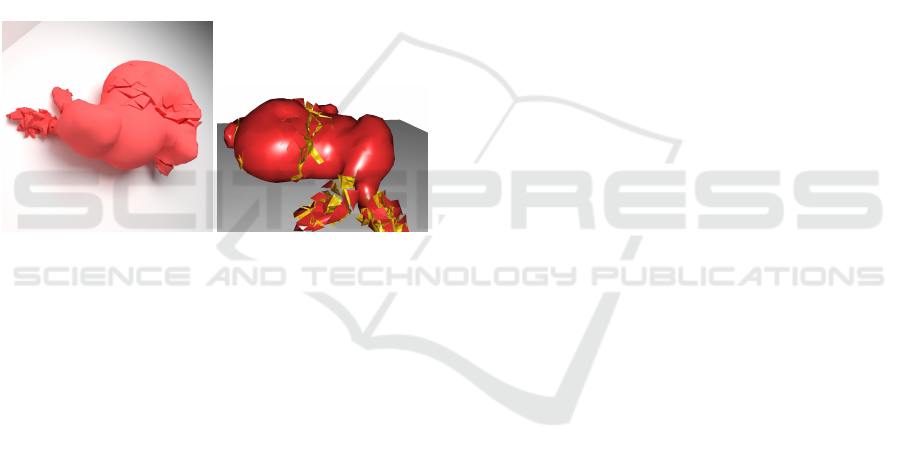
cess itself is not really parallelizable. We also want
to improve visualization, by displaying more complex
fracture surfaces as done in (Koschier et al., 2014) (it
would only be a visual artifact, with no cost on the
fracture process itself). Furthermore, one remaining
problem concerns the number of cracks (that is fan
splitting) that can be handled in one step. Indeed,
if only one crack is allowed per simulation step, no
shattering effect occurs in general. The number of
handled cracks should however be bounded.
ACKNOWLEDGMENTS
We would like to thank the anonymous reviewers for
their comments that helped us to improve this paper.
This work has benefited from the financial support of
a M.Sc internship from the MIRES federation.
Figure 8: Shattering fracture of Stanford Bunny. The bot-
tom picture aims at highlighting the fracture surface and the
different connected components.
REFERENCES
Bao, Z., Hong, J.-M., Teran, J., and Fedkiw, R. (2007).
Fracturing rigid materials. IEEE Transactions on Vi-
sualization and Computer Graphics, 13(2):370–378.
Baraff, D. and Witkin, A. (1998). Large steps in cloth simu-
lation. In Proceedings of ACM SIGGRAPH 98, Com-
puter Graphics annual conference series, pages 43–54,
Orlando.
Busaryev, O., Dey, T. K., and Wang, H. (2013). Adaptive
fracture simulation of multi-layered thin plates. ACM
Transactions on Graphics (Proceedings of ACM SIG-
GRAPH 2013), 32(4).
Chen, Z., Yao, M., Feng, R., and Wang, H. (2014). Physics-
inspired adaptive fracture refinement. ACM Transac-
tions on Graphics (Proceedings of ACM SIGGRAPH
2014), 33(4).
Cotin, S., Delingette, H., and Ayache, N. (1999). Real-time
elastic deformations of soft tissues for surgery simu-
lation. IEEE Transactions on Visualization and Com-
puter Graphics, 5(1):62–73.
Cotin, S., Delingette, H., and Ayache, N. (2000). A hybrid
elastic model allowing real-time cutting, deformation
and force-feedback for surgery training and simula-
tion. The Visual Computer, 16(8):437–452.
Glondu, L., Marchal, M., and Dumont, G. (2012). Real-
time simulation of brittle fracture using modal anal-
ysis. IEEE Transactions on Visualization and Com-
puter Graphics, 19(2):201–209.
Glondu, L., Schvartzman, S. C., Marchal, M., Dumont, G.,
and Otaduy, M. A. (2014). Fast collision detection for
fracturing rigid bodies. IEEE Transactions on Visual-
ization and Computer Graphics, 20(1):30–41.
Hahn, D. and Wojtan, C. (2015). High-resolution brittle
fracture simulation with boundary elements. ACM
Transactions on Graphics (Proceedings of ACM SIG-
GRAPH 2015), 34(4).
Hahn, D. and Wojtan, C. (2016). Fast approximations for
boundary element based brittle fracture simulation.
ACM Transactions on Graphics (Proceedings of ACM
SIGGRAPH 2016), 35(4).
Hilde, L., Meseure, P., and Chaillou, C. (2001). A fast im-
plicit integration method for solving dynamic equa-
tions of movement. In Proceedings of the ACM Con-
ference on Virtual Reality Software and Technology,
pages 71–76, Banff.
Koschier, D., Bender, J., and Thuerey, N. (2017). Robust
extended finite elements for complex cutting of de-
formables. ACM Transactions on Graphics (Proceed-
ings of ACM SIGGRAPH 2017), 36(4).
Koschier, D., Lipponer, S., and Bender, J. (2014). Adap-
tive tetrahedral meshes for brittle fracture simulation.
In Proceedings of the ACM SIGGRAPH/Eurographics
Symposium on Computer Animation, pages 57–66,
Copenhagen.
Lienhardt, P. (1994). N-dimensional generalized combi-
natorial maps and cellular quasimanifolds. Int. J. of
Computational Geometry and Applications, 4(3):275–
324.
Liu, N., He, X., Li, S., and Wang, G. (2011). Meshless sim-
ulation of brittle fracture. Computer Animation and
Virtual Worlds, 22(2–3):115–124.
Meseure, P., Darles, E., Skapin, X., and Touileb, Y. (2015).
Adaptive resolution for topology modifications in
physically-based animation. Technical report, XLIM
lab.
Michels, D. L., Luan, V. T., and Tokman, M. (2017). A
stiffly accurate integrator for elastodynamic problems.
ACM Transactions on Graphics (Proceedings of ACM
SIGGRAPH 2017), 36(4).
Molino, N., Bao, Z., and Fedkiw, R. (2004). A virtual node
algorithm for changing mesh topology during simula-
tion. ACM Transactions on Graphics (Proceedings of
ACM SIGGRAPH 2004), 23(3):385–392.
Muguercia, L., Bosch, C., and Patown, G. (2014). Frac-
ture modeling in computer graphics. Computers and
Graphics, 45(C):86–100.
M
¨
uller, M., Chentanez, N., and Kim, T.-Y. (2013).
Real time dynamic fracture with volumetric approxi-
mate convex decompositions. ACM Transactions on
Graphics (Proceedings of ACM SIGGRAPH 2013),
32(4).
GRAPP 2018 - International Conference on Computer Graphics Theory and Applications
38