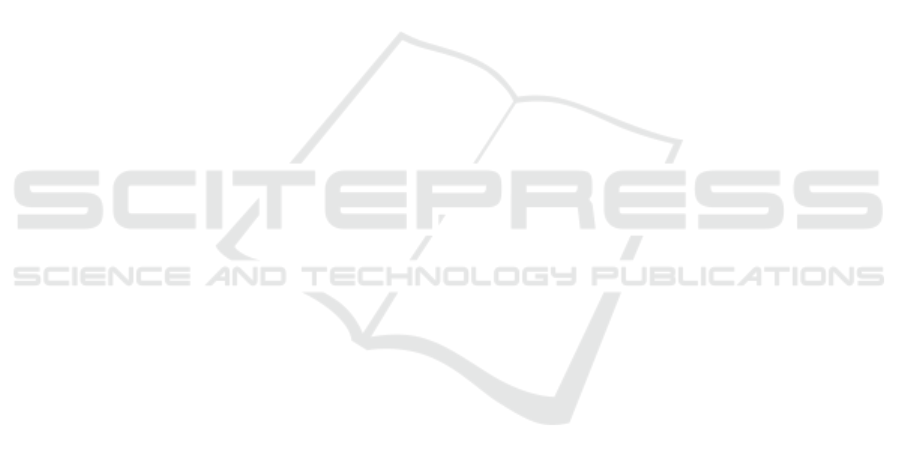
Boudjadar, J., Jin, H. K., Larsen, K., and Nyman, U.
(2014b). Compositional schedulability analysis of an
avionics system using uppaal. In International Con-
ference on Advanced Aspects of Software Engineer-
ing, pages 111–132.
Boudjadar, J. and Khooban, M. H. (2021). A safety-driven
cost optimization for the real-time operation of a hy-
brid energy system. In Proceedings of the 27th Intl.
Conf. ICSEng 2020.
Clarke, E. M., Klieber, W., Nov
´
a
ˇ
cek, M., and Zuliani,
P. (2012). Model Checking and the State Explosion
Problem. Springer Berlin Heidelberg.
Domke, J. (2012). Generic methods for optimization-based
modeling. In Proceedings of the Intl. Conf. on Ar-
tificial Intelligence and Statistics, volume 22, pages
318–326.
Eyring, V., K
¨
ohler, H. W., Lauer, A., and Lemper,
B. (2005). Emissions from international shipping:
2. impact of future technologies on scenarios un-
til 2050. Journal of Geophysical Research: Atmo-
spheres, 110(D17).
Fitzgerald, J. S., Larsen, P. G., and Pierce, K. G. (2019).
Multi-modelling and co-simulation in the engineering
of cyber-physical systems: Towards the digital twin.
In From Software Engineering to Formal Methods and
Tools, and Back, LNCS Springer, pages 40–55.
Frangopoulos, C. A. (2018). Recent developments and
trends in optimization of energy systems. Energy,
164:1011–1020.
Garc
´
ıa-Gusano, D., Garra
´
ın, D., and Dufour, J. (2017).
Prospective life cycle assessment of the spanish elec-
tricity production. Renewable and Sustainable Energy
Reviews, 75:21–34.
Haq, A. U. and G, S. R. (2016). Low power vlsi archi-
tectures for digital pid controller applications. In-
ternational Journal of Advanced Research in Electri-
cal, Electronics and Instrumentation Engineering, 5-
3:903–910.
He, R., Chen, G., Dong, C., Sun, S., and Shen, X. (2019).
Data-driven digital twin technology for optimized
control in process systems. ISA Transactions, 95:221–
234.
Herr, N., Nicod, J., and Varnier, C. (2014). Prognostics-
based scheduling in a distributed platform: Model,
complexity and resolution. In CASE’14, pages 1054–
1059.
Herr, N., Nicod, J.-M., Varnier, C., Jardin, L., Sorrentino,
A., Hissel, D., and P
´
era, M.-C. (2017). Decision pro-
cess to manage useful life of multi-stacks fuel cell
systems under service constraint. Renewable Energy,
105:590 – 600.
