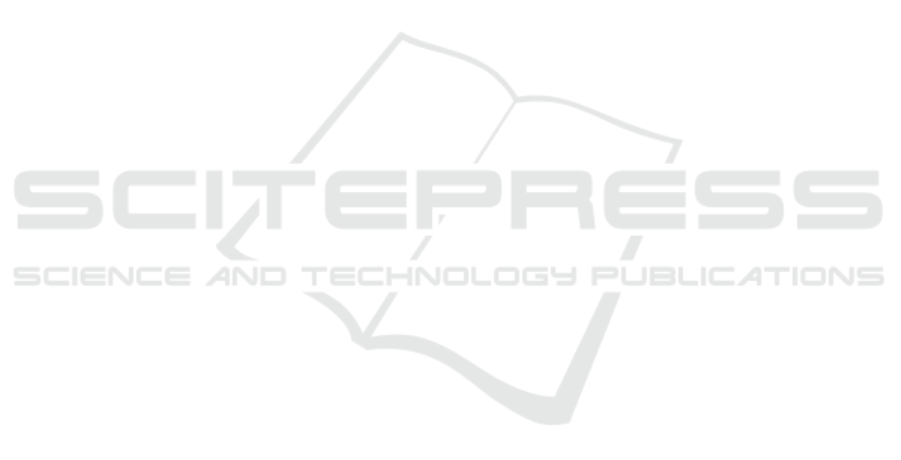
national Conference on Advanced Robotics (ICAR),
pages 128–133.
Chin, K., Hellebrekers, T., and Majidi, C. (2020). Machine
Learning for Soft Robotic Sensing and Control. Ad-
vanced Intelligent Systems, 2(6):1900171.
Cianchetti, M., Laschi, C., Menciassi, A., and Dario, P.
(2018). Biomedical applications of soft robotics. Na-
ture Reviews Materials, 3(6):143–153. Number: 6
Publisher: Nature Publishing Group.
Della Santina, C., Katzschmann, R. K., Biechi, A., and Rus,
D. (2018). Dynamic control of soft robots interact-
ing with the environment. In 2018 IEEE International
Conference on Soft Robotics (RoboSoft), pages 46–53.
Gazzola, M., Dudte, L. H., McCormick, A. G., and Ma-
hadevan, L. (2018). Forward and inverse problems in
the mechanics of soft filaments. Royal Society Open
Science, 5(6).
George Thuruthel, T., Ansari, Y., Falotico, E., and Laschi,
C. (2018). Control Strategies for Soft Robotic Ma-
nipulators: A Survey. Soft Robotics, 5(2):149–163.
Publisher: Mary Ann Liebert, Inc., publishers.
George Thuruthel, T., Falotico, E., Manti, M., Pratesi,
A., Cianchetti, M., and Laschi, C. (2017). Learning
closed loop kinematic controllers for continuum ma-
nipulators in unstructured environments. Soft robotics,
4(3):285–296.
Giorelli, M., Renda, F., Ferri, G., and Laschi, C. (2013). A
feed-forward neural network learning the inverse ki-
netics of a soft cable-driven manipulator moving in
three-dimensional space. In 2013 IEEE/RSJ Interna-
tional Conference on Intelligent Robots and Systems,
pages 5033–5039. ISSN: 2153-0866.
Kim, D., Kim, S.-H., Kim, T., Kang, B. B., Lee, M., Park,
W., Ku, S., Kim, D., Kwon, J., Lee, H., Bae, J., Park,
Y.-L., Cho, K.-J., and Jo, S. (2021). Review of ma-
chine learning methods in soft robotics. PLOS ONE,
16(2):e0246102. Publisher: Public Library of Sci-
ence.
Laschi, C., Mazzolai, B., and Cianchetti, M. (2016).
Soft robotics: Technologies and systems pushing
the boundaries of robot abilities. Science Robotics,
1(1):eaah3690. Publisher: American Association for
the Advancement of Science.
