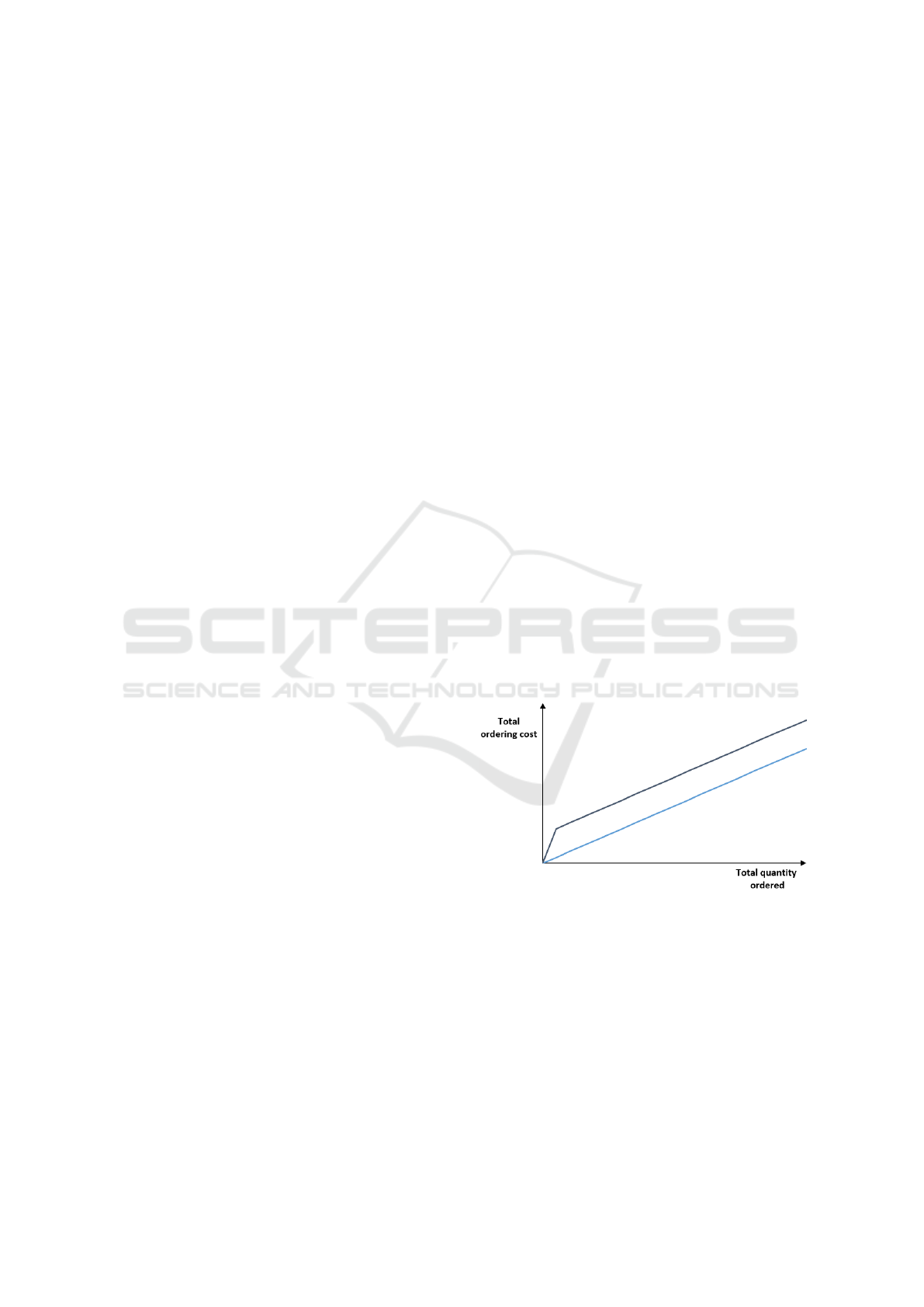
to solve it exactly in a reasonable time, and it is nec-
essary to solve it approximately. In this article, we
tried to reduce the solution space of the problem we
address by modeling. In this model, the orders we
can place are represented by objects we call "order-
ing blocks", as defined in (Sahu, 2020). The opti-
mization aims to find the best combination of blocks
for the considered horizon. It enabled us to formu-
late the problem we want to solve as an Integer Linear
Program (ILP) and to solve it using a classic branch-
and-bound solver. As there are multiple cases of all-
unit discounts in industrial replenishment contexts,
the ILP has been written to be generic and applica-
ble to a large set of discount types.
The ILP allows an easy formulation of the prob-
lem. As free and commercial solvers already exist,
there is no need to develop more complicated heuris-
tics to solve ILPs. As a result, the method we offer
is easily implementable in real multiperiodic joint-
replenishment contexts. Moreover, the optimization
tool we develop is intended to be a module assisting a
single-item single-period replenishment optimization
engine. Therefore, it is suitable to be integrated with
already existing optimization tools.
The remainder of the paper is organized as fol-
lows. We will first describe the approach we devel-
oped and the notations we use in section 2. Then, we
will present the ILP in section 3. We will next de-
scribe the experimental protocol we put in place to
validate the model and present the numerical results
in section 4. Finally, we will provide a conclusion in
section 5.
2 DEVELOPED APPROACH AND
NOTATIONS
In this section, we will first detail the problem we ad-
dress and give some examples of application in indus-
trial replenishment contexts. Then, we will explain
the approach we put in place to model and solve it.
2.1 Details of the Problem and Use
Cases
As we stated before, we focus on constraints concern-
ing several items at the same time. It implies a need to
design an optimization method that takes into account
all the items simultaneously. We search to plan the re-
plenishment for groups of items jointly, on several pe-
riods for a finite horizon, considering joint costs and
discounts. In this paper, we consider only all-unit dis-
counts. This means the discount is applied on all the
items ordered once the breakdown is reached. We ap-
ply a direct grouping strategy, as defined in (Bastos
et al., 2017), and consider only groups of items that
have the same cycle time.
There are two major categories of multi-item con-
straints we consider: fixed ordering cost and all-unit
discount. They are defined as follows.
Fixed Ordering Cost: It is a cost applied to the
whole order once we order something (i.e. when
the total quantity ordered is strictly superior to 0).
For example, a supplier can add a transport cost
to the ordering cost, and this cost is only applied
if something is ordered. This cost is also called in
the literature "Major Ordering Cost".
All-unit Discount: It is a discount applied on all the
items ordered (i.e. on the total ordering cost)
once a given breakdown is reached. There can
be one or several breakdowns with corresponding
discounts. The breakdowns can also concern dif-
ferent values, such as the total ordering cost or the
total quantity ordered, but also the total weight or
volume of the order for example. A practical ex-
ample of the all-unit discount is the Franco, where
the supplier charges a constant penalty cost if the
total ordering cost is lower than a given break-
down.
Figures 1 and 2 are graphical examples of the two
notions explained above.
Figure 1: Representation of the cost function in case of a
fixed ordering cost. The dark blue curve is the case without
fixed ordering cost.
2.2 Modeling Approach and Definitions
As the problem is NP-Hard, we can’t expect to find
the optimal solution to large-scale instances in a rea-
sonable time. Therefore, we have to define a pro-
cess to find good-quality solutions in a suitable de-
lay. In this article, we choose to reduce the search
space by modeling. First, we constrain the time steps
Multi-periodic Joint Replenishment Planning Method for Various All-unit Discounts
87