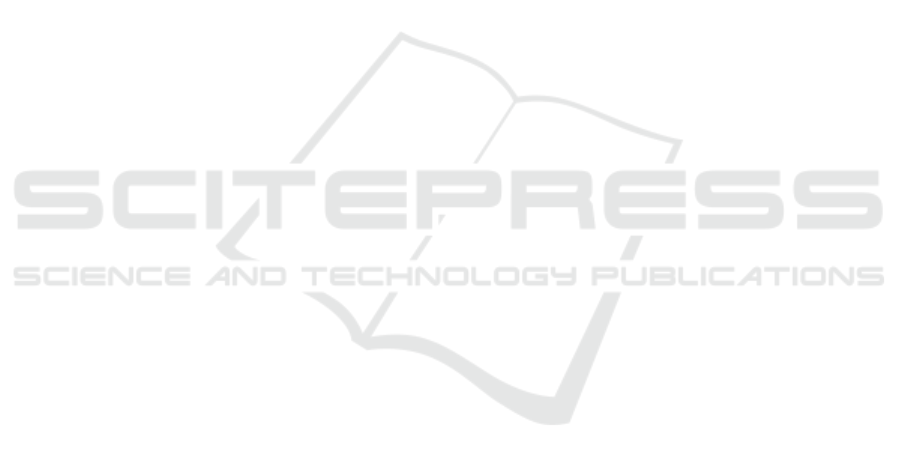
in this paper includes mechanical connection by way
of rotating permanent magnets, communication us-
ing Ethernet for the physical layer utilizing the mag-
nets as the electrical connection between modules,
and power sharing via a modified power over Eth-
ernet system using the same conductors as the data
pairs. The system has been successfully protoyped
and mechanically tested, work is ongoing to integrate
the electronics and mechanical hardware together to
perform holistic testing. Initial experiments have been
performed in simulation to assess the accuracy of the
network simulator. Work is ongoing to perform ex-
periments with rover modules, and implement proto-
cols for topology discovery and routing of data pack-
ets through the system.
REFERENCES
Ahmadzadeh, H., Masehian, E., and Asadpour, M. (2016).
Modular robotic systems: Characteristics and appli-
cations. Journal of Intelligent and Robotic Systems:
Theory and Applications, 81(3-4):317–357.
Baca, J., Ferre, M., and Aracil, R. (2012). A heterogeneous
modular robotic design for fast response to a diversity
of tasks. Rob. Auton. Syst., 60(4):522–531.
Baca, J., Hossain, S. G. M., Dasgupta, P., Nelson, C. A.,
and Dutta, A. (2014). ModRED: Hardware design
and reconfiguration planning for a high dexterity mod-
ular self-reconfigurable robot for extra-terrestrial ex-
ploration. Rob. Auton. Syst., 62(7):1002–1015.
Brunete, A., Ranganath, A., Segovia, S., de Frutos, J. P.,
Hernando, M., and Gambao, E. (2017). Current trends
in reconfigurable modular robots design. Int. J. Adv.
Rob. Syst., 14(3):172988141771045.
Castano, A., Behar, A., and Will, P. M. (2002). The
conro modules for reconfigurable robots. IEEE/ASME
Trans. Mechatron., 7(4):403–409.
Daidi
´
e, D., Barbey, O., Guignard, A., Roussy, D., Guenter,
F., Ijspeert, A., and Billard, A. (2007). The DoF-box
project: An educational kit for configurable robots.
IEEE/ASME International Conference on Advanced
Intelligent Mechatronics, AIM.
Davey, J., Kwok, N., and Yim, M. (2012). Emulating self-
reconfigurable robots - design of the SMORES sys-
tem. Rep. U. S., pages 4464–4469.
Dorigo, M. (2005). Swarm-bot: An experiment in swarm
robotics. Proceedings - 2005 IEEE Swarm Intelli-
gence Symposium, SIS 2005, 2005:199–207.