Mahl, T., Mayer, A. E., Hildebrandt, A., and Sawodny,
O. (2013). A variable curvature modeling approach
for kinematic control of continuum manipulators. In
2013 American Control Conference, pages 4945–
4950. ISSN: 2378-5861.
Naughton, N., Sun, J., Tekinalp, A., Parthasarathy, T.,
Chowdhary, G., and Gazzola, M. (2021). Elastica: A
Compliant Mechanics Environment for Soft Robotic
Control. IEEE Robotics and Automation Letters,
6(2):3389–3396. Conference Name: IEEE Robotics
and Automation Letters.
Piqu
´
e, F., Kalidindi, H. T., Fruzzetti, L., Laschi, C., Men-
ciassi, A., and Falotico, E. (2022). Controlling soft
robotic arms using continual learning. IEEE Robotics
and Automation Letters, 7(2):5469–5476.
Raptopoulos, F., Koskinopoulou, M., and Maniadakis, M.
(2020). Robotic Pick-and-Toss Facilitates Urban
Waste Sorting *. In 2020 IEEE 16th International
Conference on Automation Science and Engineering
(CASE), pages 1149–1154. ISSN: 2161-8089.
Rus, D. and Tolley, M. (2015). Design, fabrication and con-
trol of soft robots. Nature, 521:467–75.
Thuruthel, T. G., Falotico, E., Manti, M., and Laschi, C.
(2018). Stable Open Loop Control of Soft Robotic
Manipulators. IEEE Robotics and Automation Letters,
3(2):1292–1298. Conference Name: IEEE Robotics
and Automation Letters.
Thuruthel, T. G., Falotico, E., Renda, F., Flash, T.,
and Laschi, C. (2019). Emergence of behavior
through morphology: a case study on an octopus in-
spired manipulator. Bioinspiration & biomimetics,
14(3):034001.
Vannucci, L., Cauli, N., Falotico, E., Bernardino, A., and
Laschi, C. (2014). Adaptive visual pursuit involving
eye-head coordination and prediction of the target mo-
tion. In 2014 IEEE-RAS International Conference on
Humanoid Robots, pages 541–546.
Vannucci, L., Falotico, E., Di Lecce, N., Dario, P., and
Laschi, C. (2015). Integrating feedback and predic-
tive control in a bio-inspired model of visual pursuit
implemented on a humanoid robot. Lecture Notes in
Computer Science (including subseries Lecture Notes
in Artificial Intelligence and Lecture Notes in Bioin-
formatics), 9222:256–267.
Wales, D. J. and Doye, J. P. K. (1997). Global Opti-
mization by Basin-Hopping and the Lowest Energy
Structures of Lennard-Jones Clusters Containing up
to 110 Atoms. The Journal of Physical Chemistry A,
101(28):5111–5116. Publisher: American Chemical
Society.
Zeng, A., Song, S., Lee, J., Rodriguez, A., and Funkhouser,
T. (2020). TossingBot: Learning to Throw Arbitrary
Objects with Residual Physics. arXiv:1903.11239 [cs,
stat]. arXiv: 1903.11239.
Zhang, X., Chan, F. K., Parthasarathy, T., and Gazzola, M.
(2019). Modeling and simulation of complex dynamic
musculoskeletal architectures. Nature Communica-
tions, 10(1):undefined–undefined. Number: 1.
Zlatintsi, A., Dometios, A. C., Kardaris, N.,
Rodomagoulakis, I., Koutras, P., Papageorgiou,
X., Maragos, P., Tzafestas, C. S., Vartholomeos, P.,
Hauer, K., Werner, C., Annicchiarico, R., Lombardi,
M. G., Adriano, F., Asfour, T., Sabatini, A. M.,
Laschi, C., Cianchetti, M., G
¨
uler, A., Kokkinos, I.,
Klein, B., and L
´
opez, R. (2020). I-Support: A robotic
platform of an assistive bathing robot for the elderly
population. Robotics and Autonomous Systems,
126:103451.
Open-loop Control of a Soft Arm in Throwing Tasks
145