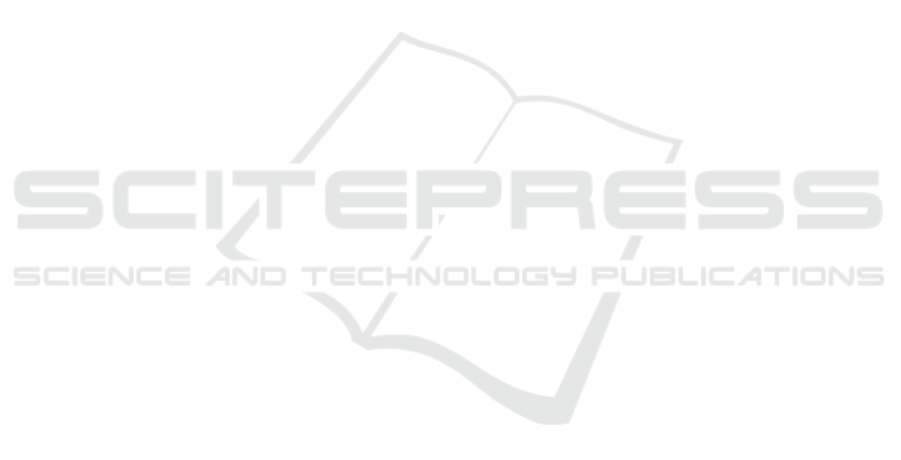
be extended from zero load to loaded cases after us-
ing the state equations from the geometrically exact
model (Rucker et al., 2010). The presented objectives
may have less conflicting effect on each other when
highly flexible CTCRs with more tubes are used. In
such situations, they have multiple configurations for
any required objective and the conflicting objectives
could find a compromise solution satisfying the re-
quirements. However, it is computationally complex
to solve problems with more than three tubes. Obsta-
cle avoidance can be considered by including the ob-
jective function (Lyons et al., 2009; Flaßkamp et al.,
2019) to the presented framework.
ACKNOWLEDGEMENTS
The research of Dhanakoti and Maddocks has been
funded by the Einstein Foundation Berlin.
REFERENCES
Alfalahi, H., Renda, F., and Stefanini, C. (2020). Concentric
tube robots for minimally invasive surgery: Current
applications and future opportunities. IEEE Trans.
Med. Robot. Bion.
Baykal, C., Torres, L. G., and Alterovitz, R. (2015). Opti-
mizing design parameters for sets of concentric tube
robots using sampling-based motion planning. In
2015 IEEE/RSJ International Conference on Intelli-
gent Robots and Systems (IROS), pages 4381–4387.
Bergeles, C., Gosline, A. H. C., Vasilyev, N. V., Codd,
P. J., del Nido, P. J., and Dupont, P. E. (2015). Con-
centric tube robot design and optimization based on
task and anatomical constraints. IEEE Transactions
on Robotics, 31:67–84.
Betts, J. T. (2010). Practical Methods for Optimal Control
and Estimation Using Nonlinear Programming, Sec-
ond Edition. Society for Industrial and Applied Math-
ematics, second edition.
Burgner, J., Rucker, D. C., Gilbert, H. B., Swaney, P. J.,
Russell, P. T., Weaver, K. D., and Webster, R. J.
(2013). A telerobotic system for transnasal surgery.
IEEE/ASME transactions on mechatronics : a joint
publication of the IEEE Industrial Electronics Soci-
ety and the ASME Dynamic Systems and Control Di-
vision, 19(3):996—1006.
Burgner, J., Swaney, P. J., Rucker, D. C., Gilbert, H. B.,
Nill, S. T., Russell, P. T., Weaver, K. D., and Webster
III, R. J. (2011). A bimanual teleoperated system for
endonasal skull base surgery. In 2011 IEEE/RSJ In-
ternational Conference on Intelligent Robots and Sys-
tems, pages 2517–2523.
Dichmann, D. J., Li, Y., and Maddocks, J. H. (1996).
Hamiltonian formulations and symmetries in rod me-
chanics. In Mesirov, J. P., Schulten, K., and Sumners,
D. W., editors, Mathematical approaches to biomolec-
ular structure and dynamics, pages 71–113. Springer.
Flaßkamp, K., Worthmann, K., M
¨
uhlenhoff, J., Greiner-
Petter, C., B
¨
uskens, C., Oertel, J., Keiner, D., and Sat-
tel, T. (2019). Towards optimal control of concentric
tube robots in stereotactic neurosurgery. Mathemati-
cal and Computer Modelling of Dynamical Systems,
25(6):560–574.
Garriga-Casanovas, A. and y Baena, F. R. (2018). Com-
plete follow-the-leader kinematics using concentric
tube robots. The International Journal of Robotics Re-
search, 37(1):197–222.
Gilbert, H. B., Hendrick, R. J., and Webster, R. J. (2016).
Elastic stability of concentric tube robots: A stabil-
ity measure and design test. IEEE transactions on
robotics : a publication of the IEEE Robotics and Au-
tomation Society, 32(1):20–35.
Gilbert, H. B., Neimat, J., and Webster, R. J. (2015). Con-
centric tube robots as steerable needles: Achieving
follow-the-leader deployment. IEEE Transactions on
Robotics, 31(2):246–258.
Granna, J., Godage, I. S., Wirz, R., Weaver, K. D., Webster,
R. J., and Burgner-Kahrs, J. (2016). A 3-d volume
coverage path planning algorithm with application to
intracerebral hemorrhage evacuation. IEEE Robotics
and Automation Letters, 1(2):876–883.
Griewank, A. and Walther, A. (2000). Evaluating deriva-
tives - principles and techniques of algorithmic dif-
ferentiation, second edition. In Frontiers in applied
mathematics.
Kierzenka, J. A. and Shampine, L. F. (2008). A BVP solver
that controls residual and error. JNAIAM J. Numer.
Anal. Ind. Appl. Math, pages 1–2.
Lyons, L. A., Webster, R. J., and Alterovitz, R. (2009). Mo-
tion planning for active cannulas. In 2009 IEEE/RSJ
International Conference on Intelligent Robots and
Systems, pages 801–806.
Nocedal, J. and Wright, S. (2006). Numerical Optimization.
Springer.
Rucker, D. C., Jones, B. A., and Webster III, R. J. (2010).
A geometrically exact model for externally loaded
concentric-tube continuum robots. IEEE transactions
on robotics : a publication of the IEEE Robotics and
Automation Society, 26(5):769–780.
Rucker, D. C. and Webster, R. J. (2011). Computing Jaco-
bians and compliance matrices for externally loaded
continuum robots. In 2011 IEEE International Con-
ference on Robotics and Automation, pages 945–950.
Rucker, D. C., Webster III, R. J., Chirikjian, G. S., and
Cowan, N. J. (2010). Equilibrium conformations of
concentric-tube continuum robots. The International
Journal of Robotics Research, 29(10):1263–1280.
Yip, M. C., Sganga, J., and Camarillo, D. B. (2017).
Autonomous control of continuum robot manipula-
tors for complex cardiac ablation tasks. J. Medical
Robotics Res., 2:1750002:1–1750002:13.
ICINCO 2022 - 19th International Conference on Informatics in Control, Automation and Robotics
154