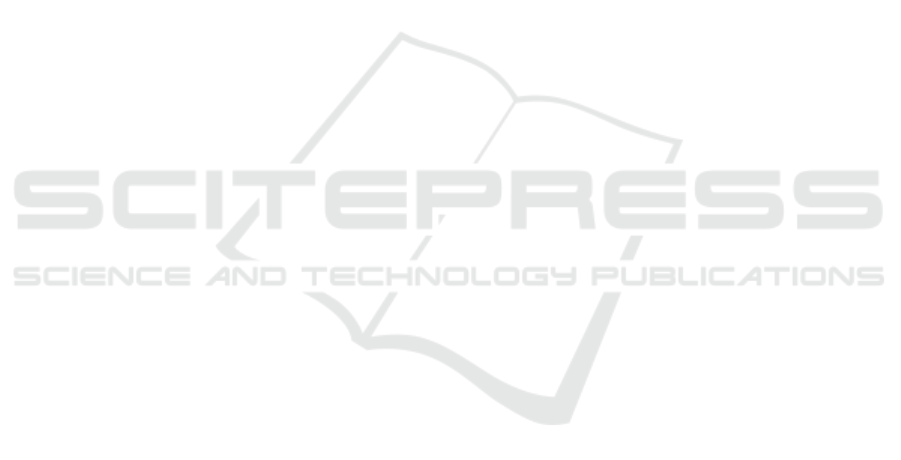
bination of springs is integrated. Springs’ fixation
points can be adjusted to produce a counter-torque
that can statically balance a range of applied exter-
nal forces. The design of this compensator shows that
torque due to payload can be decoupled and compen-
sated with a combination of linear springs. Variation
of payload can be compensated by adjusting the dis-
tance of one of the springs’ fixation points. The ratio
between the range of the payload and the distance that
can be spanned by the fixation point can determine
the value of the spring coefficient. The paper presents
the use of the compensator with a 2-DoF manipula-
tor. The simulation shows that a complete compen-
sation of constant payload can be achieved around the
whole workspace. The adaptation feature allows com-
plete compensation in case the payload has changed.
The design of this system is very complex yet, possi-
ble. This system can be very useful in repetitive tasks
with constant payload while having the advantage of
readjusting for different tasks with different payloads.
The advantage of this system is that it reduces energy
consumed to support payload as the robot’s actuators
need only to support dynamic torques.
In the future, it will be necessary to use this com-
pensator with manipulators with more than 2-DoF and
to test it on real hardware.
ACKNOWLEDGEMENTS
This work was supported by Russian Scientific Foun-
dation (Project number 22-41-02006).
REFERENCES
Agrawal, S. K. and Fattah, A. (2004). Gravity-balancing of
spatial robotic manipulators. volume 39, pages 1331–
1344. Elsevier Ltd.
Arakelian, V. (2016). Gravity compensation in robotics. Ad-
vanced Robotics, 30:79–96.
Arakelian, V., Dahan, M., and Smith, M. (2000). A histor-
ical review of the evolution of the theory on balanc-
ing of mechanisms. In Ceccarelli, M., editor, Interna-
tional Symposium on History of Machines and Mecha-
nisms Proceedings HMM 2000, pages 291–300, Dor-
drecht. Springer Netherlands.
Cho, C. and Kang, S. (2014). Design of a static balanc-
ing mechanism for a serial manipulator with an un-
constrained joint space using one-dof gravity compen-
sators. IEEE Transactions on Robotics, 30:421–431.
Cho, C., Lee, W., Lee, J., and Kang, S. (2012). A 2-dof
gravity compensator with bevel gears. Journal of Me-
chanical Science and Technology, 26:2913–2919.
Chung, D. G., Hwang, M., Won, J., and Kwon, D.-S.
(2016). Gravity compensation mechanism for roll-
pitch rotation of a robotic arm. In 2016 IEEE/RSJ In-
ternational Conference on Intelligent Robots and Sys-
tems (IROS), pages 338–343.
Gopalswamy, A., Gupta, P., and Vidyasagar, M. (1992). A
new parallelogram linkage configuration for gravity
compensation using torsional springs. In Proceedings
1992 IEEE International Conference on Robotics and
Automation, pages 664–665. IEEE Computer Society.
Jhuang, C. S., Kao, Y. Y., and Chen, D. Z. (2018). Design of
one dof closed-loop statically balanced planar linkage
with link-collinear spring arrangement. Mechanism
and Machine Theory, 130:301–312.
Kim, H. S., Min, J. K., and Song, J. B. (2016). Multiple-
degree-of-freedom counterbalance robot arm based on
slider-crank mechanism and bevel gear units. IEEE
Transactions on Robotics, 32:230–235.
Kim, H.-S. and Song, J.-B. (2014). Multi-dof counterbal-
ance mechanism for a service robot arm. IEEE/ASME
Transactions on Mechatronics, 19:1756–1763.
Kim, S. H. and Cho, C. H. (2017). Static balancer of
a 4-dof manipulator with multi-dof gravity compen-
sators. Journal of Mechanical Science and Technol-
ogy, 31:4875–4885.
Klimchik, A. and Pashkevich, A. (2022). Stiffness Model-
ing for Gravity Compensators, pages 27–71. Springer
International Publishing, Cham.
Klimchik, A., Pashkevich, A., Caro, S., and Furet, B.
(2017). Calibration of industrial robots with pneu-
matic gravity compensators. In 2017 IEEE Inter-
national Conference on Advanced Intelligent Mecha-
tronics (AIM), pages 285–290. IEEE.
Klimchik, A., Wu, Y., Dumas, C., Caro, S., Furet, B., and
Pashkevich, A. (2013). Identification of geometrical
and elastostatic parameters of heavy industrial robots.
In 2013 IEEE International Conference on Robotics
and Automation, pages 3707–3714. IEEE.
Koser, K. (2009). A cam mechanism for gravity-balancing.
Mechanics Research Communications, 36:523–530.
Lin, P. Y., Shieh, W. B., and Chen, D. Z. (2010). Design of
a gravity-balanced general spatial serial-type manipu-
lator. Journal of Mechanisms and Robotics, 2.
Lin, P. Y., Shieh, W. B., and Chen, D. Z. (2012). Design
of statically balanced planar articulated manipulators
with spring suspension.
Morita, T., Kuribara, F., Shiozawa, Y., and Sugano, S.
(2003). A novel mechanism design for gravity com-
pensation in three dimensional space. In Proceed-
ings 2003 IEEE/ASME International Conference on
Advanced Intelligent Mechatronics (AIM 2003), vol-
ume 1, pages 163–168. IEEE.
Nakayama, T., Araki, Y., and Fujimoto, H. (2009). A
new gravity compensation mechanism for lower limb
rehabilitation. In 2009 International Conference on
Mechatronics and Automation, pages 943–948. IEEE.
External Force Adaptive Compensator for Serial Manipulators
507