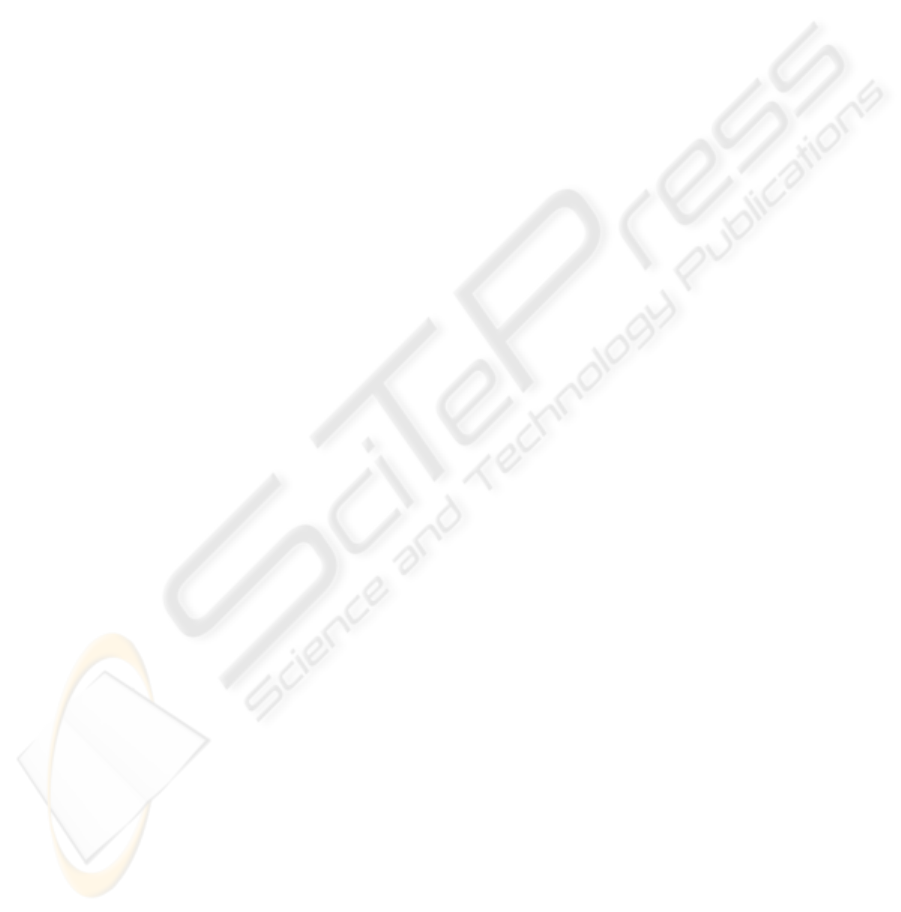
5 FUTURE TRENDS
If RFID technology is to succeed in today’s competition, it
must be economically viable. Although RFID already
found its place in supply chain and warehouse
operations it is arguable if its short-term return of
investment justifies initial cost of implementation.
A major problem of today’s RFID is a lack of
unified electronic product code, making RFID tags
an “internal inventory” of individual companies or
supply chains. Although EPC global standards were
adopted, for really wide spread use of RFID it will
be necessary to introduce certain standardized
format of codes as it was in case with bar codes. To
make tags economically sensible for item-level
tagging of low cost products it is essential to cut
their costs from current ¢ 50 - $2 to maximum ¢ 5
(Sarma, 2003).Mentioned future development of
RFID technology will allow better management of
in-house and supply chain processes with greater
accuracy and provide unprecedented visibility to the
material flows.
ACKNOWLEDGEMENTS
This work was supported by European Commission
programme INTERREG IIIC, ECO4LOG
international project.
