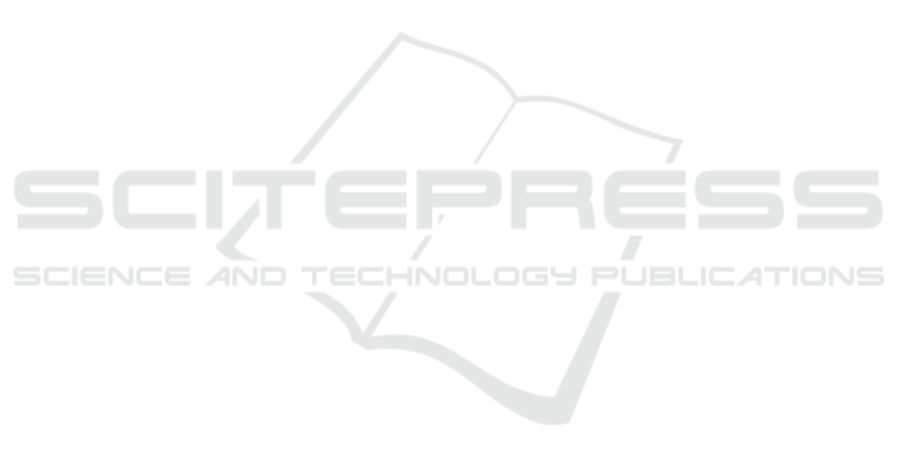
language definitions. We will also develop a model
transformation tool using the Metaedit+ technologies
so as to transform the ManLang models in accor-
dance with the AutomationML standard (Drath et al.,
2008), which is supported by other manufacturing
tools and thus enables to process the modeled re-
quirements in ManLang by different tools. We will
further extend ManLang for the specifications of re-
source behaviours (e.g., spot welding robots) and de-
velop a transformation tool for Modelica (Mattsson
et al., 1998) which enables to use the simulation tools
that support Modelica.
ACKNOWLEDGEMENTS
This work is part of the AITOC (Artificial Intelligence
supported Tool Chain in Manufacturing Engineering)
project supported by European ITEA and funded by
the TUBITAK TEYDEB Project No: 9200078.
REFERENCES
Brauer, W., Reisig, W., and Rozenberg, G., editors (1987).
Petri Nets: Central Models and Their Properties, Ad-
vances in Petri Nets 1986, Part II, Proceedings of
an Advanced Course, Bad Honnef, 8.-19. September
1986, volume 255 of Lecture Notes in Computer Sci-
ence. Springer.
Brooke, J. (1996). SUS: a “quick and dirty” usability scale.
Usability evaluation in industry, 189(3):189–194.
Chryssolouris, G., Mavrikios, D., Papakostas, N., Mourtzis,
D., Michalos, G., and Georgoulias, K. (2009). Digi-
tal manufacturing: History, perspectives, and outlook.
Proceedings of the Institution of Mechanical Engi-
neers, Part B: Journal of Engineering Manufacture,
223(5):451–462.
Drath, R., Luder, A., Peschke, J., and Hundt, L. (2008).
Automationml - the glue for seamless automation en-
gineering. In 2008 IEEE International Conference
on Emerging Technologies and Factory Automation,
pages 616–623.
Freddi, D. (2018). Digitalisation and employment in man-
ufacturing - pace of the digitalisation process and im-
pact on employment in advanced italian manufactur-
ing companies. AI Soc., 33(3):393–403.
Friedenthal, S., Moore, A., and Steiner, R. (2008). A Prac-
tical Guide to SysML: Systems Modeling Language.
Morgan Kaufmann Publishers Inc., San Francisco,
CA, USA.
Jiwei, H., Hexu, S., Tao, L., and Zhaoming, L. (2008). The
research of manufacturing execution system modeling
based on colored petri nets. In 2008 2nd International
Symposium on Systems and Control in Aerospace and
Astronautics, pages 1–4.
Kelly, S., Lyytinen, K., and Rossi, M. (2013). Metaedit+
A fully configurable multi-user and multi-tool CASE
and CAME environment. In Jr., J. A. B., Krogstie,
J., Pastor, O., Pernici, B., Rolland, C., and Sølvberg,
A., editors, Seminal Contributions to Information Sys-
tems Engineering, 25 Years of CAiSE, pages 109–129.
Springer.
Kroll, H., Horvat, D., and J
¨
ager, A. (2018). Effects of au-
tomatisation and digitalisation on manufacturing com-
panies’ production efficiency and innovation perfor-
mance. Fraunhofer ISI Discussion Papers - Inno-
vation Systems and Policy Analysis 58, Karlsruhe.
urn:nbn:de:0011-n-4873361.
L
¨
utjen, M. and Rippel, D. (2015). Gramosa framework
for graphical modelling and simulation-based analy-
sis of complex production processes. The Interna-
tional Journal of Advanced Manufacturing Technol-
ogy, 81(1):171–181.
Mattsson, S. E., Elmqvist, H., and Otter, M. (1998). Phys-
ical system modeling with modelica. Control Engi-
neering Practice, 6(4):501–510.
Petrasch, R. and Hentschke, R. (2016). Process modeling
for industry 4.0 applications: Towards an industry 4.0
process modeling language and method. In 2016 13th
International Joint Conference on Computer Science
and Software Engineering (JCSSE), pages 1–5.
Rumbaugh, J., Jacobson, I., and Booch, G. (2004). Uni-
fied Modeling Language Reference Manual, The (2Nd
Edition). Pearson Higher Education.
Seidewitz, E. (2003). What models mean. IEEE Software,
20(5):26–32.
Vjestica, M., Dimitrieski, V., Pisaric, M., Kordic, S., Ris-
tic, S., and Lukovic, I. (2020). An application of
a DSML in industry 4.0 production processes. In
Lalic, B., Majstorovic, V. D., Marjanovic, U., von
Cieminski, G., and Romero, D., editors, Advances in
Production Management Systems. The Path to Digital
Transformation and Innovation of Production Man-
agement Systems - IFIP WG 5.7 International Con-
ference, APMS 2020, Novi Sad, Serbia, August 30 -
September 3, 2020, Proceedings, Part I, volume 591
of IFIP Advances in Information and Communication
Technology, pages 441–448. Springer.
V
¨
olzer, H. (2010). An overview of BPMN 2.0 and its poten-
tial use. In Mendling, J., Weidlich, M., and Weske, M.,
editors, Business Process Modeling Notation - Second
International Workshop, BPMN 2010, Potsdam, Ger-
many, October 13-14, 2010. Proceedings, volume 67
of Lecture Notes in Business Information Processing,
pages 14–15. Springer.
Weissenberger, B., Flad, S., Chen, X., R
¨
osch, S., Voigt,
T., and Vogel-Heuser, B. (2015). Model driven en-
gineering of manufacturing execution systems using
a formal specification. In 20th IEEE Conference on
Emerging Technologies & Factory Automation, ETFA
2015, Luxembourg, September 8-11, 2015, pages 1–8.
IEEE.
Whittle, J., Hutchinson, J., and Rouncefield, M. (2014). The
state of practice in model-driven engineering. IEEE
Software, 31(3):79–85.
Witsch, M. and Vogel-Heuser, B. (2012). Towards a formal
specification framework for manufacturing execution
systems. IEEE Trans. Ind. Informatics, 8(2):311–320.
ENASE 2022 - 17th International Conference on Evaluation of Novel Approaches to Software Engineering
404