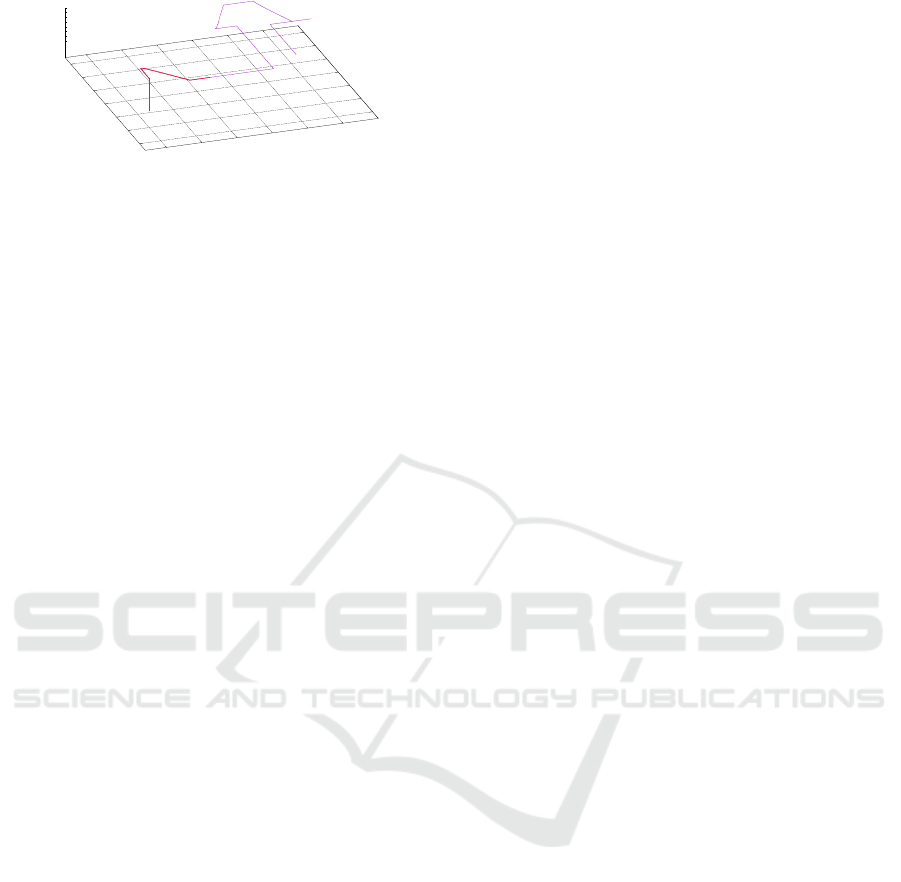
-100
-80
-60
-40
-20
0
20
0
50
100
150
200
250
300
70
60
50
40
30
20
10
0
X
Y
Z
Figure 11: Adaptive parameter adjustment. Optimal param-
eters are interactively searched for using the first part of data
(red line), and then the whole trajectory (purple line) can be
automatically reconstructed.
scape will influence the output of ultrasonic senor. In
the future work, combining with more sensors, tra-
jectory can be reconstructed in more complicated en-
vironment. Besides, our method does better in re-
constructing straight lines than in curves. However,
curves can be divided into short line segments, hence
theoretically our approach is feasible in reconstruct-
ing trajectory in arbitrary shapes. Note that the flight
route of the drone are not as perfect as our design,
because it will be influenced by the environment and
battery power.
Our trajectory reconstruction method can be ap-
plied in various applications. Since the trajectory can
provide important view point information, 3D recon-
struction, map building or stereoscopic video synthe-
sizing may be potential future research directions.
ACKNOWLEDGEMENTS
This work is partially supported by NSFC grants
#61370112 and #61602012, and the Key Labora-
tory of Machine Perception (Ministry of Education),
Peking University.
REFERENCES
Amzajerdian, F., Pierrottet, D., Petway, L., Hines, G., and
Roback, V. (2011). Lidar systems for precision navi-
gation and safe landing on planetary bodies. In Proc.
SPIE, volume 8192, page 819202.
