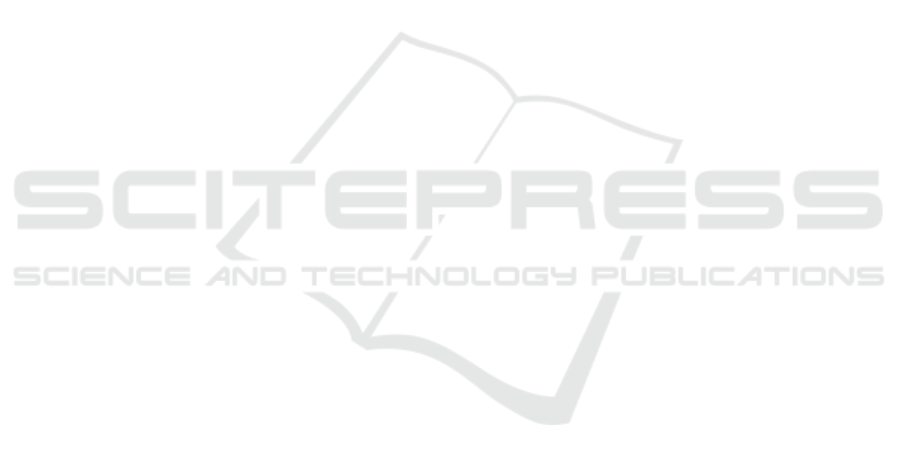
As future work we plan to validate the method on
the real system as well as on more complex systems.
Further study of the influence of the tuning of the ex-
tended Kalman filter will also be carried out to vali-
date the robustness of the proposed method.
REFERENCES
Akdo
˘
gan, E., Aktan, M. E., Koru, A. T., Selc¸uk Arslan, M.,
Atlıhan, M., and Kuran, B. (2018). Hybrid impedance
control of a robot manipulator for wrist and forearm
rehabilitation: Performance analysis and clinical re-
sults. Mechatronics, 49:77–91.
Atkeson, C. G., An, C. H., and Hollerbach, J. M. (1986).
Estimation of inertial parameters of manipulator loads
and links. The International Journal of Robotics Re-
search, 5:101–119.
Bogdan, I. C. (2010). Mod
´
elisation et commande
de syst
`
emes lin
´
eaires de micro-positionnement :
application
`
a la production de micro-composants
´
electroniques. PhD thesis, Universit
´
e Paul Verlaine
- Metz.
Brunot, M., Janot, A., Young, P., and Carrillo, F. (2018).
An improved instrumental variable method for indus-
trial robot model identification. Control Engineering
Practice, 74:107–117.
Dang, Q.-V. (2013). Conception et commande d’une in-
terface haptique
`
a retour d’effort pour la CAO. PhD
thesis, Universit
´
e Polytechnique Hauts-de-France.
Gautier, M. (1997). Dynamic identification of robots with
power model. In Proceedings of International Con-
ference on Robotics and Automation, volume 3, pages
1922–1927.
Gautier, M., Janot, A., and Vandanjon, P.-O. (2013). A new
closed-loop output error method for parameter iden-
tification of robot dynamics. IEEE Transactions on
Control Systems Technology, 21:428–444.
Han, Y., Wu, J., Liu, C., and Xiong, Z. (2020). An iterative
approach for accurate dynamic model identification
of industrial robots. IEEE Transactions on Robotics,
36:1577–1594.
Khalil, W. and Dombre, E. (2002). Chapter 9 - dynamic
modeling of serial robots. In Modeling, Identification
and Control of Robots, pages 191–233. Oxford.
Leboutet, Q., Roux, J., Janot, A., Guadarrama-Olvera, J. R.,
and Cheng, G. (2021). Inertial parameter identifica-
tion in robotics: A survey. Applied Sciences, 11.
Mayeda, H., Yoshida, K., and Osuka, K. (1990). Base
parameters of manipulator dynamic models. IEEE
Transactions on Robotics and Automation, 6:312–
321.
Olsen, M., Swevers, J., and Verdonck, W. (2002). Max-
imum likelihood identification of a dynamic robot
model: Implementation issues. The International
Journal of Robotics Research, 21:89–96.
Pham, M., Gautier, M., and Poignet, P. (2001). Identifica-
tion of joint stiffness with bandpass filtering. In Pro-
ceedings 2001 ICRA. IEEE International Conference
on Robotics and Automation, volume 3, pages 2867–
2872.
Shardt, Y. A., Yang, X., and Ding, S. X. (2016). Quantisa-
tion and data quality: Implications for system identi-
fication. Journal of Process Control, 40:13–23.
Swevers, J., Ganseman, C., Tukel, D., de Schutter, J., and
Van Brussel, H. (1997). Optimal robot excitation and
identification. IEEE Transactions on Robotics and Au-
tomation, 13:730–740.
ICINCO 2022 - 19th International Conference on Informatics in Control, Automation and Robotics
702