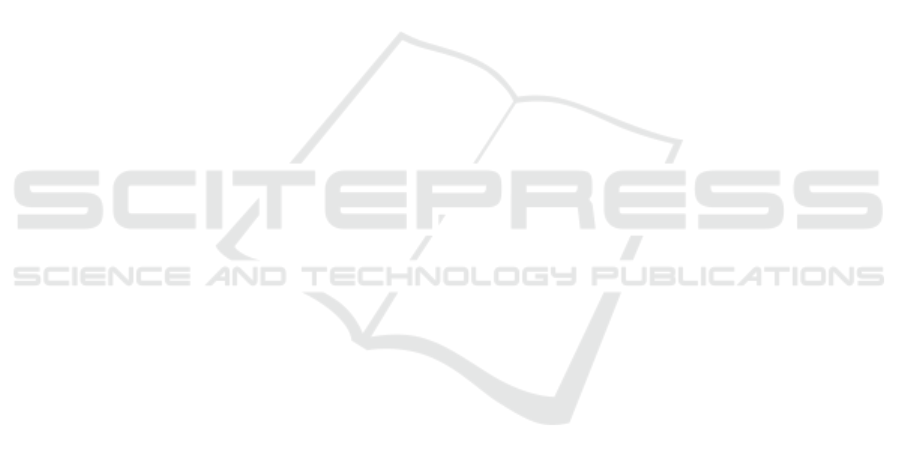
4 CONCLUSION
The design of simple endeffectors paired with suit-
able control strategies allows for the non-prehensile
manipulation of a variety of objects that otherwise
would be hard to grasp. We have shown that sin-
gle contact endeffectors can be used to move flat,
lightweight objects. Heavier objects can be success-
fully pushed with line-contact endeffectors. A torque-
based closed-loop control strategie facilitates stable
contact with the pushed objects along the trajectory
without visual feedback.
REFERENCES
Al-Jarrah, O. M. and Zheng, Y. F. (1998). Intelligent com-
pliant motion control. IEEE Transactions on Sys-
tems, Man, and Cybernetics, Part B (Cybernetics),
28(1):116–122.
Alex Owen-Hill (2021). Robotics research 101: Getting
started with force control. [Online].
Cosgun, A., Hermans, T., Emeli, V., and Stilman, M.
(2011). Push planning for object placement on clut-
tered table surfaces. In IEEE/RSJ Int. Conf. on intelli-
gent robots and systems.
Dogar, M. and Srinivasa, S. (2010). Push-grasping with
dexterous hands: Mechanics and a method. In
IEEE/RSJ Int. Conf. on Intelligent Robots and Sys-
tems.
Dogar, M. and Srinivasa, S. (2011). A framework for push-
grasping in clutter. Robotics: Science and systems.
Eppner, C. and Brock, O. (2015). Planning grasp strategies
that exploit environmental constraints. In IEEE Int.
Conf. on Robotics and Automation (ICRA).
Krivic, S. and Piater, J. (2018). Online adaptation of robot
pushing control to object properties. In IEEE/RSJ Int.
Conf. on Intelligent Robots and Systems (IROS).
Krivic, S., Ugur, E., and Piater, J. (2016). A robust push-
ing skill for object delivery between obstacles. In
IEEE Int. Conf. on Automation Science and Engineer-
ing (CASE).
Li, Q. and Payandeh, S. (2007). Manipulation of convex
objects via two-agent point-contact push. The inter-
national journal of robotics research, 26(4):377–403.
Lynch, K. M. (1996). Nonprehensile robotic manipulation:
Controllability and planning. Carnegie Mellon Uni-
versity.
Lynch, K. M. and Murphey, T. D. (2003). Control of
nonprehensile manipulation. In Control Problems in
Robotics, pages 39–57. Springer.
Lynch, K. M. and Park, F. C. (2017). Modern Robotics.
Cambridge University Press.
Omr
ˇ
cen, D., B
¨
oge, C., Asfour, T., Ude, A., and Dillmann,
R. (2009). Autonomous acquisition of pushing actions
to support object grasping with a humanoid robot. In
IEEE-RAS Int. Conf. on Humanoid Robots.
Ott, C., Mukherjee, R., and Nakamura, Y. (2010). Unified
impedance and admittance control. In IEEE Int. Conf.
on robotics and automation.
Ruggiero, F., Lippiello, V., and Siciliano, B. (2018). Non-
prehensile dynamic manipulation: A survey. IEEE
Robotics and Automation Letters, 3(3):1711–1718.
Ryu, J.-C., Ruggiero, F., and Lynch, K. M. (2013). Con-
trol of nonprehensile rolling manipulation: Balanc-
ing a disk on a disk. IEEE Transactions on Robotics,
29(5):1152–1161.
Sarantopoulos, I. and Doulgeri, Z. (2018). Human-inspired
robotic grasping of flat objects. Robotics and au-
tonomous systems, 108:179–191.
Schindlbeck, C. and Haddadin, S. (2015). Unified passivity-
based cartesian force/impedance control for rigid and
flexible joint robots via task-energy tanks. In IEEE
Int. Conf. on robotics and automation (ICRA).
Serra, D. (2016). Robot control for nonprehensile dynamic
manipulation tasks. In Int. Conf. on Informatics in
Control, Automation and Robotics.
Siciliano, B., Villani, L., and Federico, N. (2000). From in-
direct to direct force control: A roadmap for enhanced
industrial robots. Rob
´
otica.
Song, C. and Boularias, A. (2020). Learning to slide un-
known objects with differentiable physics simulations.
arXiv preprint arXiv:2005.05456.
St
¨
uber, J., Kopicki, M., and Zito, C. (2018). Feature-based
transfer learning for robotic push manipulation. In
IEEE Int. Conf. on Robotics and Automation (ICRA).
St
¨
uber, J., Zito, C., and Stolkin, R. (2022). Let’s push things
forward: A survey on robot pushing. Frontiers in
Robotics and AI, 7.
Vukcevic, D. (2020). Lazy robot control by relaxation of
motion and force constraints. Technical report, Fach-
bereich Informatik.
Yu, K.-T., Bauza, M., Fazeli, N., and Rodriguez, A. (2016).
More than a million ways to be pushed. a high-fidelity
experimental dataset of planar pushing. In IEEE/RSJ
Int. Conf. on intelligent robots and systems (IROS).
Zeng, A., Song, S., Welker, S., Lee, J., Rodriguez, A., and
Funkhouser, T. (2018). Learning synergies between
pushing and grasping with self-supervised deep rein-
forcement learning. In IEEE/RSJ Int. Conf. on Intelli-
gent Robots and Systems (IROS).
Zhou, J., Paolini, R., Bagnell, J. A., and Mason, M. T.
(2016). A convex polynomial force-motion model for
planar sliding: Identification and application. In IEEE
Int. Conf. on Robotics and Automation (ICRA).
Zito, C., Stolkin, R., Kopicki, M., and Wyatt, J. L. (2012).
Two-level RRT planning for robotic push manipula-
tion. In IEEE/RSJ Int. Conf. on intelligent robots and
systems (IROS).
ICINCO 2022 - 19th International Conference on Informatics in Control, Automation and Robotics
78