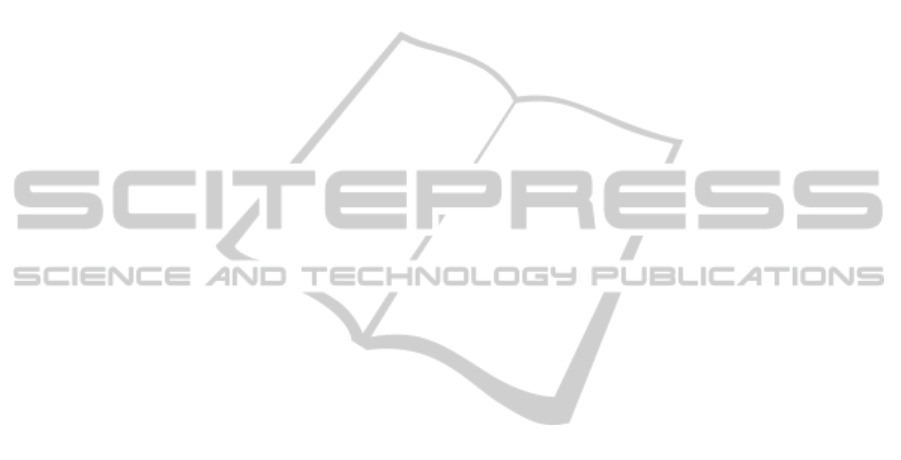
5 CONCLUSIONS
The material characterization of silicone rubber used
for vocal fold modeling by means of pipette aspiration
was proposed. Different aspiration areas were com-
pared with respect to the resulting displacement pro-
files. Finite element simulations based on frequency-
dependent material parameters were performed which
showed similar results revealing the potential of both,
the pipette aspiration technique for the characteriza-
tion of soft materials and the determination of dy-
namic material parameters using an Inverse Method
(Rupitsch and Lerch, 2009). By calculating the ra-
tio of the areas of the displacement profiles in or-
thogonal directions, a quantitative parameter for an
isotropic material behavior was presented. Because
this study validates both, the measurement procedure
and the numerical model, it provides a basis for fu-
ture studies dealing with similar characterizations of
synthetic materials used for vocal fold modeling.
ACKNOWLEDGEMENTS
The presented work was supported by Deutsche
Forschungsgemeinschaft (DFG, German Research
Foundation), Grant No. FOR 894/2, and by Grant
Number R01DC009616 from the U.S. National In-
stitute on Deafness and Other Communication Disor-
ders (NIDCD). Dr. Thomson gratefully acknowledges
support as a visiting professor from the University of
Erlangen Graduate School in Advanced Optical Tech-
nologies (SAOT).
REFERENCES
Alipour-Haghighi, F. and Titze, I. R. (1991). Elastic models
of vocal fold tissues. Journal of the Acoustical Society
of America, 90:1326–1331.
Aoki, T., Ohashi, T., Matsumoto, T., and Sato, M. (1997).
The pipette aspiration applied to the local stiffness
measurement of soft tissues. Annals of Biomedical
Engineering, 25:581–587.
Becker, S., Kniesburges, S., and M
¨
uller, S. (2009).
Flow-structure-acoustic interaction in a human voice
model. Journal of the Acoustical Society of America,
125:1351–1361.
Chan, R. W. and Titze, I. R. (1999). Viscoelastic shear
properties of human vocal fold mucosa: measurement
methodology and empirical results. Journal of the
Acoustical Society of America, 106:2008–2021.
Finck, C. and Dejeune, L. (2010). Handbook of Mammalian
Vocalization, chapter Structure and oscillatory func-
tion of the vocal folds, pages 427–438. Elsevier.
Gray, S. D. (2000). Cellular physiology of the vocal folds.
Voice disorders and Phonosurgery I, 33:679–697.
Hammond, T. H., Zhou, R., Hammond, E. H., Pawlak, A.,
and Gray, S. D. (1997). The intermediate layer: A
morphologic study of the elastin and hyaluronic acid
constituents of normal human vocal folds. Journal of
Voice, 11(1):59–66.
Henriksen, J. R. and Ipsen, J. H. (2004). Measurement of
membrane elasticity by micro-pipette aspiration. The
European Physical Journal E, 14:149–167.
Hirano, M. (1981). Clinical examination of Voice. Springer.
Ilg, J., Rupitsch, S. J., Sutor, A., and Lerch, R. (2012). De-
termination of dynamic material properties of silicone
rubber using one-point measurements and finite ele-
ment simulations. IEEE Transactions on Instrumen-
tation and Measurement, 61:3031–3038.
Kaltenbacher, M. (2007). Numerical Simulations of Mecha-
tronic Sensors and Actuators. Springer.
Matsumoto, T., Abe, H., Ohashi, T., Kato, Y., and Sato,
M. (2002). Local elastic modulus of atheroscle-
rotic lesions of rabbit thoracic aortas measured by
pipette aspiration method. Physiological Measure-
ment, 23:635–648.
Ohashi, T., Abe, H., Matsumoto, T., and Sato, M. (2005).
Pipette aspiration technique for the measurement of
nonlinear and anisotropic mechanical properties of
blood vessels under biaxial stretch. Journal of Biome-
chanics, 38:2248–2256.
Pickup, B. A. and Thomson, S. L. (2009). Influence of
asymmetric stiffness on the structural and aerody-
namic response of synthetic vocal fold models. Jour-
nal of Biomechanics, 42:2219–2225.
Rupitsch, S. J., Ilg, J., Sutor, A., Lerch, R., and D
¨
ollinger,
M. (2011). Simulation based estimation of dynamic
mechanical properties for viscoelastic materials used
for vocal fold models. Journal of Sound and Vibration,
330:4447–4459.
Rupitsch, S. J. and Lerch, R. (2009). Inverse method to es-
timate material parameters for piezoceramic disc ac-
tuators. Applied Physics A: Material Science & Pro-
ceedings, 97:735–740.
Weiss, S., Thomson, S. L., Lerch, R., D
¨
ollinger, M., and Su-
tor, A. (2013). Pipette aspiration applied to the charac-
terization of nonhomogeneous, transversely isotropic
materials used for vocal fold modeling. Journal of the
Mechanical Behavior of Biomedical Materials, doi:
10.1016/j.jmbbm.2012.08.005.
Z
¨
orner, S., Kaltenbacher, M., Lerch, R., Sutor, A., and
D
¨
ollinger, M. (2010). Measurement of the elastic-
ity modulus of soft tissues. Journal of Biomechanics,
43:1540–1545.
InfluenceofPipetteGeometryontheDisplacementProfileofIsotropicMaterialsusedforVocalFoldModeling
113