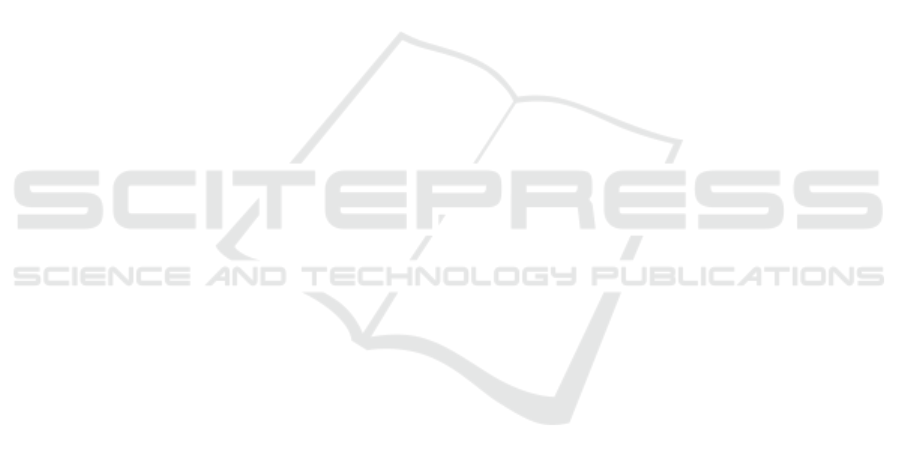
than cos(α
sharp
) = −0.85, because for corners that are
sharper than this value the oscillation increases signif-
icantly when we apply the local spline approximation
method.
9 CONCLUSIONS
We developed an algorithm for generating curvature-
optimized tool paths for 5-axis milling. The gener-
ated tool paths consist of a position B-spline curve
and an orientation B-spline curve. The position curve
can be handles like a 3-axis machining tool path. For
the orientation curve, the control points are restricted
to stay within a frustum formed by the lead and tilt
tolerances. To obtain an acceptable quality-speed ra-
tio, we combine two algorithms: a local version of
the sleeve-algorithm and a local spline approximation
with G
2
-continuity connections. Corresponding po-
sition and orientation point groups are solved by the
same algorithm. We solve the orientation problem on
the sphere to avoid any complications caused by loca-
tion of position points. The splitting of the original
orientation curve into groups is performed with re-
spect to the corresponding position point groups and
complexity of the groups. The local spline approxi-
mation algorithm is very efficient and produces good
results for simple groups, while the local sleeve algo-
rithm is less efficient but produces high-quality results
even for complicated groups.
The created algorithm can be used as a part of a
micro milling process. This approach provides new
possibilities for calculating velocity, acceleration, and
jerk profiles. The benefits are that profiles are easier
to compute and that the milling can generally be per-
formed with a higher velocity. The latter is essential
for practical purposes, since the higher the velocity of
the tool tip is the faster is the manufacturing process.
ACKNOWLEDGMENTS
This work was supported by BMWi under grant num-
ber 5166/50258.
REFERENCES
Robert V. Fleisig and Allan D. Spence (2001) Constant feed
and reduced angular acceleration interpolation algo-
rithm for multi-axis machining. Computer Aided De-
sign 33(1):1-15.
Cha-Soo Jun, Kyungduck Cha, Yuan-Shin Lee (2003) Op-
timizing tool orientations for 5-axis machining by
configuration-space search method. Computer-Aided
Design 35(6):549-566.
Taejung Kim and Sanjay E. Sarma (2002) Toolpath gen-
eration along directions of maximum kinematic per-
formance; a first cut at machine-optimal paths.
Computer-Aided Design 34(6): 453-468.
Jean Marie Langeron, Emmanuel Duc, Claire Lartigue,
Pierre Bourdet (2004) A new format for 5-axis tool
path computation, using B-spline curves. Computer-
Aided Design 36(12): 1219-1229.
Sylvain Lavernhe, Christophe Tournier and Claire Lartigue
(2007) Kinematical performance prediction in multi-
axis machining for process planning optimization.
The International Journal of Advanced Manufacturing
Technology 37(5-6): 534-544.
Wei Li, Yadong Liu, Kazuo Yamazaki, Makoto Fujisima
and Masahiko Mori (2008) The design of a NURBS
pre-interpolator for five-axis machining. The Interna-
tional Journal of Advanced Manufacturing Technol-
ogy 36(9-10):927-935.
Xianbing Liua, Fahad Ahmada, Kazuo Yamazakia, and
Masahiko Mori (2005) Adaptive interpolation scheme
for NURBS curves with the integration of machining
dynamics. International Journal of Machine Tools and
Manufacture 45(4-5):433-444.
David Lutterkort and J
¨
org Peters (1999) Tight lin-
ear envelopes for splines. Numerische Mathematik
89(4):735-748.
David Lutterkort and J
¨
org Peters (1999) Smooth path in
a polygon channel. In: Proceedings of the 15th an-
nual symposium on Computational Geometry 316-
321, ACM Press.
Ashish Myles and J
¨
org Peters (2005) Threading splines
through 3D channels. Computer-Aided Design
37(2):139-148.
J
¨
org Peters and Xiaobin Wu (2004) Sleeves for planar spline
curves. Computer-Aided Design 21(6):615-635.
Les A. Piegl (1991) On NURBS: a Survey. IEEE Computer
Graphics and Applications 11(1):55-71.
Les A. Piegl and Wayne Tiller (1997) The NURBS Book.
Springer.
Les A. Piegl and Wayne Tiller (2002) Data approximation
using biarcs. 18:59-65. Engineering with Computers,
Springer.
Hartmut Prautzsch, Wolfgang Boehm and Marco Paluszny
(2002) B
´
ezier and B-Spline Techniques. Springer.
Selinger, Jevgenija and Linsen, Lars (2011) Efficient
Curvature-optimized G2-continuous Path Generation
with Guaranteed Error Bound for 3-axis Machining.
in Proceedings of the 15th International Conference
on Information Visualisation 519–527. 5th Interna-
tional Conference on Geometric Modeling and Imag-
ing (GMAI 2011) . IEEE Computer Society.
Rong Zhen Xu, Le Xie, Cong Xin Li, and Dao Shan Du
(2008) Adaptive parametric interpolation scheme with
limited acceleration and jerk values for NC machin-
ing. The International Journal of Advanced Manufac-
turing Technology 36(3-4):343-354.
Wang Yongzhang, Ma Xiongbo, Chen Liangji, Han Zhenyu
(2007) Realization Methodology of a 5-axis Spline In-
terpolator in an Open CNC System. Chinese Journal
of Aeronautics 20(4):362-369.
GRAPP 2018 - International Conference on Computer Graphics Theory and Applications
70