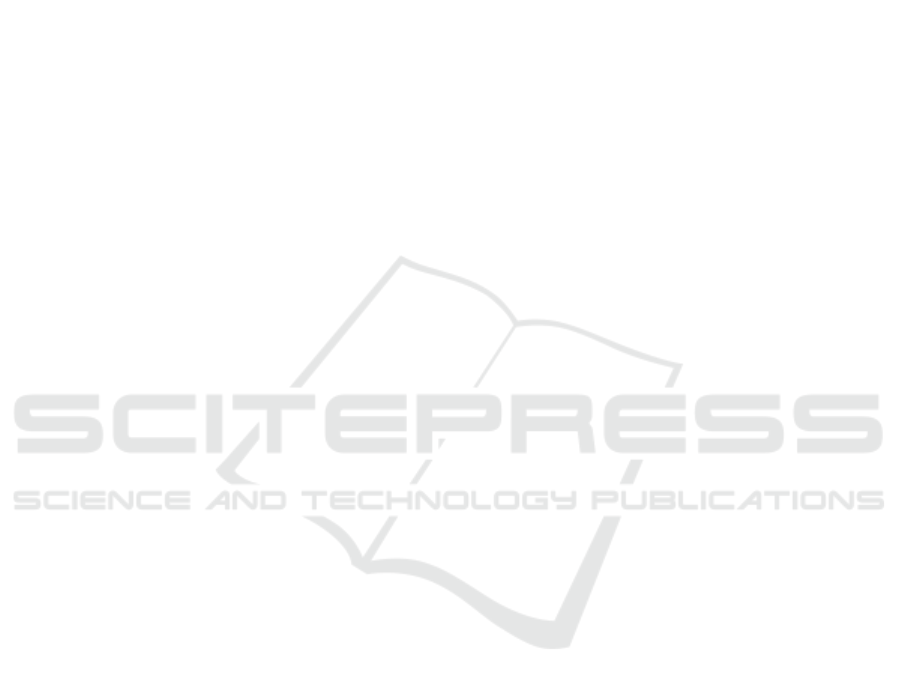
The Visual Inspection of Solder Balls in Semiconductor Encapsulation
Conceic¸
˜
ao N. Silva
1
, Neandra P. Ferreira
2
, Sharlene S. Meireles
2
, Mario Otani
2
,
Vandermi J. da Silva
1
, Carlos A. O. de Freitas
1
and Felipe G. Oliveira
1
1
Institute of Exact Sciences and Technology (ICET), Federal University of Amazonas (UFAM),
Itacoatiara, Amazonas, Brazil
2
Cal-Comp, Institute of Research and Technological Innovation (ICCT), Manaus, Amazonas, Brazil
neandra pf@calcomp-icct.org.br, sharlene@calcomp-icct.org.br, mario otani@calcomp-icct.org.br
Keywords:
Ball Bond Inspection, Automatic Visual Inspection, Deep Learning.
Abstract:
The growing demand for increasing memory storage capacity has required a high density of integration within
the semiconductor encapsulation and, consequently, has made this process more complex and susceptible
to failures during the production stage. In the semiconductor encapsulation area, the costs of materials and
equipment are high and the profit margin is narrow, making it necessary to rigorously inspect the process steps
to keep the productive activity viable. This work addresses the problem of quality control in silicon wafers
soldering procedure, allowing error detection before the epoxy resin molding process, generating useful infor-
mation for correcting equipment configurations and predicting failures from the raw materials and inputs used
in the process. We propose an approach to classify solder balls, in the soldering process of silicon wafers on
Ball Grid Array (BGA), contained in the Printed Circuit Board (PCB) substrates. The proposed methodology
is composed of two main steps: i) Solder ball segmentation; and ii) Solder ball classification through deep
learning. The proposed predictive model learns the relation between visual features and the different soldering
conditions. Real and simulated experiments were carried out to validate the proposed approach. Results show
the obtained accuracy of 99.4%, using Convolutional Neural Network (CNN) classification model. Further-
more, the proposed approach presents high accuracy even regarding noisy images, resulting in accuracy of
92.8% and 75.7% for a Salt and Pepper and Gaussian noise, respectively, in the worst scenario. Experiments
demonstrate reliability and robustness, optimizing the manufacturing.
1 INTRODUCTION
Automated inspection of semiconductors has been the
focus of numerous research efforts in Microelectron-
ics and Industrial communities in the past few years
(Zhang et al., 2022). The semiconductors inspection
has the role of feeding back the methods with infor-
mation on specific errors, which can be correlated
with production problems. The semiconductors anal-
ysis includes the assessment on occurrence of failures
due to the materials involved in the process or inad-
equate definitions of the machine parameters (Zhang
et al., 2021).
In the semiconductors context, the production of
memory devices represents a great manufacturing
challenge, especially due to the small component’s di-
mensions and the required precision in its operation.
Additionally, the market demand for memory devices
has increased massively, requiring the expansion of
memory production volume, making the manual in-
spection process critical (Chang et al., 2018).
The use of the conventional visual inspection pro-
cess, regarding a trained human operator, presents ef-
fectiveness between 80% and 90% of cases. However,
after the first half working hour, the human operator
visual acuity decreases significantly, for the analysis
of a single type of defect [1]. In Figure 1, is pre-
sented an example of a human visual inspection of
silicon wafers, where the human operator should visu-
ally run through all the components on the PCB sub-
strate looking for different types of defects.
In this paper, we present an approach to clas-
sify solder balls, in the soldering process of a sili-
con wafer, called die, on BGAs, contained in the PCB
substrates. The solder ball is classified into three cat-
egories: i) correct; ii) absence; or iii) failure. We also
introduce a CNN architecture for supervised classifi-
cation of solder balls, which learns the main features
that represent all approached types of soldering condi-
tions. Experiments in real-world scenarios and simu-
750
Silva, C., Ferreira, N., Meireles, S., Otani, M., J. da Silva, V., O. de Freitas, C. and Oliveira, F.
The Visual Inspection of Solder Balls in Semiconductor Encapsulation.
DOI: 10.5220/0011357400003271
In Proceedings of the 19th International Conference on Informatics in Control, Automation and Robotics (ICINCO 2022), pages 750-757
ISBN: 978-989-758-585-2; ISSN: 2184-2809
Copyright
c
2022 by SCITEPRESS – Science and Technology Publications, Lda. All rights reserved