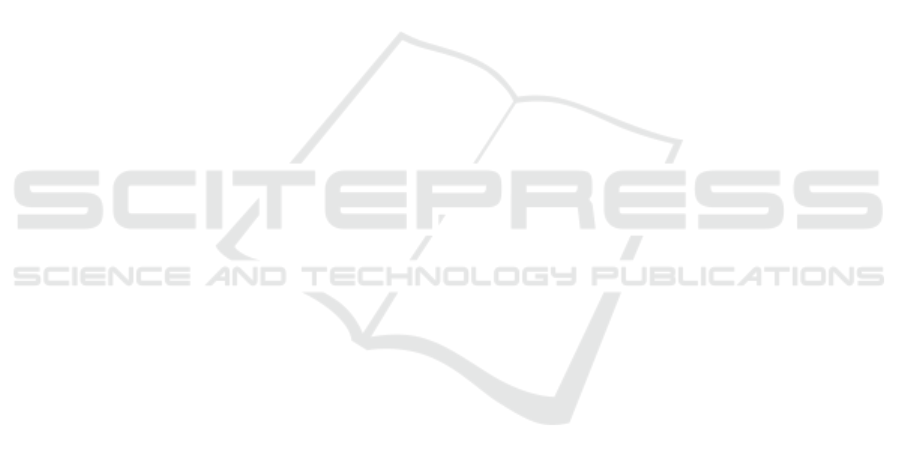
range cameras in 5 seconds without pattern. In In-
ternational Conference on Intelligent Robots and Sys-
tems. IEEE/RSJ.
Fischler, M. and Bolles, R. (1981). Random sampling con-
sensus: A paradigm for model fitting with applications
to image analysis and automated cartography. Com-
munications of the ACM, 24:381–385.
Fuchs, S. and May, S. (2008). Calibration and registra-
tion for precise surface reconstruction with time of
flight cameras. Int. J. Intell. Syst. Technol. Appl.,
5(3/4):274–284.
Guan, J., Deboeverie, F., Slembrouck, M., van Haeren-
borgh, D., van Cauwelaert, D., Veelaert, P., and
Philips, W. (2015). Extrinsic calibration of cam-
era networks using a sphere. Sensors, 15(8):18985–
19005.
Guan, J., Deboeverie, F., Slembrouck, M., Van Haeren-
borgh, D., Van Cauwelaert, D., Veelaert, P., and
Philips, W. (2016). Extrinsic calibration of camera
networks based on pedestrians. Sensors, 16(5).
Hansard, M., Lee, S., Choi, O., and Horaud, R. (2012). Time
of Flight Cameras: Principles, Methods, and Applica-
tions. SpringerBriefs in Computer Science. Springer.
Hoffman, K. and Kunze, R. (1971). Linear algebra.
Prentice-Hall mathematics series. Prentice-Hall.
Mao, J., Huang, X., and Jiang, L. (2010). A flexible solu-
tion to ax=xb for robot hand-eye calibration. In Pro-
ceedings of the 10th WSEAS International Conference
on Robotics, Control and Manufacturing Technology,
ROCOM’10, pages 118–122, Stevens Point, Wiscon-
sin, USA. World Scientific and Engineering Academy
and Society (WSEAS).
Pathak, K., Birk, A., Va
ˇ
skevi
ˇ
cius, N., and Poppinga, J.
(2010). Fast registration based on noisy planes with
unknown correspondences for 3-d mapping. Trans.
Rob., 26(3):424–441.
Pattinson, T. (2011). Quantification and Description of Dis-
tance Measurement Errors of a Time-of-Flight Cam-
era. PhD thesis, University of Stuttgard.
Penne, R., Mertens, L., and Ribbens, B. (2013). Planar
segmentation by time-of-flight cameras. In Advanced
Concepts for Intelligent Vision Systems, volume 8192
of Lecture Notes in Computer Science, pages 286–
297.
Penne, R., Raposo, C., Mertens, L., Ribbens, B., and
Araujo, H. (2015a). Investigating new calibration
methods without feature detection for tof cameras. Im-
age and Vision Computing, 43:5062.
Penne, R., Ribbens, B., and Mertens, L. (2015b). An incre-
mental procedure for the lateral calibration of a time-
of-flight camera by one image of a flat surface. Inter-
national Journal of Computer Vision, 113(2):81–91.
Petersen, K. B. and Pedersen, M. S. (2012). The Matrix
Cookbook. Technical University of Denmark. Version
20121115.
Pottmann, H. and Wallner, J. (2001). Computational Line
Geometry. Springer-Verlag New York, Inc., Secaucus,
NJ, USA.
Raposo, C., Barreto, J., and Nunes, U. (2013). Fast and ac-
curate calibration of a kinect sensor. In International
Conference on 3D Vision. IEEE.
Sabata, B. and Aggarwal, J. (1991). Estimation of motion
from a pair of range images: A review. CVGIP: Image
Understanding, 54(3):309 – 324.
Shah, M., Eastman, R. D., and Hong, T. (2012). An
overview of robot-sensor calibration methods for eval-
uation of perception systems. In Proceedings of the
Workshop on Performance Metrics for Intelligent Sys-
tems, PerMIS ’12, pages 15–20, New York, NY, USA.
ACM.
Teichman, A., Miller, S., and Thrun, S. (2013). Unsuper-
vised intrinsic calibration of depth sensors via SLAM.
In Robotics: Science and Systems.
Torr, P. and Zisserman, A. (2000). Mlesac: A new robust
estimator with application to estimating image geom-
etry. Comput. Vis. Image Underst., 78(1):138–156.
Tsai, R. Y. (1992). Radiometry. chapter A Versatile Cam-
era Calibration Technique for High-accuracy 3D Ma-
chine Vision Metrology Using Off-the-shelf TV Cam-
eras and Lenses, pages 221–244. Jones and Bartlett
Publishers, Inc., USA.
Vasconcelos, F., Barreto, J., and Nunes, U. (2012). A min-
imal solution for the extrinsic calibration of a cam-
era and a laser-rangefinder. IEEE Trans Pattern Anal
Mach Intell., 34(11):2097–2107.
Zhang, Z. (1989). Motion and structure from two perspec-
tive views: algorithms, error analysis, and error esti-
mation. 11(5):451–476.
Zhang, Z. (2000). A flexible new technique for camera cal-
ibration. 22(11):1330–1334.
New Error Measures for Evaluating Algorithms that Estimate the Motion of a Range Camera
515