, F., Marini, A., Menculini, L., Termite,
L., Garinei, A., Biondi, L., and Marconi, M. (2021).
Edge intelligence with deep learning in greenhouse
management. In Proceedings of the 10th International
Conference on Smart Cities and Green ICT Systems
- Volume 1: SMARTGREENS,, pages 180–187. IN-
STICC, SciTePress.
Saraf, S. B. and Gawali, D. H. (2017). IoT based smart ir-
rigation monitoring and controlling system. In 2017
2nd IEEE International Conference on Recent Trends
in Electronics, Information & Communication Tech-
nology (RTEICT), pages 815–819. IEEE.
Shi, W., Cao, J., Zhang, Q., Li, Y., and Xu, L. (2016). Edge
computing: Vision and challenges. IEEE Internet of
Things Journal, 3(5):637–646.
Zhou, G.-X., Li, P.-q., and Zhou, X.-d. (2011). Global cli-
mate warming on climate and agriculture in western
liaoning impact. In 2011 International Conference on
Remote Sensing, Environment and Transportation En-
gineering, pages 2200–2203.
SENSORNETS 2022 - 11th International Conference on Sensor Networks
222