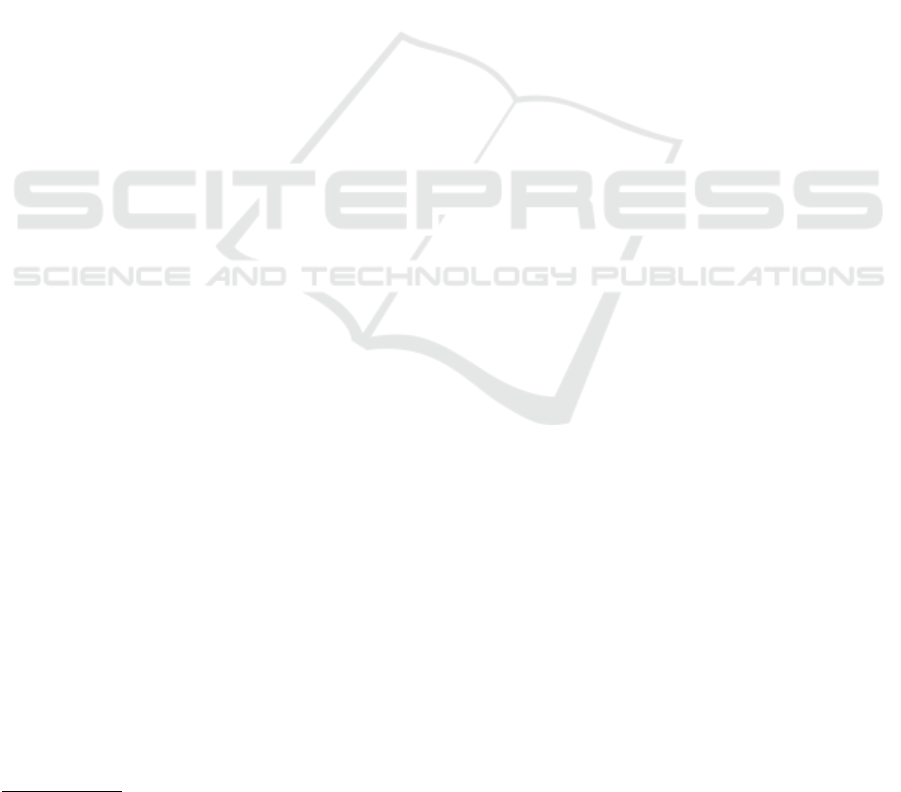
5 CONCLUSION
This paper has depicted the use of NetLogo to
model and simulate a factory producing according
to the job-shop manufacturing principle. We con-
tributed SwarmFabSim, a modular simulation frame-
work written in NetLogo that can apply various al-
gorithms to optimize a make-to-order manufacturing
system and supports multiple configurable scenarios.
The evaluation framework was used to assess the ef-
fectiveness of an artificial hormone algorithm com-
pared to a naïve basic implementation and a reference
baseline algorithm. The evaluation was based on three
key performance indicators: Flow factor, delay, and
utilization. The simulations show promising results
of the artificial hormone algorithm in three reference
scenarios with significant improvements over the ref-
erence algorithms. The implementation of the simula-
tion environment is published as open source in a Git
repository
13
. Readers are welcome to contribute with
their ideas and developments.
ACKNOWLEDGEMENT
This work was performed in the course of project
ML&Swarms supported by KWF-React EU under
contract number KWF-20214|34789|50819.
REFERENCES
Alves, F., Varela, M. L. R., Rocha, A. M. A., Pereira, A. I.,
Barbosa, J., and Leitão, P. (2018). Hybrid system
for simultaneous job shop scheduling and layout opti-
mization based on multi-agents and genetic algorithm.
In International Conference on Hybrid Intelligent Sys-
tems, pages 387–397. Springer.
Bagheri, A., Zandieh, M., Mahdavi, I., and Yazdani, M.
(2010). An artificial immune algorithm for the flex-
ible job-shop scheduling problem. Future Generation
Computer Systems, 26(4):533–541.
