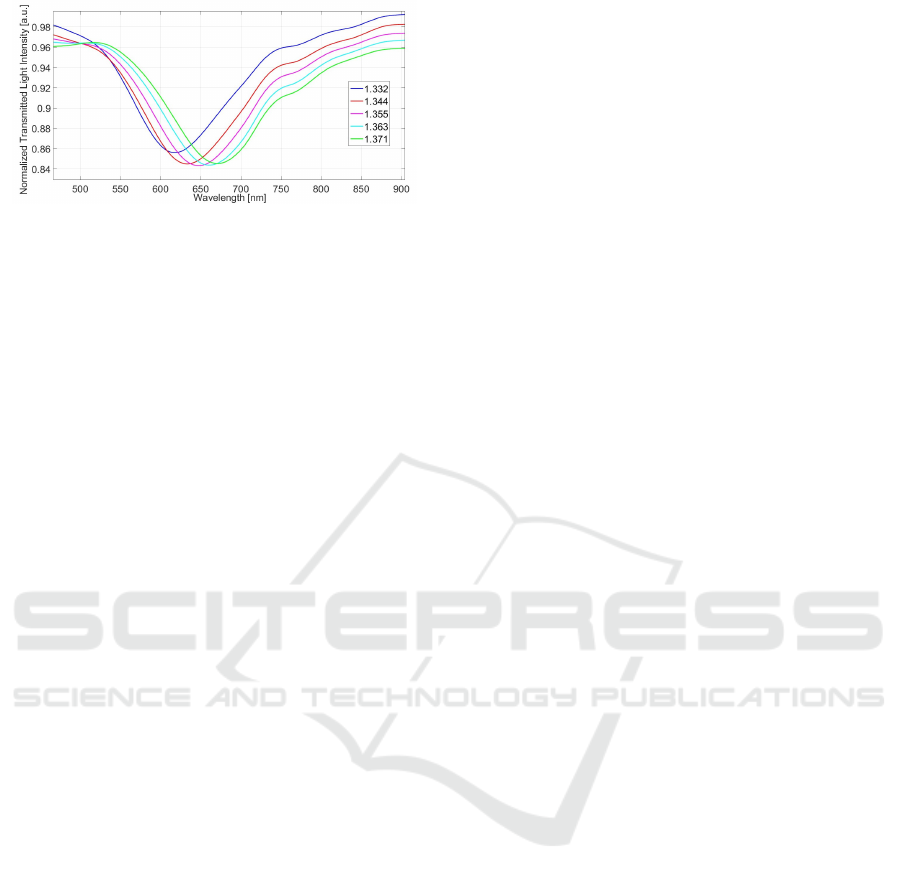
Figure 10: SPR spectra obtained by a D-shaped POF sen-
sor without the buffer layer (with a gold nanofilm on the
core of POF, directly) at different water-glycerin solutions
in contact with the gold nanofilm.
polishing process here proposed, only a gold sputter-
ing has been used to carry out the SPR-D-shaped POF
sensor. We have characterized the SPR-POF sensor
configuration without the buffer layer to better test the
automatic polishing process here proposed. With re-
spect to the SPR curves reported in (Cennamo et al.,
2011) in the same configuration, the SPR curves here
obtained present better performances in terms of full
width at half maximum of the SPR curve, due to the
automatic polishing process here proposed.
6 CONCLUSIONS
The experimental results presented in this paper
demonstrate the feasibility of the proposed approach
for automatic production of a SPR-POF sensor based
on the human-robot collaboration paradigm. The
robotized polishing phase results into a duration 70%
shorter than the current handmade process. The qual-
ity of the polishing process is at least comparable to
the handmade one as demonstrated by the SPR-POF
sensor tests. A characterization of the actual rough-
ness will be carried out by resorting to Atomic force
microscope measurements. This will allow to opti-
mize the process parameters. Moreover, the possi-
bility to establish the contact force so as to obtain a
given D-shaped depth with the aim to optimize the
plasmonic resonant quality factor will be investigated.
ACKNOWLEDGEMENTS
This work was supported by the VALERE program of
the University of Campania, CAMPANIA project.
REFERENCES
Calinon, S. (2018). Learning from Demonstration (Pro-
gramming by Demonstration), pages 1–8. Springer
Berlin Heidelberg, Berlin, Heidelberg.
Cennamo, N., Massarotti, D., Conte, L., and Zeni, L.
(2011). Low cost sensors based on spr in a plastic
optical fiber for biosensor implementation. Sensors
(Basel), 11(12):11752–11760.
Cennamo, N., Pesavento, M., and Zeni, L. (2021). A re-
view on simple and highly sensitive plastic optical
fiber probes for bio-chemical sensing. Sens. and Act.
B: Chemical, 331:129393.
Cohn, D., Ghahramani, Z., and Jordan, M. (1996). Active
learning with statistical models. J. Art. Intell. Res.,
4:129–145.
Dempster, A., Laird, N., and Rubin, D. (1977). Maxi-
mum likelihood from incomplete data via the em al-
gorithm. J. Royal Statist. Soc.: Series B (Methodolog-
ical), 29(1):1–38.
Flacco, F., Kroger, T., Luca, A. D., and Khatib, O. (2012). A
depth space approach to human-robot collision avoid-
ance. In 2012 IEEE Int. Conf. on Rob. and Aut. IEEE.
Gasior, K., Martynkien, T., and Urbanczyk, W. (2014).
Effect of constructional parameters on the perfor-
mance of a surface plasmon resonance sensor based
on a multimode polymer optical fiber. Appl. Opt.,
53(35):8167–8174.
Haddadin, S., Albu-Schaffer, A., Frommberger, M., Ross-
mann, J., and Hirzinger, G. (2009). The dlr crash
report: towards a standard crash-testing protocol for
robot safety - part II: Discussions. In 2009 IEEE Int.
Conf. on Rob. and Aut., pages 280–287. IEEE.
Khatib, O. (1987). A unified approach for motion and force
control of robot manipulators: The operational space
formulation. IEEE J. Rob. and Aut., 3(1):43–53.
Magrini, E., Flacco, F., and De Luca, A. (2014). Estimation
of contact forces using a virtual force sensor. In 2014
IEEE/RSJ Int. Conf. on Intell. Rob. and Syst., pages
2126–2133.
Natale, C. (2019). Physical Human-Robot Interaction,
pages 1–9. Springer London, London.
PrimeSense (2011). PrimeSense NITE Algorithms
1.5. https://www.yumpu.com/en/document/view/
11580035/primesense-nite-algorithms-15-openni.
Accessed on December 2021.
Schindlbeck, C. and Haddadin, S. (2015). Unified passivity-
based cartesian force/impedance control for rigid and
flexible joint robots via task-energy tanks. In 2015
IEEE Int. Conf. on Rob. and Aut. (ICRA), pages 440–
447.
Schwarz, G. (1978). Estimating the dimension of a model.
Annals of Statistics, 6(2):461–464.
Siciliano, B., Sciavicco, L., Villani, L., and Oriolo, G.
(2009). Robotics – Modelling, Planning and Control.
Springer.
Villani, L. (2020). Hybrid Force and Position Control,
pages 1–6. Springer Berlin Heidelberg, Berlin, Hei-
delberg.
ICINCO 2022 - 19th International Conference on Informatics in Control, Automation and Robotics
368