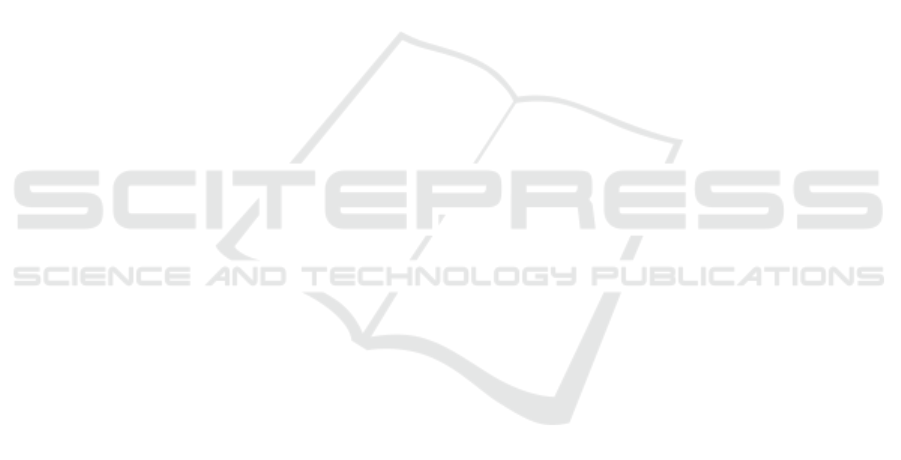
another (unknown). To achieve this task a geometric
approach has been developed, which is supported on
a simplified hydro-dynamic model. To validate our
approach some tests on simulation environments are
presented.
This work is organized as follows. In next sec-
tion some important works related to the spill prob-
lem is described in the next section. Subsequently, in
section 3 it will be described the proposed geomet-
ric approach to solve the spillover problem. Then, in
section 4 presents the results obtained from the sim-
ulation. Finally, at section 5 the conclusions are pre-
sented.
2 RELATED WORKS
The problem of precise liquids’ pouring has become
very important in recent years There are many appli-
cations both industries and diverse sectors as: com-
merce or services.
For example, in metallurgy industry is a very com-
mon and important task, where it is required to main-
tain a constant flow to prevent oxidation, air entrap-
ment and erosion on metals (Noda and Terashima,
2006), (Noda and Terashima, 2007). To deal with
such problem in (Castilla et al., 2017) is presented
an approach to automate liquids pouring from a tilt-
ing ladle. Considering only the tilting ladle in mo-
tion, it is proposed to rotate the ladle at an angular
speed prescribed by a geometric and dynamic calcu-
lation to keep the discharge flow constant. To simplify
the geometry ladle is considered as a cylindric recip-
ient with circular weir. The resulting angular veloc-
ity was used as input for a set of computational fluid
dynamics simulations to later calculate the trajectory
of the spilled liquid. In (Sueki and Noda, 2019) it
is developed an improved model, initially proposed
in (Sueki and Noda, 2018), to pour molten metal in
a container by controlling the tilting ladle. The pro-
cess is achieved using a spill flow feedback control
to improve tracking performance. The discharge flow
rate is computed by using an extended Kalman filter
and controlled using a PID scheme. The proposed ap-
proach has been applied at laboratory with a pouring
robot.
Other approaches use physical models of simpli-
fied dynamics; for example, in (Pan and Manocha,
2016), is presented an approach using intrinsic prop-
erties of liquids to transfer them with a robotic ma-
nipulator from a container to another avoiding with
it, the high-cost solution of Navier-Stokes model. A
motion planning algorithm is then used to compute
a smooth and collision-free trajectory (Park et al.,
2012), (Ratliff et al., 2009), (Pan et al., 2016). The
simplified parameter set, and dynamic model is re-
stricted to the task of slow-rate liquid transfer. When
the end-effector is moves too fast, the motion de-
scribed could be far from planned trajectory. This ap-
proach pours the complete content of one recipient to
another.
To pour partial amounts of liquids, in (Do and
Burgard, 2019) it is proposed to control pouring liq-
uid level directly at destination recipient; for which,
authors propose, on one side to determine stoppage
using depth data from a low cost RGB-D camera and
on the other side, adapting pouring speed based on
liquid’s level at destination. With the use of an in-
frared light, authors overcome the problem of liquid’s
level detection for different transparency and refrac-
tive index of liquids like water, oil, or milk.
Spilled estimation is very important task when
pouring specific quantities. In (Matl et al., 2019) it
is proposed a method to pour liquids through haptic
sensing. In this work, initially a robot moves a con-
tainer through a series of tilting movements and ob-
serves the twists induced in the manipulator’s wrist
while the liquid’s center of mass scrolls. It is showed
that with haptic signals and a physics-based model it
can be obtained a high-precision estimate of liquids’
mass and volume in a cylindrical container. Addition-
ally, it is provided a framework for estimating fluid
viscosity.
The geometric characteristics of the container are
also important, for example in (Kennedy et al., 2017)
is proposed a method to autonomously dispense a pre-
cise amount of liquid using visual feedback. Authors
model diverse geometrical containers, showing that,
in particular for square base prisms the flow can be
controlled by observing the height of the fluid in the
receiving container. This approach to pouring control
is not smooth and calibration of the target container is
required.
Finally, in (Dong et al., 2019) are proposed two
approaches to control the movement of a service robot
as it accurately pours liquid from one unknown con-
tainer to another unknown container without the need
for external tools. The first proposal focuses on mea-
suring the height of poured liquid in the target con-
tainer. In this case, the action is controlled using a PD
controller, which considers the angular velocity of the
pouring vessel as a process variable and the volume
poured as a control variable. The second method fo-
cuses on the pouring container. The volume poured
is calculated using the relationship between the an-
gle of the pour container and discharged volume. The
action is controlled with a simple proportional con-
troller that takes the angular velocity of pouring vessel
A Geometric Approach for Partial Liquids’ Pouring from a Regular Container by a Robotic Manipulator
689