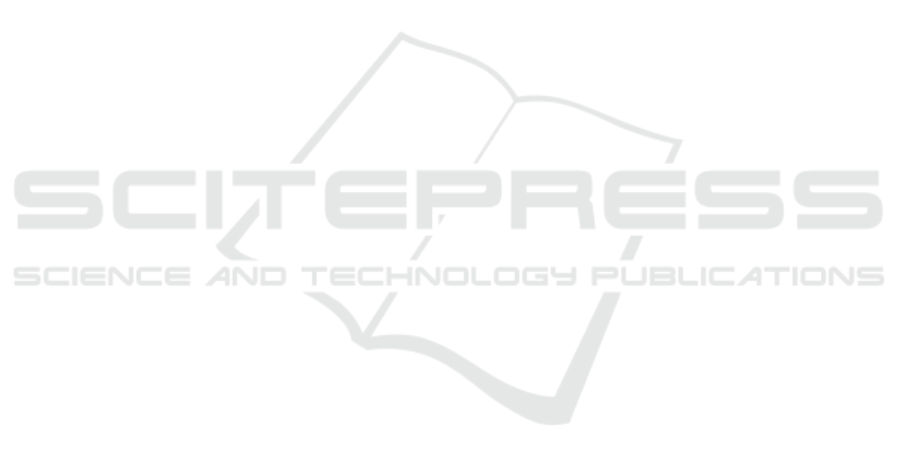
Hemphill, M., Yuan, T., Wang, G., Yeh, J., Tsai, C.,
Chuang, A., and Liaw, P. (2012). Fatigue behavior of
al0.5cocrcufeni high entropy alloys. Acta Materialia,
60(16):5723–5734.
Ingram, C. and Scheaffer, R. (1976). On consistent esti-
mation of age replacement intervals. Technometrics,
18(2):213–219.
Keshevan, K., Sargent, G., and Conrad, H. (1980). Sta-
tistical analysis of the hertzian fracture of pyrex glass
using the weibull distribution function. Journal of Ma-
terials Science, 15:839–844.
Knopik, L. and Migawa, K. (2017). Optimal age-
replacement policy for non-repairable technical ob-
jects with warranty. Eksploatacja i Niezawodnosc -
Maintenance and Reliability, 19(2):172–178.
Lai, C. (2014). Generalized Weibull Distributions. Springer,
Heidelberg.
Lai, C., Murthy, D., and Xie, M. (2006). Weibull distri-
butions and their applications. In Pham, H., editor,
Springer Handbook of Engineering Statistics, pages
63–78. Springer London, London.
L
´
eger, C. and Cl
´
eroux, R. (1992). Nonparametric age re-
placement: bootstrap confidence intervals for the op-
timal cost. Operations research, 40(6):1062–1073.
Li, Q., Fang, J., Liu, D., and Tang, J. (2003). Failure proba-
bility prediction of concrete components. Cement and
Concrete Research, 33:1631–1636.
Li, Y.-B., Sang, H.-B., Xiong, X., and Li, Y.-R. (2021).
An improved adaptive genetic algorithm for two-
dimensional rectangular packing problem. Applied
Sciences, 11(1):413.
Nakagawa, T. (2003). Maintenance and optimum policy. In
Pham, H., editor, Handbook of reliability engineering,
pages 367–395. Springer.
Nakagawa, T. (2006). Statistical models on maintenance. In
Pham, H., editor, Springer Handbook of Engineering
Statistics, pages 835–848. Springer London, London.
Neuenfeldt Jr., A., Silva, E., Francescatto, M., Rosa, C.,
and Siluk, J. (2022). The rectangular two-dimensional
strip packing problem real-life practical constraints:
A bibliometric overview. Computers & Operations
Research, 137:105521.
Newell, J., Kurzeja, T., Spence, M., and Lynch, M. (2002).
Analysis of recoil compressive failure in high perfor-
mance polymers using two-, four-parameter weibull
models. High Performance Polymers, 14:425–434.
Queeshi, F. and Sheikh, A. (1997). Probabilistic characteri-
zation of adhesive wear in metals. IEEE Transactions
on Reliability, 46:38–44.
Ran, A. and Rosenlund, S. (1976). Age replacement with
discounting for a continuous maintenance cost model.
Technometrics, 18(4):459–465.
Scmeaffer, R. (1971). Optimum Age Replacement Poli-
cies with an Ikreasing Cost Factor. Technometrics,
13(1):139–144.
Sheikh, A., Boah, J., and Hansen, D. (1990). Statistical
modelling of pitting corrosion and pipeline reliability.
Corrosion, 46:190–196.
Subramanian, R. and Wolff, M. (1976). Age replacement in
simple systems with increasing loss functions. IEEE
Transactions on Reliability, 25(1):32–34.
Wang, J., Qiu, Q., and Wang, H. (2021a). Joint optimization
of condition-based and age-based replacement policy
and inventory policy for a two-unit series system. Re-
liability Engineering and System Safety, 205:107251.
Wang, T., Hu, Q., and Lim, A. (2021b). An exact algorithm
for two-dimensional vector packing problem with vol-
umetric weight and general costs. European Journal
of Operational Research.
Wei, L., Lai, M., Lim, A., and Hu, Q. (2020). A branch-and-
price algorithm for the two-dimensional vector pack-
ing problem. European Journal of Operational Re-
search, 281(1):25–35.
Weibull, W. (1939). A statistical theory of the strength of
material. Ingeniors Vetenskaps Akademiens Handli-
gar, 151:5–45.
Xie, S., Lin, H., Wang, Y., Chen, Y., Xiong, W., Zhao,
Y., and Du, S. (2020). A statistical damage consti-
tutive model considering whole joint shear deforma-
tion. International Journal of Damage Mechanics,
29(6):988–1008.
Zhao, X., Al-Khalifa, K., Hamouda, A., and Nakagawa, T.
(2017). Age replacement models: A summary with
new perspectives and methods. Reliability Engineer-
ing & System Safety, 161:95–105.
Zhao, X., Li, B., Mizutani, S., and Nakagawa, T. (2021).
A Revisit of Age-Based Replacement Models With
Exponential Failure Distributions. IEEE Transactions
on Reliability.
Zhou, S., Li, X., Zhang, K., and Du, N. (2019). Two-
dimensional knapsack-block packing problem. Ap-
plied Mathematical Modelling, 73:1–18.
Global Spare Parts Exploitation Costs Optymization and Its Reduction to Rectangular Knapsack Problem
373