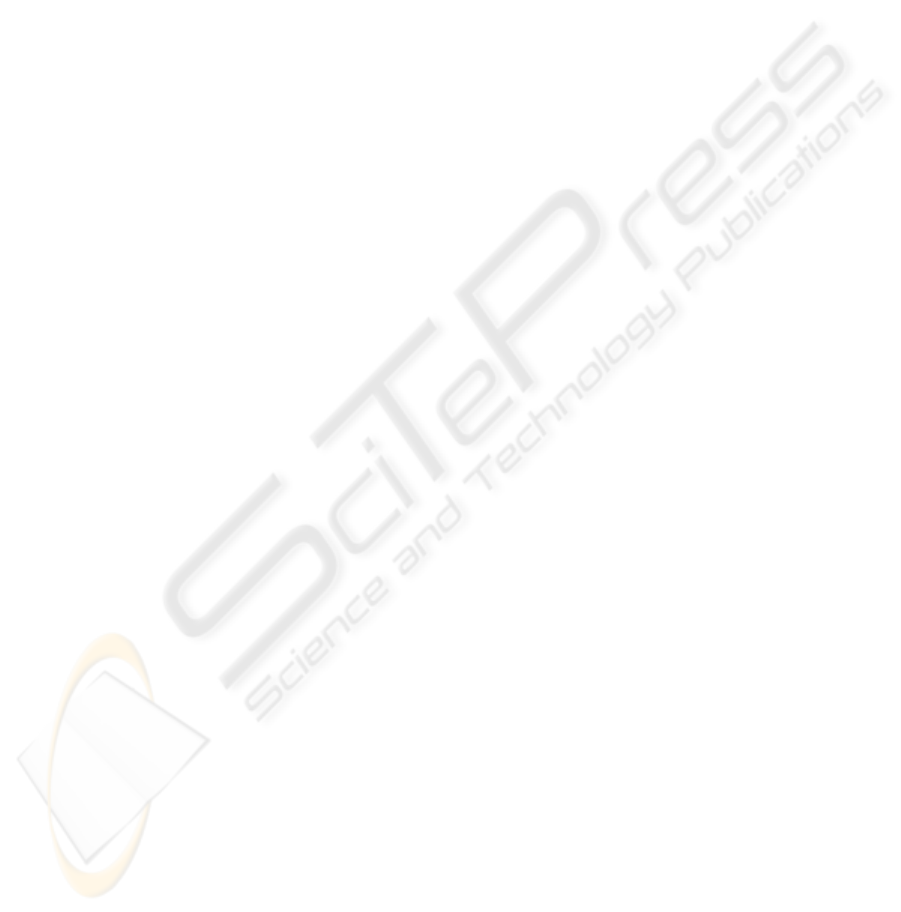
6 DISCUSSION
Technological solutions have been developed to
overcome aforesaid challenges, but, as illustrated, so
far the value of these solutions has been close to
zero. They have been developed separately for small,
specific needs, which have resulted fragmented ap-
plication architecture that fails to support the work
processes adequately. Also, because of the life-cycle
of the paper machine, the systems at the paper mill
are developed purely for their own needs. They are
not even designed to have external connections and
to support service business as information producer.
Yet they are perceived as one by the service provider.
Integrating these solutions for a service-oriented
application architecture has been a topic of discus-
sion in the companies. Yet the task is highly compli-
cated. A generic platform and loosely-tied integra-
tion of applications is needed, but it is not enough.
As only a part of the information can be collected
from the remote systems, its correct interpretation
sets a need for contextual information. This, as
turned out in our case, becomes challenging as ap-
propriate experts are traveling between their own
organization’s sites or between them and customer
site. The question is not only having access to data
but also having access to experts.
Technological challenges for industrial service
business can be summarized as follows:
• Systems are not developed in accordance to
networked environment, and they are lacking a
dynamic and loose coupled network.
• System architecture is fragmented consisting of
separate solutions for specific purposes. Design-
ing new system architecture is needed but may
turn out to be impossible.
• Platform technology to enable service innova-
tions, development and remote service applica-
tion concepts does not exist.
• Lack of interoperability between applications
and systems in the network causes that the inte-
gration between business applications and con-
nections to external systems is difficult.
• Lack of technical interoperability between or-
ganizations does not support delivery and visi-
bility of service products.
• Applications do not form a solid entity or sup-
port workflows.
• Operational interfaces do not support fluent co-
operation or communication limiting interaction
between service provider and customer.
• Knowledge created in the service process can-
not be shared and utilized.
These are even more challenging when the transition
from product-based industry to service-oriented
business mode is considered; while we are still
struggling with technological issues, that, by solving
them, would enable industrial service business, we
are also trying to change business environment and
organizational practices. So, although all this needs
to be done concurrently, we are still in a situation
where the base, i.e. ICT infrastructure in its entirety,
is not rigid and well established. Although Biehl et
al. (2004) argued for the existence of the ICT infra-
structure, our case argues against that. In fact, we
have bits and pieces of the infrastructure, but it is not
complete or coherent. There are still several issues
that need to be considered before the organizations
can operate in a service-oriented business mode ei-
ther as service producers or service consumers.
REFERENCES
Biehl, M., E. Prater, J.R. McIntyre (2004). Remote repair,
diagnostics, and maintenance. CACM 47(11), 100-106.
Brooks T., Chen S., Lee K. (2003). IEEE 1451 smart wire-
less machinery monitoring and control for naval ves-
sels. 13th International Ship Control Systems Sympo-
sium, April 7-9, Orlando, FL, USA.
Grönroos, C. (2001). Palveluiden johtaminen ja
markkinointi [Service management and marketing: in
Finnish]. Helsinki, WSOY
Heikkilä, J., M. Heikkilä, J. Lehmonen, & S. Pekkola
(2005) Smart ICT support for business networks. In:
Vervest et al. (2005) pp. 389-403
Laudon, K. & Laudon, J. (2004) Management Information
Systems: Managing the digital firm. Prentice Hall.
Mumford, E. (1993) Designing Human Systems: For New
Technology. Manchester Business School.
Rödder, H., Kieckhöfel, O. & Manzke, S. (1998). Internet-
based maintenance support for customers and manu-
facturers. Industrial Electronics Society. IECON '98.
pp. 2084 – 2088.
Shaw, D., R. Snowdon, C. Holland, P. Kawalek, B. War-
boys, (2005)., The Viable Systems Model Applied To
A Smart Network: The Case Of The UK Electricity
Market, In: Vervest et al. (2005). pp. 289-305.
Sihn, W. & Graupner, T.-D. (2003). e-Industrial services
for manufacturing systems: differentiation through
internet services. The 36th CIRP-International Semi-
nar on Manufacturing Systems, 3.-5. June 2003, Saar-
bruecken, Germany.
Thompson A. (2004). Wireless and Internet communica-
tions technologies for monitoring and control. Control
Engineering Practice. 12(June). 781-791.
Van Liere, D. W., L. Hagdorn, M.R. Hoogeweegen,
P.H.M. Vervest (2004) Embedded coordination in a
business network. J. IT 19(4) 261-269.
Vervest, P., E. van Heck, K. Preiss, and L.-F. Pau (eds).
(2005). Smart business networks. Springer.
TOWARDS INDUSTRIAL SERVICE BUSINESS: Challenges in Designing ICT Support for the Networks of Companies
519