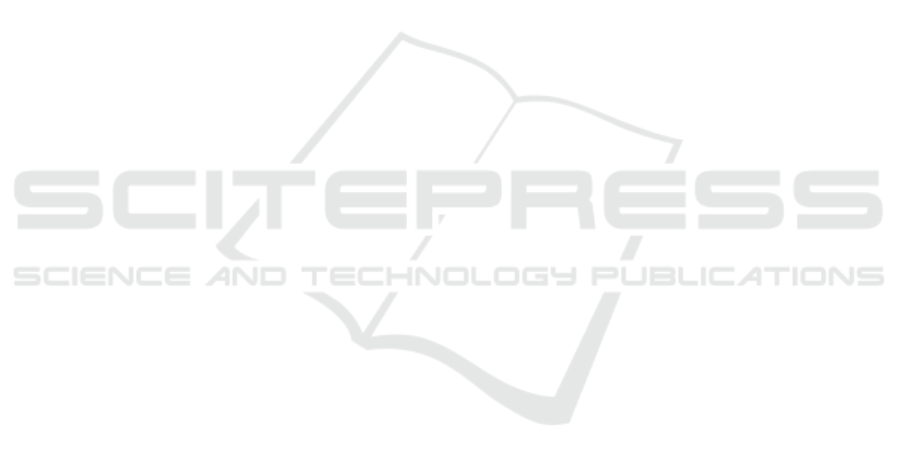
Daney, D. and Emiris, I. (2001). Robust parallel robot cal-
ibration with partial information. volume 4, pages
3262–3267.
Deblaise, D., Hernot, X., and Maurine, P. (2006). A system-
atic analytical method for pkm stiffness matrix calcu-
lation. pages 4213 – 4219.
Driels, M., Swayze, W., and Potter, S. (1993). Full-pose
calibration of a robot manipulator using a coordinate-
measuring machine. The Inter. J. of Advanced Manu-
facturing Technology, 8:34–41.
Dumas, C., Caro, S., Garnier, S., and Furet, B. (2011). Joint
stiffness identification of six-revolute industrial serial
robots. Robot. Comput.-Integr. Manuf., 27:881–888.
Elatta, A., Gen, L., Zhi, F., Daoyuan, Y., and Fei, L. (2004).
An overview of robot calibration. Information Tech-
nology J., 3:74–78.
Gonzalez, M. K., Theissen, N. A., Barrios, A., and
Archenti, A. (2022). Online compliance error com-
pensation system for industrial manipulators in con-
tact applications. Robot. Comput.-Integr. Manuf.,
76:102305.
Hage, H. (2012). Identification and physical simulation of
a st
¨
aubli tx90 robot during high-speed milling.
Jazar, R. (2022). Theory of Applied Robotics: Kinematics,
Dynamics, and Control (3rd Edition). Springer.
Jiang, Z., Huang, M., Tang, X., and Song, B. (2020).
Observability index optimization of robot calibration
based on multiple identification spaces. Autonomous
Robots, 44:1029–1046.
Jin, J. and Gans, N. (2015). Parameter identification for in-
dustrial robots with a fast and robust trajectory design
approach. Robot. Comput.-Integr. Manuf., 31:21–29.
Joubair, A., Slamani, M., and Bonev, I. (2012). Kinematic
calibration of a five-bar planar parallel robot using all
working modes. Robot. Comput.-Integr. Manuf., 29.
Kamali, K. and Bonev, I. (2019). Optimal experiment de-
sign for elasto-geometrical calibration of industrial
robots. IEEE/ASME Trans. on Mech., 24:2733–2744.
Klimchik, A., Ambiehl, A., Garnier, S., Furet, B., and
Pashkevich, A. (2016). Experimental study of robotic-
based machining. IFAC-PapersOnLine, pages 174–
179.
Klimchik, A., Ambiehl, A., Garnier, S., Furet, B., and
Pashkevich, A. (2017). Efficiency evaluation of
robots in machining applications using industrial per-
formance measure. Robot. Comput.-Integr. Manuf.,
48:12–29.
Klimchik, A., Bondarenko, D., Pashkevich, A., Briot, S.,
and Furet, B. (2014). Compliance error compensation
in robotic-based milling. Informatics in Control, Au-
tomation and Robotics, 283.