Dorigo, M., Floreano, D., Gambardella, L. M., Mondada,
F., Nolfi, S., Baaboura, T., Birattari, M., Bonani, M.,
Brambilla, M., Brutschy, A., Burnier, D., Campo,
A., Christensen, A. L., Decugniere, A., Di Caro,
G., Ducatelle, F., Ferrante, E., F
¨
orster, A., Gonzales,
J. M., Guzzi, J., Longchamp, V., Magnenat, S., Math-
ews, N., Montes De Oca, M., O’Grady, R., Pinciroli,
C., Pini, G., R
´
etornaz, P., Roberts, J., Sperati, V., Stir-
ling, T., Stranieri, A., St
¨
utzle, T., Trianni, V., Tuci,
E., Turgut, A. E., and Vaussard, F. (2013). Swar-
manoid: A novel concept for the study of heteroge-
neous robotic swarms. IEEE Robot. Autom. Mag.,
20(4):60–71.
Fai
˜
na, A., Bellas, F., Orjales, F., Souto, D., and Duro,
R. J. (2015). An evolution friendly modular archi-
tecture to produce feasible robots. Rob. Auton. Syst.,
63(P2):195–205.
Feczko, J., Manka, M., Krol, P., Giergiel, M., Uhl, T., and
Pietrzyk, A. (2015). Review of the modular self re-
configurable robotic systems. 2015 10th International
Workshop on Robot Motion and Control, RoMoCo
2015, pages 182–187.
Fukuda, T. and Kawauchi, Y. (1990). Cellular robotic
system (CEBOT) as one of the realization of self-
organizing intelligent universal manipulator. pages
662–667.
Fukuda, T. and Nakagawa, S. (1988). Dynamically recon-
figurable robotic system. In Proceedings. 1988 IEEE
International Conference on Robotics and Automa-
tion, pages 1581–1586 vol.3.
Gambao, E., Brunete, A., and Hernando, M. (2005). Multi-
configurable inspection robots for low diameter canal-
izations. In 22nd ISARC. unknown.
Gilpin, K., Knaian, A., and Rus, D. (2010). Robot peb-
bles: One centimeter modules for programmable mat-
ter through self-disassembly. Proceedings - IEEE In-
ternational Conference on Robotics and Automation,
pages 2485–2492.
Gilpin, K., Kotay, K., Rus, D., and Vasilescu, I.
(2008). Miche: Modular shape formation by Self-
Disassembly. Int. J. Rob. Res., 27(3-4):345–372.
Jia, X., Frenger, M., Chen, Z., Hamel, W. R., and Zhang, M.
(2015). An alligator inspired modular robot. Proceed-
ings - IEEE International Conference on Robotics and
Automation, 2015-June(June):1949–1954.
Jørgensen, M. W., Østergaard, E. H., and Lund, H. H.
(2004). Modular ATRON: Modules for a self-
reconfigurable robot. Rep. U. S., 2:2068–2073.
Kee, V., Rojas, N., Elara, M. R., and Sosa, R. (2014).
Hinged-Tetro : A self-recon fi gurable module for
nested recon fi guration. pages 1539–1546.
Koseki, M., Minami, K., and Inou, N. (2004). Cellular
robots forming a mechanical structure ( evaluation of
structural formation and hardware design of “ CHO-
BIE II ”). Proceedings of 7th International Sym-
posium on Distributed Autonomous Robotic Systems
(DARS04), pages 131–140.
Kotay, K., Rus, D., Vona, M., and McGray, C. (1998). The
self-reconfiguring robotic molecule. Proceedings -
IEEE International Conference on Robotics and Au-
tomation, 1:424–431.
Liedke, J., Matthias, R., Winkler, L., and Worn, H. (2013).
The collective self-reconfigurable modular organism
(CoSMO). 2013 IEEE/ASME International Confer-
ence on Advanced Intelligent Mechatronics: Mecha-
tronics for Human Wellbeing, AIM 2013, pages 1–6.
Lyder, A., Franco, R., Garcia, M., and Stoy, K. (2010).
Genderless connection mechanism for modular robots
introducing torque transmission between modules.
ICINCO 2022 - 19th International Conference on Informatics in Control, Automation and Robotics
392