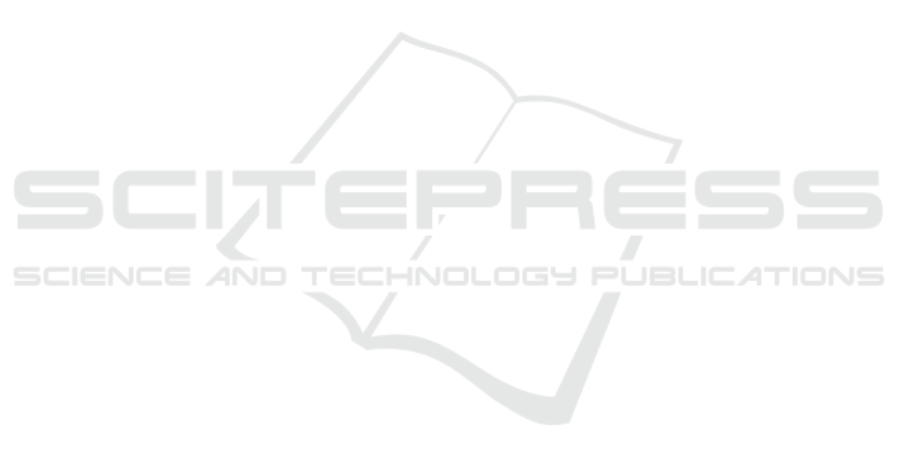
REFERENCES
Baraff, D. and Witkin, A. (1998). Large steps in cloth
simulation. In Proceedings of the 25th annual con-
ference on Computer graphics and interactive tech-
niques, pages 43–54. ACM.
Bender, J. and Deul, C. (2013). Adaptive cloth simula-
tion using corotational finite elements. Computers &
Graphics, 37(7):820–829.
Bielser, D., Glardon, P., Teschner, M., and Gross, M.
(2004). A state machine for real-time cutting of tetra-
hedral meshes. Graphical Models, 66(6):398–417.
Bowyer, A. (1981). Computing dirichlet tessellations. The
computer journal, 24(2):162–166.
Busaryev, O., Dey, T. K., and Wang, H. (2013). Adaptive
fracture simulation of multi-layered thin plates. ACM
Transactions on Graphics (TOG), 32(4):52.
Cakir, O., Yazici, R., and Cakir, O. (2009). Real-time
cutting simulation based on stiffness-warped fem.
In Computer and Information Sciences, 2009. ISCIS
2009. 24th International Symposium on, pages 721–
724. IEEE.
Cotin, S., Delingette, H., and Ayache, N. (2000). A hy-
brid elastic model for real-time cutting, deformations,
and force feedback for surgery training and simula-
tion. The Visual Computer, 16(8):437–452.
Courtecuisse, H., Jung, H., Allard, J., Duriez, C., Lee,
D. Y., and Cotin, S. (2010). Gpu-based real-time
soft tissue deformation with cutting and haptic feed-
back. Progress in biophysics and molecular biology,
103(2):159–168.
Felippa, C. A. and Haugen, B. (2005). A unified formu-
lation of small-strain corotational finite elements: I.
theory. Computer Methods in Applied Mechanics and
Engineering, 194(21):2285–2335.
Georgii, J. and Westermann, R. (2008). Corotated finite
elements made fast and stable. VRIPHYS, 8:11–19.
Kaufmann, P., Martin, S., Botsch, M., Grinspun, E., and
Gross, M. (2009). Enrichment textures for detailed
cutting of shells. In ACM Transactions on Graphics
(TOG), volume 28, page 50. ACM.
Koh, W., Narain, R., and O’Brien, J. F. (2014). View-
dependent adaptive cloth simulation. In Proceedings
of the ACM SIGGRAPH/Eurographics Symposium on
Computer Animation, pages 159–166. Eurographics
Association.
Koschier, D., Bender, J., and Thuerey, N. (2017). Robust
extended finite elements for complex cutting of de-
formables. ACM Transactions on Graphics (TOG),
36(4):55.
Narain, R., Pfaff, T., and O’Brien, J. F. (2013). Folding
and crumpling adaptive sheets. ACM Transactions on
Graphics (TOG), 32(4):51.
Nesme, M., Kry, P. G., Je
ˇ
r
´
abkov
´
a, L., and Faure, F. (2009).
Preserving topology and elasticity for embedded de-
formable models. In ACM Transactions on Graphics
(TOG), volume 28, page 52. ACM.
Nienhuys, H.-W. and van der Stappen, A. F. (2004). A de-
launay approach to interactive cutting in triangulated
surfaces. In Algorithmic Foundations of Robotics V,
pages 113–129. Springer.
Pfaff, T., Narain, R., de Joya, J. M., and O’Brien, J. F.
(2014). Adaptive tearing and cracking of thin sheets.
ACM Transactions on Graphics (TOG), 33(4):110.
Pietroni, N., Ganovelli, F., Cignoni, P., and Scopigno, R.
(2009). Splitting cubes: a fast and robust technique
for virtual cutting. The Visual Computer, 25(3):227–
239.
Rebay, S. (1993). Efficient unstructured mesh genera-
tion by means of delaunay triangulation and bowyer-
watson algorithm. Journal of computational physics,
106(1):125–138.
Seiler, M., Steinemann, D., Spillmann, J., and Harders, M.
(2011). Robust interactive cutting based on an adap-
tive octree simulation mesh. The Visual Computer,
27(6-8):519–529.
Serby, D., Harders, M., and Sz
´
ekely, G. (2001). A
new approach to cutting into finite element mod-
els. In Medical Image Computing and Computer-
Assisted Intervention–MICCAI 2001, pages 425–433.
Springer.
Shewchuk, J. R. (2002). Delaunay refinement algorithms
for triangular mesh generation. Computational geom-
etry, 22(1-3):21–74.
Sifakis, E., Der, K. G., and Fedkiw, R. (2007). Arbitrary
cutting of deformable tetrahedralized objects. In Pro-
ceedings of the 2007 ACM SIGGRAPH/Eurographics
symposium on Computer animation, pages 73–80. Eu-
rographics Association.
Souza, M. S., Wangenheim, A., and Comunello, E. (2014).
Fast simulation of cloth tearing. SBC Journal on In-
teractive Systems, 5(1):44–48.
Steinemann, D., Harders, M., Gross, M., and Szekely, G.
(2006). Hybrid cutting of deformable solids. In Vir-
tual Reality Conference, 2006, pages 35–42. IEEE.
Turkiyyah, G. M., Karam, W. B., Ajami, Z., and Nasri, A.
(2011). Mesh cutting during real-time physical simu-
lation. Computer-Aided Design, 43(7):809–819.
Wu, J., Westermann, R., and Dick, C. (2015). A survey
of physically based simulation of cuts in deformable
bodies. In Computer Graphics Forum, volume 34,
pages 161–187. Wiley Online Library.
Yeung, Y.-H., Crouch, J., and Pothen, A. (2016). Inter-
actively cutting and constraining vertices in meshes
using augmented matrices. ACM Transactions on
Graphics (TOG), 35(2):18.
GRAPP 2018 - International Conference on Computer Graphics Theory and Applications
190