REFERENCES
Auto-ID center, 2002. Technology guide, Massachusetts
Institute of Technology, Cambridge
ALTA A/S,2003. White paper, Strategies for in sequence
supply, Copenhagen
Bernroider, E., Koch,S., 2000. Differences in
Characteristics of the ERP System Selection Process
between Small or Medium and Large Organizations,
In AMCIS 2000, Sixth Americas Conference on
Information Systems, pp. 1022-1028, Long Beach, CA
Chappell, G., Ginsburg, L., Schmidt, P.,Smith, J.,
Tobolski, J, 2003. Auto-ID on the Line: The Value of
Auto-ID Technology in Manufacturing, Auto-ID
Center, Massachusetts Institute of Technology,
Cambridge
Choi, B., Kim, B., 2002. MES architecture for FMS
compatible to ERP. In International Journal of
Computer integrated manufactuirng, Vol.15, No.3
Czarnecki, H., Loyd, N., 2000. Simulation of Lean
Assembly Line for High Volume Manufacturing.
Center for Automation and Robotics, University of
Alabama
Donovan, R.M.,2005. SCM: Cracking the „Bullhip
Effect“, R.Michael Donovan & Co., Framingham
DoD suppliers passive RFID information guide,2005,
Version 6.0, January 17
Kisiel, T., 2001. Manufacturing Execution Systems: Steps
to a Successful Implementation. DAI White Paper,
Digital Applications International, London, United
Kingdom
Kumar, V., 1996. Introduction to automation, University
of Pennsylvania
Lawless, G., 2000. Information Technology (IT) For
Manufacturing: Where Has It Been, Where Is It
Heading?.In: Journal of Industrial Technology,Vol.16,
Numb.4
Modrak, V, 2005. Functionalities and Position of
Manufacturing Execution Systems. In Encyclopedia of
Information Science and Technology, Volume 1-5.
Idea Group Reference, Hershey, PA, USA
MESA #2,1997. MES functionalities and MRP to MES
Data Flow Possibilities White Paper 2, Manufacturing
Execution Systems Association, Pitsburgh, P.A.
Ohno, T., 1988. Toyota Production System, Productivity
Press
Ohuchi A., Okuda Y., Nakamura Y., Hitomi M. , H.
Tomita, 2001. A Study of Simulation Model of
Human-Oriented Production Process in Consideration
of Human Factors. In Publication of Industry
Applications Society, Vol. 121D, Numb. 6,
Rockwell automation white paper, 2004. A practical guide
on extracting measurable value from RFID
implementations in plant and warehousing
operations”, October issue
Sarma, S., 2003. Towards 5 cent tag. Auto-ID Center
Massachusetts Institute of Technology, Cambridge
Silva,L., Ramos, A.,Vilarinho,P., 2000. Using simulation
for manufacturing process reengineering. A practical
case study. In
Proceedings of the 2000 Winter
Simulation Conference
Stageman,L., 2004. Consumer Awareness and Concern
About RFID on the Rise. In Market Wire, December
issue
Strassner,M.,Fleisch,E., 2003. The Promise of Auto-ID in
the Automotive Industry. Auto-ID Center,
Massachusetts Institute of Technology, Cambridge
Taylor,D. ,Brunt,D., 2000. Manufacturing Operations and
Supply Chain Management The LEAN Approach”
Viswanadham,N., 2002. Past, present and future of Supply
chain automation. In IEEE Robotics and automation
magazine
Vokorokos, L., Adám, N., Petrík , S., 2004. Operating
Matching In dynamic Data flow Architectures. In
Proceedings of IEEE International conference on
Computational Cybernetics. Vienna, Austria
Weigert,G., Werner,S., Hampel,D., 2000. ROSI – Ein
Programmsystem zur Simulation und Optimierung von
Fertigungsprozessen. 9. ASIM-Fachtagung Simulation
in Produktion und Logistik“, Berlin
ELIMINATION OF TIME DEPENDENCE OF INFORMATION VALIDITY BY APPLICATION OF RFID
TECHNOLOGY
135