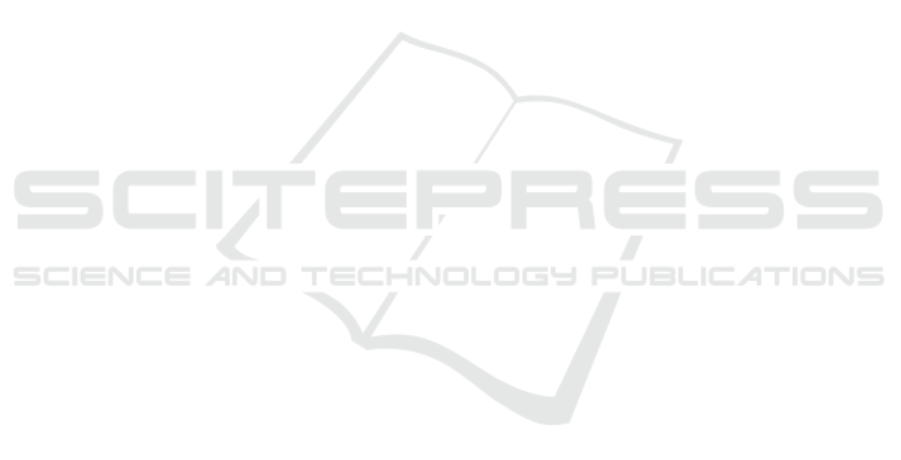
mance by collecting the operating condition data.
2. Performance Improvement by optimizing and
utilizing the equipment better, optimizing flows,
reducing production losses.
3. Quality Improvement using a feedback loop
which would measure the product quality and then
tweak the operating conditions to improve the
same.
4. Reduced Energy Consumption by operating the
equipment with minimum energy use.
5. Improved Maintenance by condition-based
monitoring, data collection on system operating
condition and subsequent data analysis.
6. Robustness/Reliability includes clear and unam-
biguous parameter measurement, less false posi-
tives, fewer or no re-calibrations required and the
solution that allows for continuous operation of
industrial processes.
7. Reasonable Cost includes the cost vs. benefit
analysis rather than the absolute cost of the IIoT
solution.
3 SMART RETROFIT: LOW
HANGING FRUIT
OPPORTUNITIES
The potential smart retrofit benefits range from
higher equipment effectiveness to achieving better
performance. These benefits depend heavily on
the application for which smart retrofit solutions
are implemented. Some potential smart retrofit
applications that fall under the “low hanging fruit”
category, meaning applications for which smart
retrofit IIoT solutions are more easily implemented,
are as described below:
• Adjustable Speed Drives in Industrial Mixing:
The central idea is to operate the industrial mix-
ing motors by reducing the initial speed to avoid
power spikes. One of the methods to accom-
plish this is to use a variable frequency drive to
control the speed of motor based on a maximum
power requirement. As the speed of mixing in-
creases, the mixture warms up reducing the vis-
cosity and thereby the torque requirement, which
in turn would reduce the power required from the
motor. There is also a possibility of measuring
and assessing the product quality through its vis-
cosity and temperature as represented by the re-
quired torque.
• Compressed Air Energy Management: In-
stalling pressure, air flow rate and current trans-
ducer sensors on compressed air system can help
analyze and report performance of the system.
This data can be used to assess air leaks, opti-
mize multiple compressor part load performance,
and avoid short cycling and flow spikes. In ad-
dition, compressed air dryer system performance
can be monitored by measuring the overflow wa-
ter collected in downstream tank and/or air out-
let dewpoint. This detects water pass through and
reports performance to create trends and support
troubleshooting procedures.
• Intelligent Bag House Fan Control: This ap-
plication consists of implementing an on-demand
system for baghouses. The system would main-
tain the required suction pressure based on the ac-
tivity of the workstations and use a variable fre-
quency drive to adjust the speed of the baghouse
blower. Such an operation would result in running
the blower at lower than full-load capacity as re-
quired. The blower speed is efficiently controlled
by changing the frequency of voltage provided to
the motor instead of using other methods such as
valves and dampers.
• Energy Storage Intelligence: The application
consists of measuring and reporting the equip-
ment performance for energy storage units like
batteries or ice storage. These measurements can
be used to charge (e.g. solar) when the energy is
available or inexpensive and discharge to reduce
electricity demand and TOU charges
• Cooling Tower “Free Cooling” Intelligence:
Using the cooling tower water to cool the process
fluid helps reduce the load from the chiller sys-
tem partially or completely depending on the am-
bient temperature. Performance can be optimized
by adjusting the parallel free cooling and chiller
loops.
• Smart Condensate Return Tank: By measur-
ing the make-up and feed water flowing through
a boiler condensate tank, condensate return and
boiler loads can be tracked and steam trap prob-
lems can be detected to reduce water treatment
costs and leaks. Boiler performance can also be
visualised for better troubleshooting and perfor-
mance optimization.
• Production Line “Quick Change” Monitor-
ing: The goal is to minimize product change-out
time. IIoT solutions can be used to know the
changeover/change out time from machine load
data. This data can also be used to provide in-
sights around overall equipment effectiveness in
SMARTGREENS 2022 - 11th International Conference on Smart Cities and Green ICT Systems
126