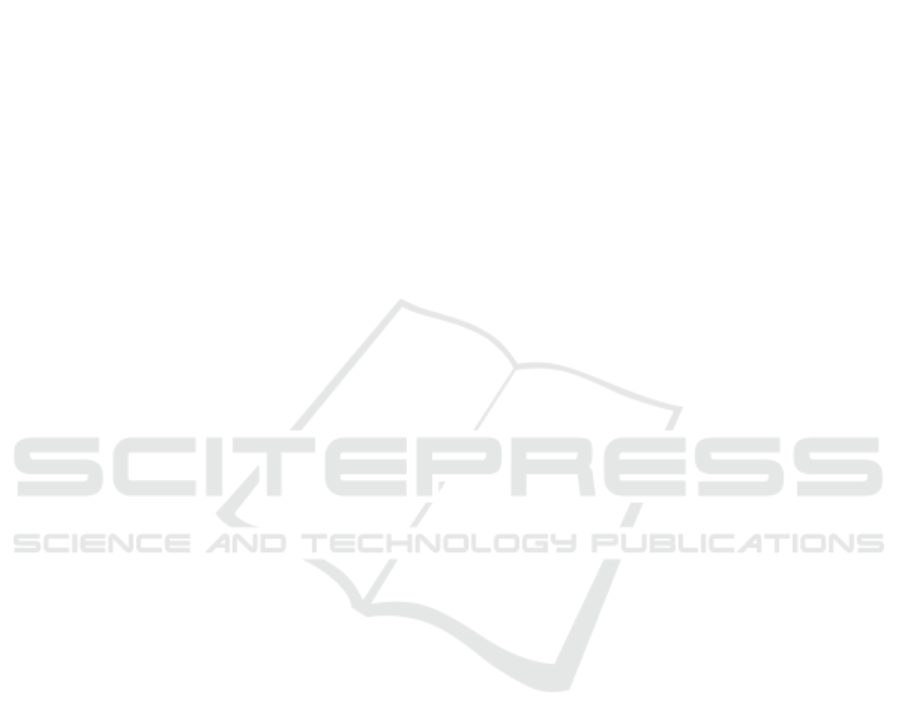
Robust Gain-scheduling LPV Control for a Reconfigurable Robot
R. Al Saidi
1
and S. Alirezaee
2
1
University of Windsor, Windsor, Canada
2
Electrical and Computer Engineering Department, Windsor, Canada
Keywords:
Reconfigurable Robot, Variable D-H Parameters, Gain-scheduling Control, LPV Control.
Abstract:
This paper develops a robust gain–scheduling linear parameter varying (LPV) control for a reconfigurable
robot that combines as many properties of different open kinematic structures as possible and can be used for
a variety of applications. The kinematic design parameters, i.e., the Denavit–Hartenberg (D–H) parameters,
can be modified to satisfy any configuration required to meet a specific task. By varying the joint twist angle
parameter (a configuration parameter), the presented model is reconfigurable to any desired open kinematic
structure, such as ABB, FANUC and SCARA robotic systems. A robust LPV control is developed for on–line
measured parameters of a perturbed LPV model of a Bosch Scara robot arm. This control achieves superior
tracking performance in the presence of dynamic and parameter uncertainties.
1 INTRODUCTION
Robotics technology has been recently exploited in
a variety of areas and various robots have been de-
veloped to accomplish sophisticated tasks in differ-
ent fields and applications such as in space explo-
ration, future manufacturing systems, medical tech-
nology, etc. In space, robots are expected to complete
different tasks, such as capturing a target, construct-
ing a large structure and autonomously maintaining
in-orbit systems. The rapid changes and adjustments
of the Reconfigurable Manufacturing Systems (RMS)
structure must happen in a relatively short time rang-
ing between minutes and hours and not days or weeks.
These systems’ reconfigurability calls for their com-
ponents, such as machines and robots to be rapidly
and efficiently modifiable to varying demands. In
these missions, one fundamental task with the robot
would be the tracking of changing workspace, paths,
the grasping and the positioning of a target in Carte-
sian space. It is desirable and cost effective to em-
ploy a single versatile robot capable of performing
tasks such as inspection, contact operations, assem-
bly (insertion or removal parts), and carrying ob-
jects (pick and place). To satisfy such varying envi-
ronments, a robot with changeable (kinematic struc-
ture) configuration is necessary to cope with these
requirements and tasks. In the literature, LPV con-
trol is used for predefined (fixed) kinematic struc-
ture robots achieving specific tracking performance
requirements. Methodologies for designing LPV con-
trol are given in (Packard, 1994), (Apkarian and
Adams, 1997), (P. Gahinet, 1994) and (Kemin Zhou,
1996), where the gain scheduled controller was guar-
anteed for H
∞
performance of a class of LPV non-
linear systems. In (Zhongwei Yu, 2003) and (Seyed
Mahdi Hashemi, 2009) a polytopic gain scheduled H
∞
control is developed for a two Degrees Of Freedom
(DOF) robot considering nominal parameters without
uncertainties. In (Y.Sun and Liang, 2018), an LPV
controller is developed for a large number of affine
scheduling dynamic parameters of a 2 DOF robot ma-
nipulator without considering uncertainties in their
robotic model.
2 KINEMATICS DEVELOPMENT
OF A RECONFIGURABLE
ROBOT
Development of the general n–DOF Global Kine-
matic Model (n–GKM) is necessary for supporting
any open kinematic robotic arm. The n–GKM model
is generated by the variable D–H parameters as pro-
posed in (A. Djuric, 2010). The D–H parameters pre-
sented in Table 1 are modeled as variable parameters
to accommodate all possible open kinematic struc-
tures of a robotic arm. The twist angle variable α
i
is limited to five different values, (0
0
,±90
0
,±180
0
),
Al Saidi, R. and Alirezaee, S.
Robust Gain-scheduling LPV Control for a Reconfigurable Robot.
DOI: 10.5220/0011356000003271
In Proceedings of the 19th International Conference on Informatics in Control, Automation and Robotics (ICINCO 2022), pages 89-96
ISBN: 978-989-758-585-2; ISSN: 2184-2809
Copyright
c
2022 by SCITEPRESS – Science and Technology Publications, Lda. All rights reserved
89