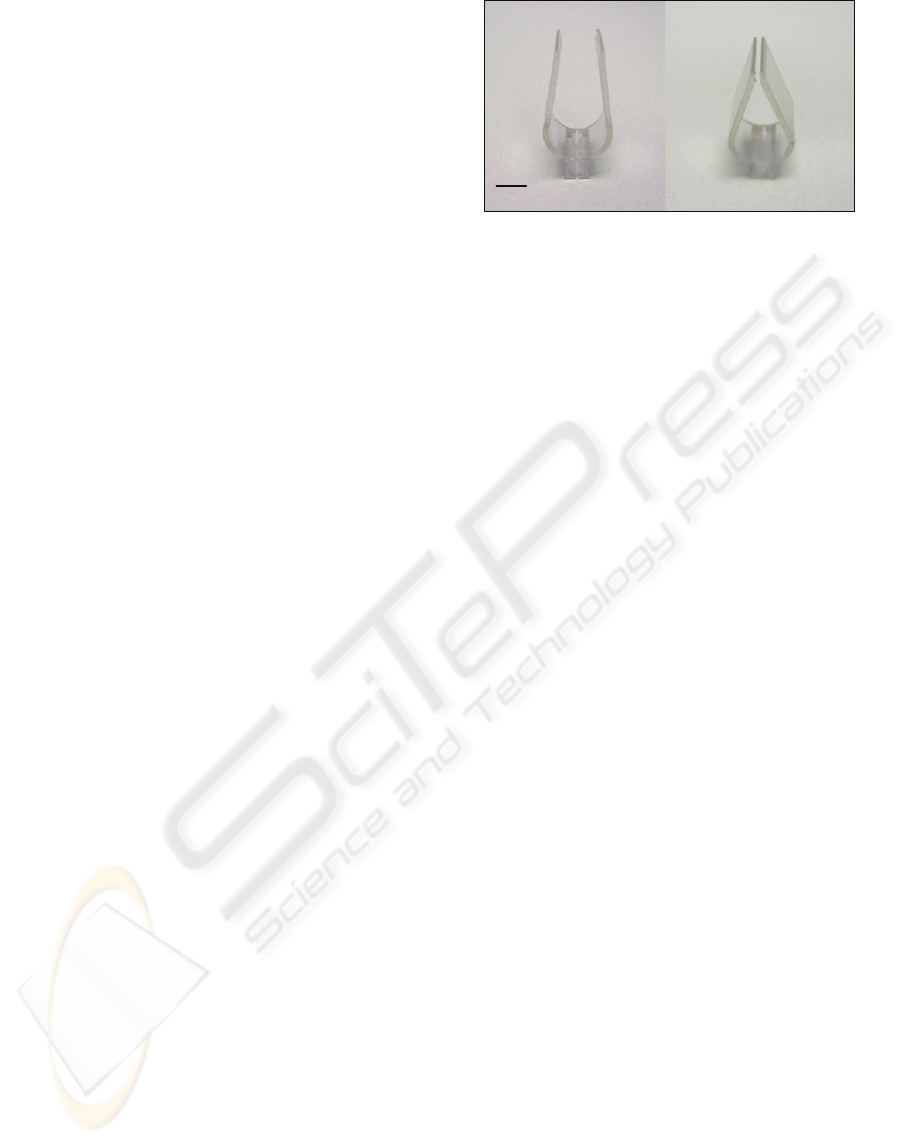
2 SHAPE-MEMORY POLYMERS
AND POTENTIAL BIODEVICES
Shape-memory polymers (SMPs) are materials that
show a mechanical response to external stimuli,
usually to changes of temperature. When these
materials are heated above their “activation”
temperature, there is a radical change from rigid
polymer to an elastic state that will sometimes allow
deformations of up to 400%. If the material is cooled
after manipulation it retains the shape imposed; the
said structure is “frozen” and returns to a rigid but
“unbalanced” state. If the material is again heated
above its glass transition temperature or “activation
temperature” it recovers its initial non-deformed
state.
The cycle can be repeated numerous times
without degrading the polymer and most suppliers
can formulate different materials with activation
temperatures of between –30 ºC y 260 ºC, depending
on the application required. Of all the polymers
developed that show shape memory properties, those
most worthy of mention are epoxy resins,
polyurethane resins, cross-linked polyethilene,
styrene-butadiene copolymers, polynorbornene and
other formulations (Lendlein, 2002, 2005, Liu,
2007).
They are therefore active materials that present
thermomechanical coupling and a high capability for
recovery from deformation, (much greater than that
shown by shape memory metal alloys), which
combined with their lower density and cost has
favoured the appearance of numerous applications.
Their properties permit applications for
manufacturing sensing devices or actuators,
especially for the aeronautics, automobile and
medical industry.
They have been proposed to develop numerous
medical devices such as self-expanding stents
(Wache, 2003), intelligent sutures (Lendlein, Kelch,
Langer, 2002, 2005), thrombectomy devices
(Wilson, 2006), active catheters (Yackaki, 2007),
drug delivery devices (Gall, 2004) or annuloplasty
systems (Díaz Lantada, 2008).
As an example of the capability of these
materials to recover their geometry Figure 1 shows
the closure of a pincer manufactured in epoxy resin
(whose trade name is Accura
®
60) when its memory
is activated by heating (under forced convection
using a hot-air gun with air at 80 ºC).
Similar devices, introducing appropriate changes
to their geometry according to the application, could
be used as the active end of a catheter to remove
harmful particles, clots and other elements.
Figure 1: Shape-memory effect in an epoxy resin pincer.
The following section explains how infrared
thermography can help optimise the development of
shape memory polymer-based medical devices.
3 THERMOGRAPHY AND SMP
BIODEVICE DEVELOPMENT
3.1 Operational Considerations
Generally speaking, the total power emitted per unit
of area is given by Stefan-Boltzmann’s Law, which
for a black body is expressed using the constant σ:
E
=
· T
4
(1)
It is important to point out that the concept of a
“black body” is an ideal concept as the real objects
are “grey bodies”, which means the concept of
emissivity “ε” has to be taken into account, giving
the equation:
E
=
ε ·
· T
4
(2)
Where emissivity shows values in the 0 < ε < 1
range and relates the radiation that would be emitted
by an ideal black body at the same temperature. This
constant is highly dependent on the material’s
surface and its finish, and on the wavelength and
surface temperature, and can have a marked
influence on the results of the tests performed with
infrared thermography equipments.
So, when conducting thermography tests, the
value of the said emissivity needs to be selected
depending on the material of the object or device
under study. The camera itself incorporates typical
values for different metals, polymers, ceramics and
other materials.
For materials not included in the camera
software, the emissivity of the material can be
determined by painting a part of the object or device
with black optical paint, for example Nextel Black
Velvet, which gives an emissivity very close to 0.94.
5 mm
BIODEVICES 2009 - International Conference on Biomedical Electronics and Devices
146