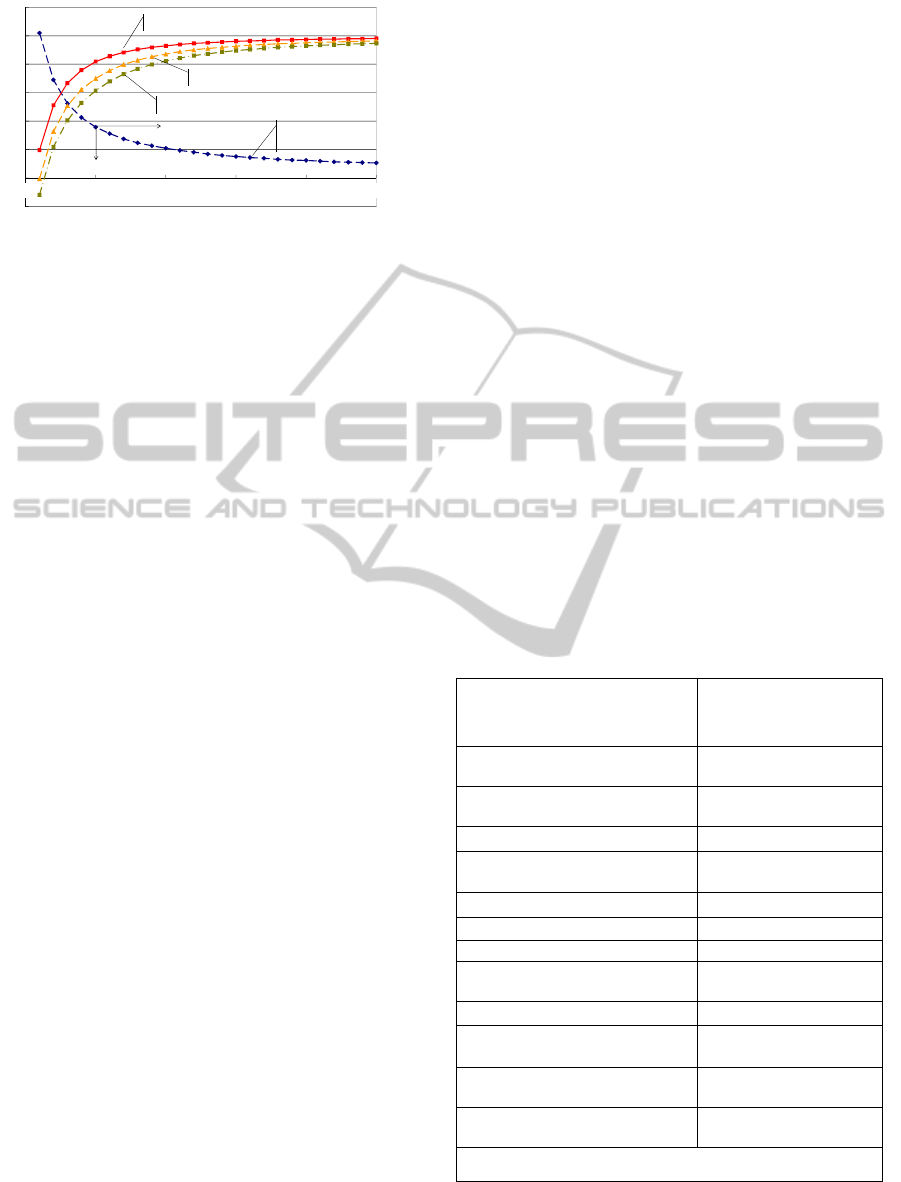
Figure 3: Relations among cost estimation MH, cost
estimation accuracy, and expected profits.
4.2 Multi-Period Evaluation on Order
Acceptance and Expected Profits
We analyse the relations between the order
acceptance and the expected profits through
successive multi-period operations using the MPOA
and Profit model, shown in Figure 2 and
APPENDIX. Table 2 shows the conditions of a
model company for this analysis.