Biswas, J. and Veloso, M. (2010). Wifi localization and
navigation for autonomous indoor mobile robots. In
Robotics and Automation (ICRA), 2010 IEEE Inter-
national Conference on, pages 4379–4384.
Bristeau, P.-J., Callou, F., Vissiere, D., and Petit, N.
(2011). The navigation and control technology inside
the ar. drone micro uav. IFAC Proceedings Volumes,
44(1):1477–1484.
Chen, Y. and Kobayashi, H. (2002). Signal strength based
indoor geolocation. In Communications, 2002. ICC
2002. IEEE International Conference on, volume 1,
pages 436–439.
Faragher, R. and Harle, R. (2015). Location fingerprint-
ing with bluetooth low energy beacons. IEEE journal
on Selected Areas in Communications, 33(11):2418–
2428.
Farrell, J. (2008). Aided navigation: GPS with high rate
sensors.
Fredrikstad, T. E. N. (2016). Vision aided inertial naviga-
tion. Master’s thesis, NTNU.
Hazas, M. and Hopper, A. (2006). Broadband ultrasonic lo-
cation systems for improved indoor positioning. IEEE
Transactions on mobile Computing, 5(5):536–547.
Huang, A. S., Bachrach, A., Henry, P., Krainin, M., Matu-
rana, D., Fox, D., and Roy, N. (2017). Visual odome-
try and mapping for autonomous flight using an rgb-d
camera. In Robotics Research, pages 235–252.
Kleusberg, A. and Langley, R. B. (1990). The limitations of
gps. GPS World, 1(2).
Kopf, J., Cohen, M. F., and Szeliski, R. (2014). First-person
hyper-lapse videos. ACM Transactions on Graphics
(TOG), 33(4):78.
Lee, T., Leoky, M., and McClamroch, N. H. (2010). Ge-
ometric tracking control of a quadrotor uav on se (3).
In Decision and Control (CDC), 2010 49th IEEE Con-
ference on, pages 5420–5425.
Mourikis, A. I., Trawny, N., Roumeliotis, S. I., Johnson,
A. E., Ansar, A., and Matthies, L. (2009). Vision-
aided inertial navigation for spacecraft entry, de-
scent, and landing. IEEE Transactions on Robotics,
25(2):264–280.
N
¨
ageli, T., Meier, L., Domahidi, A., Alonso-Mora, J., and
Hilliges, O. (2017). Real-time planning for automated
multi-view drone cinematography. ACM Transactions
on Graphics (TOG), 36(4):132.
Park, M. and Gao, Y. (2008). Error and performance analy-
sis of mems-based inertial sensors with a low-cost gps
receiver. Sensors, 8(4):2240–2261.
Pedley, M. (2013). High precision calibration of a three-axis
accelerometer. Freescale Semiconductor Application
Note, 1.
Pflugfelder, R. and Bischof, H. (2010). Localization and
trajectory reconstruction in surveillance cameras with
nonoverlapping views. IEEE Transactions on Pattern
Analysis and Machine Intelligence, 32(4):709–721.
Rencken, W. D. (1993). Concurrent localisation and map
building for mobile robots using ultrasonic sensors. In
IROS’93. Proceedings of the 1993 IEEE/RSJ Interna-
tional Conference on, volume 3, pages 2192–2197.
Silvatti, A. P., Cerveri, P., Telles, T., Dias, F. A., Baroni, G.,
and Barros, R. M. (2013). Quantitative underwater
3d motion analysis using submerged video cameras:
accuracy analysis and trajectory reconstruction. Com-
puter methods in biomechanics and biomedical engi-
neering, 16(11):1240–1248.
Suh, Y. S. (2003). Attitude estimation using low cost ac-
celerometer and gyroscope. In Science and Technol-
ogy, 2003. Proceedings KORUS 2003. The 7th Korea-
Russia International Symposium on, volume 2, pages
423–427.
Suvorova, S., Vaithianathan, T., and Caelli, T. (2012).
Action trajectory reconstruction from inertial sensor
Sensor-fusion-based Trajectory Reconstruction for Mobile Devices
57