Labandeira, X., Labeaga, J. M., Linares, P., and L
´
opez-
Otero, X. (2020). The impacts of energy efficiency
policies: Meta-analysis. Energy Policy, 147:111790.
Letafat, A., Rafiei, M., Ardeshiri, M., Sheikh, M., Banaei,
M., Boudjadar, J., and Khooban, M. H. (2020). An
efficient and cost-effective power scheduling in zero-
emission ferry ships. Complex., 2020:6487873:1–
6487873:12.
Odeim, F., Roes, J., and Heinzel, A. (2015). Power
management optimization of an experimental fuel
cell/battery/supercapacitor hybrid system. Energies,
8(7):6302–6327.
Peng, J., He, H., and Xiong, R. (2017). Rule based energy
management strategy for a series–parallel plug-in hy-
brid electric bus optimized by dynamic programming.
Applied Energy, 185:1633 – 1643. Clean, Efficient
and Affordable Energy for a Sustainable Future.
Rafiei, M., Boudjadar, J., and Khooban, M.-H. (2021). En-
ergy management of a zero-emission ferry boat with a
fuel-cell-based hybrid energy system: Feasibility as-
sessment. IEEE Transactions on Industrial Electron-
ics, 68(2):1739–1748.
Rodrigues, G. S., Esp
´
ındola Ferreira, J. C., and Rocha, C. R.
(2018). A novel method for analysis and optimization
of electric energy consumption in manufacturing pro-
cesses. Procedia Manufacturing, 17:1073–1081.
Suslov, K., Piskunova, V., Gerasimov, D., Ukolova, E.,
Akhmetshin, A., Lombardi, P., and Komarnicki, P.
(2019). Development of the methodological basis of
the simulation modelling of the multi-energy systems.
In Proceedings of E3S Web Conf., volume 124.
Teng, S. Y., Tou
ˇ
s, M., Leong, W. D., How, B. S., Lam,
H. L., and M
´
a
ˇ
sa, V. (2021). Recent advances on in-
dustrial data-driven energy savings: Digital twins and
infrastructures. Renewable and Sustainable Energy
Reviews, 135:110208.
van Biert, L., Godjevac, M., Visser, K., and Aravind, P.
(2016). A review of fuel cell systems for maritime
applications. Journal of Power Sources, 327:345 –
364.
Wang, R., Zhou, X., Dong, L., Wen, Y., Tan, R., Chen, L.,
Wang, G., and Zeng, F. (2020a). Kalibre: Knowledge-
based neural surrogate model calibration for data cen-
ter digital twins. In Proceedings of BuildSys 20.
Wang, W., Li, X., Xie, L., Lv, H., and Lv, Z. (2021). Un-
manned aircraft system airspace structure and safety
measures based on spatial digital twins. IEEE Trans-
actions on Intelligent Transportation Systems, pages
1–10.
Wang, Y., Huang, C., and Zhu, Q. (2020b). Energy-efficient
control adaptation with safety guarantees for learning-
enabled cyber-physical systems. In Intl. Conf. on
Computer-Aided Design.
Wei, C., Xu, X., Zhang, Y., Li, X., and Bai, X. (2019). A
survey on optimal control and operation of integrated
energy systems. Complex., 2019.
Wu, B., Widanage, W. D., Yang, S., and Liu, X. (2020).
Battery digital twins: Perspectives on the fusion of
models, data and artificial intelligence for smart bat-
tery management systems. Energy and AI, 1:100016.
Yu, J., Zhang, T., and Qian, J. (2011). Energy-efficiency
standards of electrical motor products. In Electrical
Motor Products, pages 51–172.
Zhang, W., Li, J., Xu, L., and Ouyang, M. (2017). Op-
timization for a fuel cell/battery/capacity tram with
equivalent consumption minimization strategy. En-
ergy Conversion and Management, 134:59 – 69.
ICINCO 2022 - 19th International Conference on Informatics in Control, Automation and Robotics
168