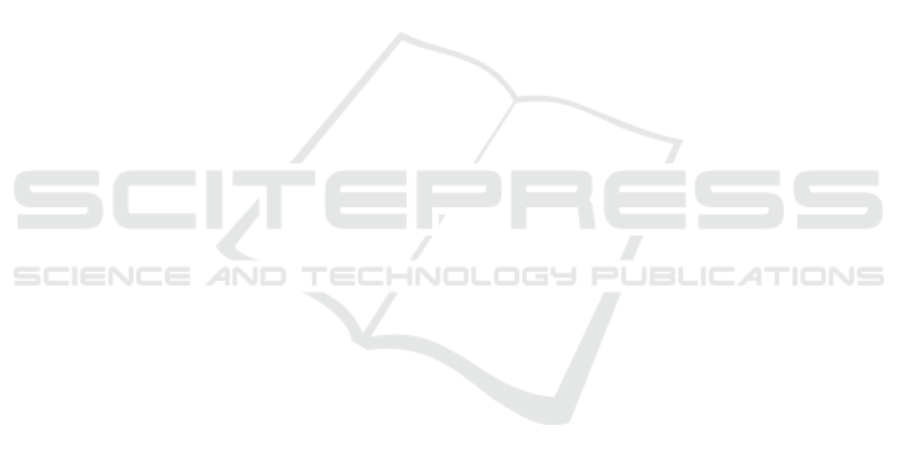
tioning error and torque ripple compensation meth-
ods using advanced controllers (Tarczewski et al.,
2014),(Tarczewski and Grzesiak, 2009).
In order to verify the computational efficiency of
the algorithm’s implementation in the real-time sys-
tem the feedrate generation process was repeated sev-
eral hundred times and the total computation time was
measured each time. The average computation time
of the whole profile was 99.6ms with maximum and
minimum time equal to 104ms and 97.6ms respec-
tively. The total execution time of the toolpath from
Fig.1 with the feedrate profile from Fig.7 was equal to
8.27s. This means that the proposed method has high
computational effectiveness. The computation time
of feedrate generation algorithm is much shorter than
the toolpath execution time. This means that the sys-
tem with the algorithm has on-line real-time capabili-
ties. Even with the inclusion of additional constraints
such as linear joint constraints the system should still
retain its real-time capabilities.
7 CONCLUSIONS
This paper presents a method for jerk limited fee-
drate planning for Non-Uniform Rational B-Spline
(NURBS) toolpaths in a parallel kinematics machine
in linear delta configuration. The algorithm uses jerk-
limited feedrate planning with limitation of of carte-
sian axes velocity, acceleration and jerk. The pre-
sented experimental results show that the algorithm
can effectively constrain cartesian axis constraints.
Further improvements of the algorithm will constrain
velocity, acceleration and jerk in the linear joints. Fur-
thermore the computation times show that the algo-
rithm is computationally effective and is viable for
real-time implementation. Future research will in-
clude improvement of the algorithm and its extension
with additional constraints.
REFERENCES
Bouri, M. and Clavel, R. (2010). The linear delta: De-
velopments and applications. In ISR 2010 (41st In-
ternational Symposium on Robotics) and ROBOTIK
2010 (6th German Conference on Robotics), pages 1–
8. VDE.
Chen, M. and Sun, Y. (2019). Contour error–bounded para-
metric interpolator with minimum feedrate fluctuation
for five-axis cnc machine tools. Int. J. Adv. Manuf.
Technol., 103(1-4):567–584.
Erwinski, K., Paprocki, M., and Karasek, G. (2021). Com-
parison of nurbs trajectory interpolation algorithms
for high-speed motion control systems. In 2021
IEEE 19th International Power Electronics and Mo-
tion Control Conference (PEMC), pages 527–533.
IEEE.
Erwinski, K., Wawrzak, A., and Paprocki, M. (2022). Real-
time jerk limited feedrate profiling and interpolation
for linear motor multi-axis machines using nurbs tool-
paths. IEEE Transactions on Industrial Informatics
(early access, published online 1.02.2022).
Jia, Z.-Y., Song, D.-N., Ma, J.-W., Hu, G.-Q., and Su, W.-
W. (2017). A nurbs interpolator with constant speed
at feedrate-sensitive regions under drive and contour-
error constraints. Int. J. Mach. Tools Manuf., 116:1–
17.
Li, G., Liu, H., Yue, W., and Xiao, J. (2021). Feedrate
scheduling of a five-axis hybrid robot for milling con-
sidering drive constraints. Int. J. Adv. Manuf. Technol.,
112(11):3117–3136.
Lu, T.-C., Chen, S.-L., and Yang, E. C.-Y. (2018). Near
time-optimal s-curve velocity planning for multiple
line segments under axis constraints. IEEE Trans. Ind.
Electron., 65(12):9582–9592.
Mercy, T., Jacquod, N., Herzog, R., and Pipeleers, G.
(2018). Spline-based trajectory generation for cnc ma-
chines. IEEE Trans. Ind. Electron., 66(8):6098–6107.
Ni, H., Yuan, J., Ji, S., Zhang, C., and Hu, T. (2018a).
Feedrate scheduling of nurbs interpolation based on
a novel jerk-continuous acc/dec algorithm. IEEE Ac-
cess, 6:66403–66417.
Ni, H., Zhang, C., Ji, S., Hu, T., Chen, Q., Liu, Y., and
Wang, G. (2018b). A bidirectional adaptive feedrate
scheduling method of nurbs interpolation based on s-
shaped acc/dec algorithm. IEEE Access, 6:63794–
63812.
Piegl, L. and Tiller, W. (1996). The NURBS book. Springer
Science & Business Media.
Su, T., Cheng, L., Wang, Y., Liang, X., Zheng, J., and
Zhang, H. (2018). Time-optimal trajectory plan-
ning for delta robot based on quintic pythagorean-
hodograph curves. IEEE Access, 6:28530–28539.
Sun, Y., Chen, M., Jia, J., Lee, Y.-S., and Guo, D.
(2019). Jerk-limited feedrate scheduling and opti-
mization for five-axis machining using new piecewise
linear programming approach. Sci. China Technol.
Sci., 62(7):1067–1081.
Tarczewski, T., Grzesiak, L., et al. (2014). Torque ripple
minimization for pmsm using voltage matching cir-
cuit and neural network based adaptive state feedback
control. In 2014 16th European Conference on Power
Electronics and Applications, pages 1–10. IEEE.
Tarczewski, T. and Grzesiak, L. M. (2009). High precision
permanent magnet synchronous servo-drive with lqr
position controller. Electrical Review, 85(8):42–47.
Zhang, Y., Ye, P., Zhao, M., and Zhang, H. (2019). Dy-
namic feedrate optimization for parametric toolpath
with data-based tracking error prediction. Mech. Syst.
Signal Process., 120:221–233.
Zhao, H., Zhu, L., and Ding, H. (2013). A real-time
look-ahead interpolation methodology with curvature-
continuous b-spline transition scheme for cnc machin-
ing of short line segments. Int. J. Mach. Tools Manuf.,
65:88–98.
Feedrate Planning for a Delta Parallel Kinematics Numerically Controlled Machine using NURBS Toolpaths
749