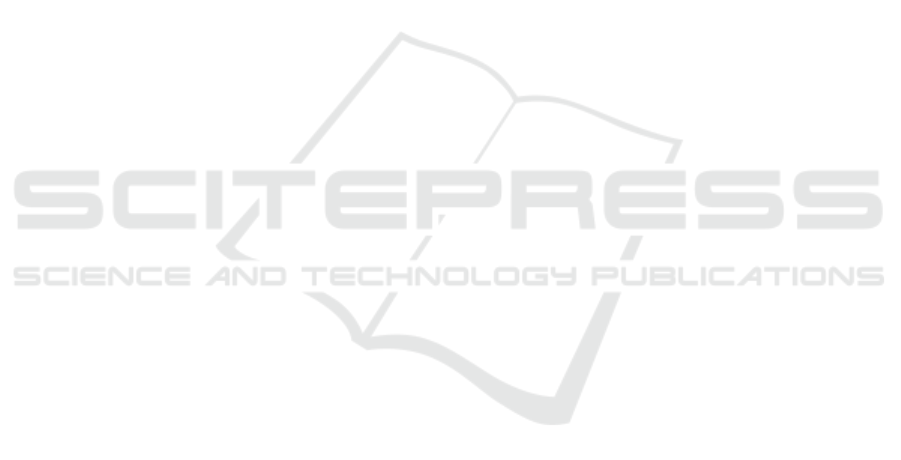
sistance level so that the operator’s workload is pro-
gressively reduced until only potential intervention is
required. The first step of gradual autonomization
describes an assisted operation (Florian Petit, 2020).
All repetitive tasks are performed automatically. In
this case, the robot arm poses for achieving the park-
ing position, operation pose or even the folding pro-
cedure as shown in Figure 6 will be performed au-
tonomously. Furthermore, safety strategies concern-
ing collisions or communication loss are being imple-
mented. Level 2 describes an autopilot that is capable
of independently performing certain tasks under op-
timal conditions. Applied to this project, this means
the autonomous navigation of the start to the end point
of the measurements, whereby more complicated pro-
cesses, such as crossing security gates and navigating
through environments with obstacles, will not be in-
cluded yet. Therefore the operator is required to mon-
itor the situation at all times. Level 3 describes a com-
pletely autonomous execution of all steps of the oper-
ation. The user is only informed in critical situations
and is also given a buffer time to react appropriately to
the situation. Thus, this stage of development would
include all tasks of the survey, from mission prepara-
tion, measurement acquisition and security gate cross-
ing to the successful completion of the survey and de-
activation of the robot. In addition, security strategies
will be developed to take effect in case of execution
errors and will either correct the problem itself or give
the user time to intervene.
REFERENCES
Alessandro Masi (2017). Train inspector monorail- tim,
url: https://cds.cern.ch/record/2260825/?ln=de (ac-
cessed 28.02.2022).
Castro, M. D., Tambutti, M. L. B., Ferre, M., Losito, R.,
Lunghi, G., and Masi, A. (2018). i-tim: A robotic sys-
tem for safety, measurements, inspection and main-
tenance in harsh environments. In 2018 IEEE Inter-
national Symposium on Safety, Security, and Rescue
Robotics, SSRR 2018, Philadelphia, PA, USA, August
6-8, 2018, pages 1–6. IEEE.
Catherall, R., Andreazza, W., Breitenfeldt, M., Dorsival, A.,
Focker, G., Gharsa, T., Giles, T., Grenard, J.-L., Locci,
F., Martins, P., Marzari, S., Schipper, J., Shornikov,
A., and Stora, T. (2017). The isolde facility. Journal
of Physics G: Nuclear and Particle Physics, 44.
CERN (2006). Code de s
´
ecurit
´
e safety code. CERN.
CERN (2022). Accelerators, url: https://home.cern/science/
accelerators (accessed 28.02.2022).
D. Forkel-Wirth, M. Silari (Editors) (2010). Radi-
ation protection group annual report 2009, url:
https://cds.cern.ch/record/2221663/files/annrep-rp-
2009.pdf (accessed 28.02.2022).
Di Castro, M., Ferre, M., and Masi, A. (2018). Cern-
tauro: A modular architecture for robotic inspection
and telemanipulation in harsh and semi-structured en-
vironments. IEEE Access, 6:37506–37522.
Florian Petit (2020). The next step in autonomous driving,
url: https://www.blickfeld.com/blog/the-next-step-in-
autonomous-driving (accessed 28.02.2022).
Forkel-Wirth, D., Roesler, S., Silari, M., Streit-Bianchi, M.,
Theis, C., Vincke, H., and Vincke, H. (2013). Radia-
tion protection at cern. CERN.
ICRP (1991). 1990 recommendations of the international
commission on radiological protection. icrp publica-
tion 60 (users edition). ICRP.
Kershaw, K., Feral, B., Grenard, J.-L., Feniet, T., De, S.,
Hazelaar-Bal, C., Bertone, C., and Ingo, R. (2013).
Remote inspection, measurement and handling for
maintenance and operation at cern. International
Journal of Advanced Robotic Systems, 10:1.
Kim, J.-H., Lee, J.-C., and Choi, Y.-R. (2014). Larob:
Laser-guided underwater mobile robot for reactor ves-
sel inspection. IEEE/ASME Transactions on Mecha-
tronics, 19:1–10.
Lunghi, G., Marin, R., Di Castro, M., Masi, A., and Sanz,
P. J. (2019). Multimodal human-robot interface for
accessible remote robotic interventions in hazardous
environments. IEEE Access, 7:127290–127319.
Michelle Starr (2022). Lunar rover discovers mys-
terious glass spheres on the far side of the
moon, url: https://www.sciencealert.com/the-moon-
has-glass-balls (accessed 28.02.2022).
Park, J., Kim, S., Kim, J., and Kim, S. (2010). Driving
control of mobile robot with mecanum wheel using
fuzzy inference system. In ICCAS 2010, pages 2519–
2523.
Pi, R., Cie
´
slak, P., Ridao, P., and Sanz, P. J. (2021). Twin-
bot: Autonomous underwater cooperative transporta-
tion. IEEE Access, 9:37668–37684.
Prados Sesmero, C., Buonocore, L. R., and Di Castro, M.
(2021). Omnidirectional robotic platform for surveil-
lance of particle accelerator environments with limited
space areas. Applied Sciences, 11(14).
Rubino, E. M., Centelles, D., Sales, J., Marti, J. V., Marin,
R., Sanz, P. J., and Alvares, A. J. (2017). Progressive
image compression and transmission with region of
interest in underwater robotics. In OCEANS 2017 -
Aberdeen, pages 1–9.
Veiga Almagro, C., Lunghi, G., Di Castro, M., Cen-
telles Beltran, D., Mar
´
ın Prades, R., Masi, A., and
Sanz, P. J. (2020). Cooperative and multimodal ca-
pabilities enhancement in the cerntauro human–robot
interface for hazardous and underwater scenarios. Ap-
plied Sciences, 10(17).
ICINCO 2022 - 19th International Conference on Informatics in Control, Automation and Robotics
458