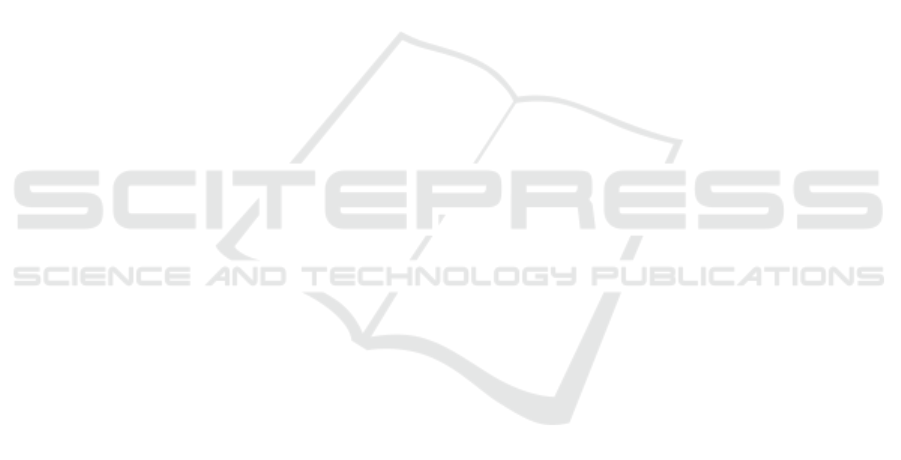
Chan, T. and Vese, L. (2001). Active contours with-
out edges. IEEE Transactions on Image Processing,
10(2), pages 266—-277.
Clegg, A., Yu, W., Erickson, Z., Tan, J., Liu, C., and Turk,
G. (2017). Learning to navigate cloth using haptics. In
IEEE International Conference on Intelligent Robots
and Systems, pages 2799–2805. Institute of Electrical
and Electronics Engineers Inc.
Cohen, L. D. (1991). On active contour models and bal-
loons. CVGIP: Image Understanding, vol. 53, no. 2,
pages 211–218.
Coleman, D., Sucan, I., Chitta, S., and Correll, N. (2014).
Reducing the barrier to entry of complex robotic soft-
ware: a moveit! case study. pages 1–14.
Ganesan, P., Rajini, V., and Rajkumar, R. (2010). Segmen-
tation and edge detection of color images using cielab
color space and edge detectors. In International Con-
ference on ”Emerging Trends in Robotics and Com-
munication Technologies”, INTERACT-2010. IEEE.
Gil, P., Mateo, C. M., Delgado,
´
A., and Torres, F. (2016).
Visual/Tactile sensing to monitor grasps with robot-
hand for planar elastic objects. 47th International
Symposium on Robotics, ISR 2016, 2016:439–445.
Kampouris, C., Mariolis, I., Peleka, G., E. Skartados, E.,
Kargakos, A., Triantafyllou, D., and Malassiotis, S.
(2016). Multi-sensorial and explorative recognition
of garments and their material properties in uncon-
strained environment. In IEEE International Con-
ference on Robotics and Automation (ICRA), pages
1656–1663. IEEE.
Kass, M., Witkin, A., and Terzopoulos, D. (1988). Snakes:
Active contour models. International Journal of Com-
puter Vision, 1(4), pages 321—-331.
Marquez-Neila, P., Baumela, L., and Alvarez, L. (2014). A
morphological approach to curvature-based evolution
of curves and surfaces. In IEEE Transactions on Pat-
tern Analysis and Machine Intelligence, 36(1), pages
2—-17.
Mira, D., Delgado, A., Mateo, C. M., Puente, S. T., Can-
delas, F. A., and Torres, F. (2015). Study of dexter-
ous robotic grasping for deformable objects manipu-
lation. 2015 23rd Mediterranean Conference on Con-
trol and Automation, MED 2015 - Conference Pro-
ceedings, pages 262–266.
