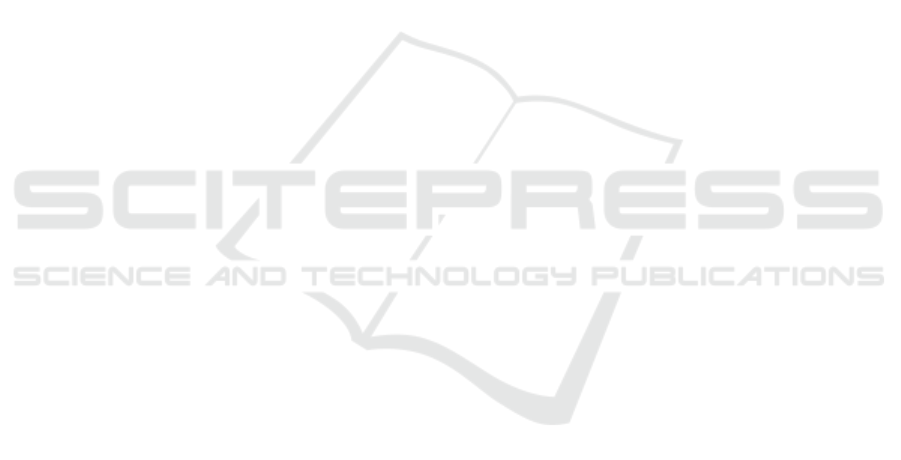
by model equations reconstructed from data process-
ing. Technical Physics Letters, 42(9):886–890.
Foundation, O. S. R. (2021). Gazebo official site.
http://gazebosim.org/.
Jacoff, A., Downs, A., Virts, A., and Messina, E. (2008).
Stepfield pallets: Repeatable terrain for evaluating
robot mobility. In Proceedings of the 8th Workshop
on Performance Metrics for Intelligent Systems, pages
29–34.
Kenwright, B. and Morgan, G. (2012). Practical introduc-
tion to rigid body linear complementary problem (lcp)
constraint solvers. In Algorithmic and Architectural
Gaming Design: Implementation and Development,
pages 159–201. IGI Global.
Malov, D., Edemskii, A., and Saveliev, A. (2019). Proactive
localization system as a part of a cyberphysical smart
environment. In 2019 International Conference on In-
dustrial Engineering, Applications and Manufactur-
ing (ICIEAM), pages 1–5. IEEE.
Morita, S., Hiramatsu, T., Niccolini, M., Argiolas, A., and
Ragaglia, M. (2018). Kinematic track modelling for
fast multiple body dynamics simulation of tracked
vehicle robot. In 2018 23rd International Confer-
ence on Methods & Models in Automation & Robotics
(MMAR), pages 910–915. IEEE.
Moskvin, I. and Lavrenov, R. (2020). Modeling tracks and
controller for servosila engineer robot. In Proceed-
ings of 14th International Conference on Electrome-
chanics and Robotics “Zavalishin’s Readings”, pages
411–422. Springer.
Pecka, M., Zimmermann, K., and Svoboda, T. (2017). Fast
simulation of vehicles with non-deformable tracks. In
2017 IEEE/RSJ International Conference on Intelli-
gent Robots and Systems (IROS), pages 6414–6419.
IEEE.
Pepper, C., Balakirsky, S., and Scrapper, C. (2007). Robot
simulation physics validation. In Proceedings of the
2007 Workshop on Performance Metrics for Intelli-
gent Systems, pages 97–104.
Prabhakar, M., Paulraj, V., Dhanraj, J. A., Nagarajan, S.,
Kannappan, D. A. K., and Hariharan, A. (2020). De-
sign and simulation of an automated guided vehicle
through webots for isolated covid-19 patients in hos-
pitals. In 2020 IEEE 4th Conference on Information &
Communication Technology (CICT), pages 1–5. IEEE.
Quigley, M., Conley, K., Gerkey, B., Faust, J., Foote, T.,
Leibs, J., Wheeler, R., Ng, A. Y., et al. (2009). Ros: an
open-source robot operating system. In ICRA work-
shop on open source software, volume 3, page 5.
Kobe, Japan.
Safin, R., Lavrenov, R., and Mart
´
ınez-Garc
´
ıa, E. A. (2021).
Evaluation of visual slam methods in usar applica-
tions using ros/gazebo simulation. In Proceedings of
15th International Conference on Electromechanics
and Robotics” Zavalishin’s Readings”, pages 371–
382. Springer.
Shabalina, K., Sagitov, A., and Magid, E. (2018). Compar-
ative analysis of mobile robot wheels design. In 2018
11th International Conference on Developments in
esystems Engineering (dese), pages 175–179. IEEE.
Shabalina, K., Sagitov, A., Su, K.-L., Hsia, K.-H., and
Magid, E. (2019). Avrora unior car-like robot in
gazebo environment. In International Conference on
Artificial Life and Robotics, pages 116–119.
Sheh, R., Jacoff, A., Virts, A.-M., Kimura, T., Pellenz,
J., Schwertfeger, S., and Suthakorn, J. (2014). Ad-
vancing the state of urban search and rescue robotics
through the robocuprescue robot league competi-
tion. In Field and service robotics, pages 127–142.
Springer.
Simakov, N., Lavrenov, R., Zakiev, A., Safin, R., and
Mart
´
ınez-Garc
´
ıa, E. A. (2019). Modeling usar maps
for the collection of information on the state of the en-
vironment. In 2019 12th International Conference on
Developments in eSystems Engineering (DeSE), pages
918–923. IEEE.
Sokolov, M., Afanasyev, I., Lavrenov, R., Sagitov, A.,
Sabirova, L., and Magid, E. (2017). Modelling
a crawler-type ugv for urban search and rescue in
gazebo environment. In Artificial Life and Robotics
(ICAROB 2017), International Conference on, pages
360–362.
Sokolov, M., Lavrenov, R., Gabdullin, A., Afanasyev, I.,
and Magid, E. (2016). 3d modelling and simulation of
a crawler robot in ros/gazebo. In Proceedings of the
4th International Conference on Control, Mechatron-
ics and Automation, pages 61–65.
Timperley, C. S., Afzal, A., Katz, D. S., Hernandez, J. M.,
and Le Goues, C. (2018). Crashing simulated planes is
cheap: Can simulation detect robotics bugs early? In
2018 IEEE 11th International Conference on Software
Testing, Verification and Validation (ICST), pages
331–342. IEEE.
Yakovlev, K., Baskin, E., and Hramoin, I. (2015). Grid-
based angle-constrained path planning. In Joint Ger-
man/Austrian Conference on Artificial Intelligence
(K
¨
unstliche Intelligenz), pages 208–221. Springer.
Yumbla, F., Yumbla, E. Q., and Moon, H. (2020). The bi-
oloid gp robot with different configurations for simu-
lation in v-rep controlled by the robot operating sys-
tem (ros). In 2020 6th International Conference on
Control, Automation and Robotics (ICCAR), pages
54–58. IEEE.
ICINCO 2022 - 19th International Conference on Informatics in Control, Automation and Robotics
572