We use two scenarios to compare profits based
on two different strategies for accepting orders, i.e.,
the high-order strategy (Case A), and the stable-
order strategy (Case B). The contractor tries to get
orders as many orders as possible at every period
under the high-order strategy. In contrast, the
contractor controls the volume of accepted orders at
a certain level via a multi-period basis in the case of
stable-order strategy. Namely, in Case A, the
volume of the order acceptance is set to 1,800
[MM$] at the 3
rd
period and to 1,200 [MM$] at other
periods. In Case B, the volume of the order
acceptance is set to 1,800 [MM$] at the 3
rd
period, to
600 [MM$] at the 4th period, and to 1,200 [MM$] at
other periods, to control the accepted orders through
entire periods as the 1,200 [MM$/Period] level.
Figures 4 and 5 show the orders, revenues, and
total costs over the periods, respectively, in Cases A
and B. In addition, Figure 6 shows a comparison of
profits in Case A and Case B over the periods.
As shown in Figures 4 and 6, in Case A, the
increased accepted orders at the 3
rd
period improves
revenues of the following three periods. Profits also
increase at the 4
th
period. However, profits start
decreasing from the 5
th
period, and it takes seven
periods to recover the profits at the 3
rd
period level.
If the same profit levels are maintained at the same
level of those of the 3
rd
period for 12 periods, the
total profits are 335 [MM$]. However, the increased
accepted orders at the 3
rd
period reduce profits
during the 6
th
to the 12
th
periods, and the total profits
for 12 periods are 190 [MM$] in Case A. In contrast,
as shown in Figures 5 and 6, the total profits for 12
periods are 318 [MM$] in Case B. The decline in
profits after the 4
th
period in Case A occurred
because of the reduced cost estimation MH by the
increased MH requirements for executing the orders
accepted at the 3
rd
period. Namely, the reduced cost
estimation MH decreases the cost estimation
accuracy, and thus the profits are reduced as
presented in the previous section. In Case B, since
the order acceptance at the 4
th
period is controlled,
and cost estimation MH is sufficiently maintained to
estimate cost accurately, the loss of profits is
reduced in comparison to that of Case A.
We can conclude based on these observations
that the strategy for accepting an adequate volume of
orders via multi-period operations is effective to
avoid decreasing cost estimation MH and cost
estimation accuracy, and thus a stable profit is the
end result.
Most contractors, in practice, tend to take a high-
order strategy. However, this strategy could reduce
cost estimation accuracy and reduce profits as
presented in this section. Namely, contractors in
ETO manufacturing should establish a strategy for
accepting orders in consideration of the balance of
MH for the cost estimation and execution of the
accepted orders via multi-period operations.
Table 2: Conditions of model company.
Rate of the i-th period revenue
on the accepted orders at the j-
th period (
j
i
ROER
)
0.333
The number of bidders (n)
including one’s own company
3 bidders
Periods for sales of accepted
order (NST)
3 Successive periods
Evaluation period -2 (1-NST) to 12
Probability density of the
bidding price
Normal distribution
Order execution cost (OEC) 100 [MM$ /order]
Rate of profit (ROP)
10%
Rate of MH cost (α
1
) 10%
Rate of materials & labour cost
(α
3
)
80%
Total in-house MH (MH
T
)
1,100 [M MH/period]
In-house senior engineer MH
(MH
S
)
440 [M MH/period]
Rate of senior engineer MH for
carry out orders (α
2
)
30%
In-house and out sourcing MH
rate (β
1
, β
2
)
100 [$/MH]
Parameters of Eq. (1) and Eq. (2) are shown in Table 1.
-2
0
2
4
6
8
10
12
00.511.522.5
Expected Profit per Order [MM$]
Cost Estimation MH [M MH/Order]
50 10 15 20 25
Cost Estimation
Accuracy
Expected Profit (Two Competitors)
Expected Profit (Three Competitors)
Expected Profit (Four Competitors)
1
0
Cost Estimation Accuracy [σ]
High
Low
A STRATEGY FOR ACCEPTING ORDERS IN ETO MANUFACTURING WITH COMPETITIVE BIDDING - Analysis
of Bidding Strategy and Expected Profits via Multi-Period Operations
383