Petr
´
ık, V., Smutn
´
y, V., Krsek, P., and Hlav
´
a
ˇ
c, V. (2017).
Single arm robotic garment folding path generation.
Advanced Robotics, 31(23-24):1325–1337.
Quigley, M., Gerkey, B., Conley, K., Faust, J., Foote, T.,
Leibs, J., Berger, E., Wheeler, R., and Ng, A. (2009).
Ros: an open-source robot operating system. In IEEE
Intl. Conf. on Robotics and Automation (ICRA) Work-
shop on Open Source Robotics.
Ramisa, A., Alenya, G., Moreno-Noguer, F., and Torras, C.
(2011). Determining where to grasp cloth using depth
information. Frontiers in Artificial Intelligence and
Applications, 232:199–207.
Rusu, R. B. and Cousins, S. (2011). 3d is here: Point cloud
library (pcl). In IEEE International Conference on
Robotics and Automation, pages 19–22.
Shehawy, H., Rocco, P., and Zanchettin, A. (2021). Estimat-
ing a garment grasping point for robot. In 20th Inter-
national Conference on Advanced Robotics (ICAR).
IEEE.
Stria, J., Prusa, D., Hlavac, V., Wagner, L., Petrik, V., Krsek,
P., and Smutny, V. (2014). Garment perception and
its folding using a dual-arm robot. IEEE Interna-
tional Conference on Intelligent Robots and Systems,
(September):61–67.
Sun, L., Aragon-Camarasa, G., Rogers, S., and Siebert,
J. P. (2018). Autonomous Clothes Manipulation Us-
ing a Hierarchical Vision Architecture. IEEE Access,
6(October):76646–76662.
Sural, S., Qian, G., and Pramanik, S. (2002). Segmentation
and histogram generation using the hsv color space for
image retrieval. In IEEE International Conference on
Image Processing, pages 589–592.
Wang, J. and Olson, E. (2016). Apriltag 2: Efficient and ro-
bust fiducial detection,. In IEEE International Confer-
ence on Intelligent Robots and Systems, pages 4193—
-4198.
Willimon, B., Birchfield, S., and Walker, I. (2011a). Clas-
sification of clothing using interactive perception. In
IEEE International Conference on Robotics and Au-
tomation, pages 1862–1868.
Willimon, B., Birchfield, S., and Walker, I. (2011b). Model
for unfolding laundry using interactive perception. In
EEE International Conference on Intelligent Robots
and Systems, pages 4871–4876. IEEE.
Yamazaki, K., Nagahama, K., and Inaba, M. (2011). Daily
clothes observation from visible surfaces based on
wrinkle and cloth-overlap detection. Proceedings of
the 12th IAPR Conference on Machine Vision Appli-
cations, MVA 2011, pages 275–278.
Yamazaki, K., Oya, R., Nagahama, K., Okada, K., and In-
aba, M. (2014). Bottom dressing by a life-sized hu-
manoid robot provided failure detection and recovery
functions. 2014 IEEE/SICE International Symposium
on System Integration, SII 2014, pages 564–570.
Yamazaki, K., Ueda, R., Nozawa, S., Mori, Y., Maki, T.,
Hatao, N., Okada, K., and Inaba, M. (2010). Sys-
tem integration of a daily assistive robot and its ap-
plication to tidying and cleaning rooms. IEEE/RSJ
2010 International Conference on Intelligent Robots
and Systems, IROS 2010 - Conference Proceedings,
pages 1365–1371.
Yuan, W., Mo, Y., Wang, S., and Adelson, E. H. (2018).
Active clothing material perception using tactile sens-
ing and deep learning. In IEEE International Con-
ference on Robotics and Automation (ICRA), pages
4842–4849. IEEE.
Yuen, H., Princen, J., Illingworth, J., and Kittler, J.
(1990). Comparative study of hough transform meth-
ods for circle finding. Image and Vision Computing,
8(1):7177.
ICINCO 2022 - 19th International Conference on Informatics in Control, Automation and Robotics
450