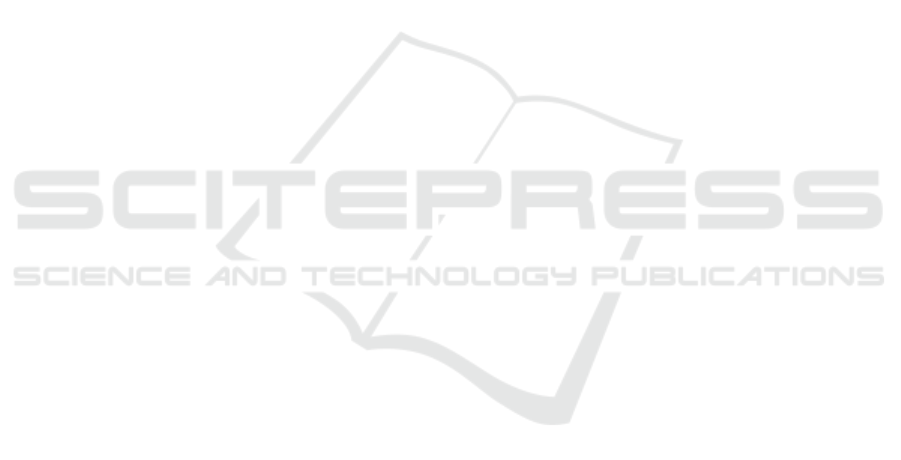
Grassmann, W. K. (2013). Computational probability, vol-
ume 24. Springer Science & Business Media.
Hjalmarsson, H., Gevers, M., and De Bruyne, F. (1996).
For model-based control design, closed-loop iden-
tification gives better performance. Automatica,
32(12):1659–1673.
Hosono, T. (1981). Numerical inversion of laplace trans-
form and some applications to wave optics. Radio
Science, 16(6):1015–1019.
Jansson, H. (2004). Experiment design with applications in
identification for control. PhD thesis, Royal Institute
of Technology (KTH), Stockholm, Sweden.
Khan, M. B., Munawar, K., and Nisar, H. (2013). Switched
hybrid position control of elastic systems with back-
lash. In 2013 IEEE International Conference on Con-
trol System, Computing and Engineering, pages 551–
556. IEEE.
Manabe, S. a. (1998). Coefficient diagram method. IFAC
Proceedings Volumes, 31(21):211–222.
Oomen, T., van Herpen, R., Quist, S., van de Wal,
M., Bosgra, O., and Steinbuch, M. (2013). Con-
necting system identification and robust control for
next-generation motion control of a wafer stage.
IEEE Transactions on Control Systems Technology,
22(1):102–118.
Risuleo, R. S. (2016). System identification with input un-
certainties: an EM kernel-based approach. PhD the-
sis, KTH Royal Institute of Technology.
Riva, M. H., Dagen, M., and Ortmaier, T. (2016). Adap-
tive unscented kalman filter for online state, parame-
ter, and process covariance estimation. In American
Control Conference (ACC), pages 4513–4519. IEEE.
Saha, P., Egerstedt, M., and Mukhopadhyay, S. (2021).
Neural identification for control. IEEE Robotics and
Automation Letters, 6(3):4648–4655.
Schr
¨
oder, D. (2015). Elektrische Antriebe-Regelung von
Antriebssystemen. Springer Vieweg, Berlin, Germany,
fourth edition.
Sch
¨
utte, F. (2003). Automatisierte Reglerinbetriebnahme
f
¨
ur elektrische Antriebe mit schwingungsf
¨
ahiger
Mechanik. Shaker.
Sch
¨
utte, F., Beineke, S., Grotstollen, H., Fr
¨
ohleke, N.,
Witkowski, U., R
¨
uckert, U., and R
¨
uping, S. (1997).
Structure-and parameter identification for a two-mass-
system with backlash and friction using a self-
organizing map. In European Conference on Power
Electronics and Applications, volume 3, pages 3–358.