Dias, L. M., Vieira, A. A., Pereira, G. A., and Oliveira,
J. A. (2016). Discrete simulation software ranking—a
top list of the worldwide most popular and used tools.
In 2016 Winter Simulation Conference, pages 1060–
1071. IEEE.
Dorigo, M. and Stützle, T. (2004). Ant Colony Optimiza-
tion. A Bradford Book, The MIT Press.
Elmenreich, W. and de Meer, H. (2008). Self-organizing
networked systems for technical applications: A dis-
cussion on open issues. In K.A. Hummel, J. S., editor,
Proceedings of the Third International Workshop on
Self-Organizing Systems, pages 1–9. Springer Verlag.
13
https://swarmfabsim.github.io
Elmenreich, W., D’Souza, R., Bettstetter, C., and de Meer,
H. (2009). A survey of models and design methods for
self-organizing networked systems. In Proceedings of
the Fourth International Workshop on Self-Organizing
Systems, volume LNCS 5918, pages 37–49. Springer
Verlag.
Elmenreich, W., Schnabl, A., and Schranz, M. (2021).
An artificial hormone-based algorithm for production
scheduling from the bottom-up. In Proceedings of the
13th International Conference on Agents and Artifi-
cial Intelligence. SciTePress.
Garey, M. R., Johnson, D. S., and Sethi, R. (1976).
The complexity of flowshop and jobshop scheduling.
Mathematics of Operations Research, 1(2):117–129.
Geng, H., editor (2018). Semiconductor Manufacturing
Handbook. McGraw-Hill Education.
Gunaratne, C. and Garibay, I. (2021). NL4Py: Agent-
based modeling in Python with parallelizable NetL-
ogo workspaces. SoftwareX, 16:100801.
Gwiazda, A., Bana
´
s, W., S˛ekala, A., Topolska, S., and
Hryniewicz, P. (2020). Modelling of production pro-
cess using multiple ant colony approach. Interna-
tional Journal of Modern Manufacturing Technolo-
gies, XII(1):201–213.
Habib Zahmani, M. and Atmani, B. (2021). Multiple dis-
patching rules allocation in real time using data min-
ing, genetic algorithms, and simulation. Journal of
Scheduling, 24(2):175–196.
Heylighen, F. (2001). The science of self-organization and
adaptivity. The Encyclopedia of Life Support Systems,
5(3):253–280.
Lawler, E. L., Lenstra, J. K., Kan, A. H. R., and Shmoys,
D. B. (1993). Sequencing and scheduling: Algorithms
and complexity. Handbooks in Operations Research
and Management Science, 4:445–522.
Prehofer, C. and Bettstetter, C. (2005). Self-organization
in communication networks: Principles and design
paradigms. IEEE Communications Magazine, pages
78–85.
Pulikottil, T., Estrada-Jimenez, L. A., Rehman, H. U.,
Barata, J., Nikghadam-Hojjati, S., and Zarzycki, L.
(2021). Multi-agent based manufacturing: current
trends and challenges. In 2021 26th IEEE Interna-
tional Conference on Emerging Technologies and Fac-
tory Automation (ETFA), pages 1–7. IEEE.
Railsback, S., Ayllón, D., Berger, U., Grimm, V., Lytinen,
S., Sheppard, C., and Thiele, J. C. (2017). Improving
execution speed of models implemented in netlogo.
Journal of Artificial Societies and Social Simulation.
Railsback, S. F. and Grimm, V. (2019). Agent-based and
individual-based modeling: a practical introduction.
Princeton university press, "2nd" edition.
Schranz, M., Umlauft, M., and Elmenreich, W. (2021).
Bottom-up job shop scheduling with swarm intelli-
gence in large production plants. In Proceedings of
the 11th International Conference on Simulation and
Modeling Methodologies, Technologies and Applica-
tions, pages 327–334.
Schranz, M., Umlauft, M., Sende, M., and Elmenreich, W.
(2020). Swarm robotic behaviors and current applica-
tions. Frontiers in Robotics and AI, 7:36.
SIMULTECH 2022 - 12th International Conference on Simulation and Modeling Methodologies, Technologies and Applications
278