Klimchik, A., Furet, B., Caro, S., and Pashkevich, A.
(2015). Identification of the manipulator stiffness
model parameters in industrial environment. Mech.
Mach. Theory, 90:1–22.
Klimchik, A. and Pashkevich, A. (2017). Serial vs. quasi-
serial manipulators: Comparison analysis of elasto-
static behaviors. Mech. Mach. Theory, 107:46–70.
Klimchik, A., Pashkevich, A., Caro, S., and Chablat, D.
(2012). Stiffness matrix of manipulators with passive
joints: Computational aspects. Robot. IEEE Trans. on,
28:955–958.
K
¨
ovecses, J. and Angeles, J. (2007). The stiffness matrix in
elastically articulated rigid-body systems. Multibody
System Dynamics, 18:169–184.
Li, Z., Li, S., and Luo, X. (2021). An overview of calibra-
tion technology of industrial robots. IEEE/CAA J. of
Automatica Sinica, 8:23–36.
Ma, L., Bazzoli, P., Sammons, P., Landers, R., and Bristow,
D. (2017). Modeling and calibration of high-order
joint-dependent kinematic errors for industrial robots.
Robot. Comput.-Integr. Manuf., 50.
Mamedov, S., Popov, D., Mikhel, S., and Klimchik, A.
(2018). Compliance error compensation based on re-
duced model for industrial robots. pages 190–201.
Marie, S., Courteille, E., and Maurine, P. (2013). Elasto-
geometrical modeling and calibration of robot manip-
ulators: Application to machining and forming appli-
cations. Mech. Mach. Theory, 69:13–43.
Nguyen, V. L., Kuo, C.-H., and Lin, P. T. (2022). Compli-
ance error compensation of a robot end-effector with
joint stiffness uncertainties for milling: An analytical
model. Mech. Mach. Theory, 170:104717.
Nubiola, A. and Bonev, I. (2013). Absolute calibration of
an abb irb 1600 robot using a laser tracker. Robot.
Comput.-Integr. Manuf., 29:236–245.
Park, I.-W., Lee, B.-J., Cho, S.-H., Hong, Y.-D., and
Kim, J.-H. (2012). Laser-based kinematic calibra-
tion of robot manipulator using differential kinemat-
ics. Mech. IEEE/ASME Trans. on, 17:1059–1067.
Pashkevich, A., Chablat, D., and Wenger, P. (2009). Stiff-
ness analysis of overconstrained parallel manipula-
tors. Mech. Mach. Theory, 44:966–982.
Piras, G., Cleghorn, W., and Mills, J. (2005). Dynamic
finite-element analysis of a planar high-speed, high-
precision parallel manipulator with flexible links.
Mech. Mach. Theory, 40:849–862.
Qin, J., L
´
eonard, F., and Abba, G. (2016). Real-time tra-
jectory compensation in robotic friction stir welding
using state estimators. IEEE Trans. on Control Sys-
tems Technology, 24:2207–2214.
Quennouelle, C. and Gosselin, C. (2008). Stiffness Matrix
of Compliant Parallel Mechanisms, pages 331–341.
Springer.
Renders, J.-M., Rossignol, E., Becquet, M., and Hanus, R.
(1992). Kinematic calibration and geometrical param-
eter identification for robots. Robot. and Automation,
IEEE Trans. on, 7:721 – 732.
Salisbury, J. (1981). Active stiffness control of a manipu-
lator in cartesian coordinates. volume 1, pages 95 –
100.
Veitschegger, W. and Wu, C.-h. (1987). A method for cali-
brating and compensating robot kinematic errors. vol-
ume 4, pages 39 – 44.
Wu, L., Yang, X., and Chen, K. (2015a). A minimal poe-
based model for robotic kinematic calibration with
only position measurements. IEEE Trans. on Automa-
tion Science and Eng., 12:758–763.
Wu, Y., Klimchik, A., Caro, S., Furet, B., and Pashkevich,
A. (2015b). Geometric calibration of industrial robots
using enhanced partial pose measurements and design
of experiments. Robot. Comput.-Integr. Manuf., 35.
Simulation Study on Robot Calibration Approaches
523