Sysel, P. and Rajmic, P. (2012). Goertzel algorithm gen-
eralized to non-integer multiples of fundamental fre-
quency. Journal on Advances in Signal Processing
(EURASIP), 2012(1):1–8.
Tacx, P., de Rozario, R., and Oomen, T. (2021). Model order
selection in robust-control-relevant system identifica-
tion. In 19th IFAC Symposium on System Identifica-
tion, volume 54, pages 1–6. Elsevier.
Tan, N., Atherton, D. P., and Y
¨
uce, A. (2017). Computing
step and impulse responses of closed loop fractional
order time delay control systems using frequency re-
sponse data. International Journal of Dynamics and
Control, 5(1):30–39.
Tantau, M., Jonsky, T., Ziaukas, Z., and Jacob, H.-G.
(2022). Control-relevant model selection for servo
control systems. In International Conference on Con-
trol, Decision and Information Technologies, pages 1–
8, Istanbul, Turkey. IEEE. accepted.
Tantau, M., Popp, E., Perner, L., Wielitzka, M., and Ort-
maier, T. (2020). Model selection ensuring practi-
cal identifiability for models of electric drives with
coupled mechanics. In 21st International Federation
of Automatic Control (IFAC) World Congress, Berlin,
Germany.
Tkany, C., Grotjahn, M., and K
¨
uhn, J. (2020). Flatness-
based feedforward control of a stacker crane with
online trajectory generation. In 2020 4th Interna-
tional Conference on Automation, Control and Robots
(ICACR), pages 79–87. IEEE.
Toscano, R. and Lyonnet, P. (2009). Robust pid controller
tuning based on the heuristic kalman algorithm. Auto-
matica, 45(9):2099–2106.
Tripathi, S. M., Tiwari, A. N., and Singh, D. (2015). Op-
timum design of proportional-integral controllers in
grid-integrated pmsg-based wind energy conversion
system. International Transactions on Electrical En-
ergy Systems, 26(5):1006–1031.
Van den Hof, P. (1997). Closed-loop issues in system iden-
tification. IFAC Proceedings, 30(11):1547–1560.
Van Den Hof, P. M. J. and Schrama, R. J. P. (1994). Identifi-
cation and control-closed loop issues. IFAC Proceed-
ings, 27(8):311–323.
van Herpen, R., Oomen, T., and Bosgra, O. (2011). A
robust-control-relevant perspective on model order se-
lection. In Proceedings of the American Control Con-
ference, pages 1224–1229. IEEE.
van Herpen, R., Oomen, T., van de Wal, M., and Bosgra,
O. (2010). Experimental evaluation of robust-control-
relevance: A confrontation with a next-generation
wafer stage. In Proceedings of the American Control
Conference, pages 3493–3499. IEEE.
Vinnicombe, G. (2001). On closed-loop identification: er-
ror distributions in the ν-gap metric. In 40th IEEE
Conference on Decision and Control, volume 4, pages
3099–3103. IEEE.
Wertz, H. and Schutte, F. (2000). Self-tuning speed con-
trol for servo drives with imperfect mechanical load.
In IEEE Industry Applications Conference, volume 3,
pages 1497–1504. IEEE.
Witczak, M., Obuchowicz, A., and Korbicz, J. (2002). Ge-
netic programming based approaches to identification
and fault diagnosis of non-linear dynamic systems. In-
ternational Journal of Control, 75(13):1012–1031.
Yang, Z., Geng, L., and Yang, Y. (2018). A computation-
ally efficient eiv models identification method using
the v-gap metric. In 37th Chinese Control Conference
(CCC), pages 1729–1734. IEEE.
Zhang, G. and Furusho, J. (2000). Speed control of two-
inertia system by pi/pid control. IEEE Transactions
on industrial electronics, 47(3):603–609.
Control-relevant Model Selection for Multiple-mass Systems
615