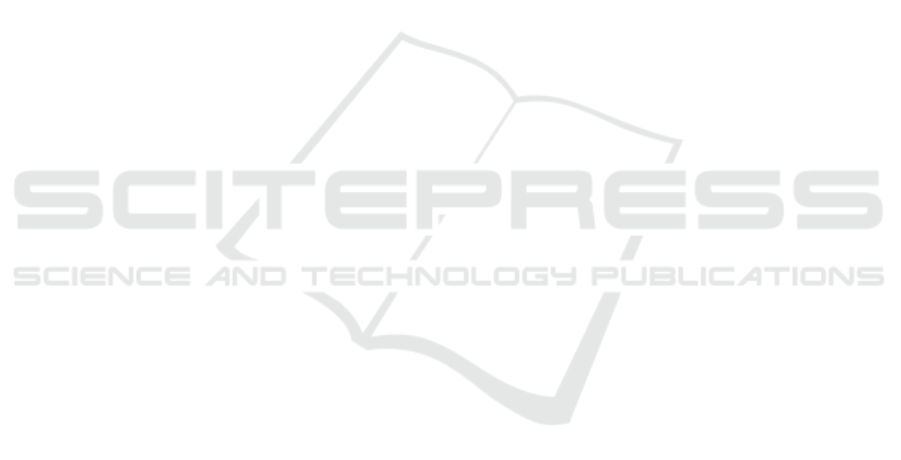
Platform for Future Production and from the EU
project ReconCell (FP7-ICT-680431) is gratefully
acknowledged.
REFERENCES
Aldoma, A., Marton, Z.-C., Tombari, F., Wohlkinger, W.,
Potthast, C., Zeisl, B., Rusu, R. B., Gedikli, S., and
Vincze, M. (2012). Tutorial: Point cloud library:
Three-dimensional object recognition and 6 dof pose
estimation. IEEE Robotics & Automation Magazine,
19(3):80–91.
Buch, A. G., Kraft, D., Kamarainen, J.-K., Petersen, H. G.,
and Kr
¨
uger, N. (2013). Pose estimation using local
structure-specific shape and appearance context. In
Robotics and Automation (ICRA), 2013 IEEE Inter-
national Conference on, pages 2080–2087. IEEE.
Chen, S., Li, Y., and Kwok, N. M. (2011). Active vi-
sion in robotic systems: A survey of recent develop-
ments. The International Journal of Robotics Rese-
arch, 30(11):1343–1377.
Costa, A. and Nannicini, G. (2015). Rbfopt: an open-
source library for black-box optimization with costly
function evaluations. Under review.
Dong, Y., Hutchens, T., Mullany, B., Morse, E., and Da-
vies, A. (2014). Using a three-dimensional opti-
cal simulation to investigate uncertainty in image-
based dimensional measurements. Optical Engineer-
ing, 53(9):092007–092007.
Everitt, C. (2001). Projective texture mapping. White paper,
NVidia Corporation, 4.
Geiger, A., Roser, M., and Urtasun, R. (2010). Efficient
large-scale stereo matching. In Asian conference on
computer vision, pages 25–38. Springer.
Großmann, B., Siam, M., and Kr
¨
uger, V. (2015). Compa-
rative Evaluation of 3D Pose Estimation of Industrial
Objects in RGB Pointclouds, pages 329–342. Springer
International Publishing, Cham.
Huntley, J. M. and Saldner, H. (1993). Temporal phase-
unwrapping algorithm for automated interferogram
analysis. Applied Optics, 32(17):3047–3052.
Irgenfried, S., Tchouchenkov, I., W
¨
orn, H., Koci, R., Hana-
cek, P., Kunovski, J., Zboril, F., Samek, J., and Pe-
ringer, P. (2011). Cadavision: a simulation frame-
work for machine vision prototyping. In Proceedings
of the Second International Conference on Computer
Modelling and Simulation, pages 59–67.
Jørgensen, T. B., Buch, A. G., and Kraft, D. (2015). Ge-
ometric edge description and classification in point
cloud data with application to 3d object recognition.
In Proceedings of the 10th International Conference
on Computer Vision Theory and Applications (VISI-
GRAPP), pages 333–340.
Knoop, S., Vacek, S., and Dillmann, R. (2006). Sensor fu-
sion for 3d human body tracking with an articulated 3d
body model. In Robotics and Automation, 2006. ICRA
2006. Proceedings 2006 IEEE International Confe-
rence on, pages 1686–1691. IEEE.
Kouteck
`
y, T., Palou
ˇ
sek, D., and Brandejs, J. (2015). Ap-
plication of a reflectance model to the sensor planning
system. In SPIE Optical Metrology, pages 953005–
953005. International Society for Optics and Photo-
nics.
Kr
¨
uger, N., Ude, A., Petersen, H. G., Nemec, B., Ellekilde,
L.-P., Savarimuthu, T. R., Rytz, J. A., Fischer, K.,
Buch, A. G., Kraft, D., et al. (2014). Technologies
for the fast set-up of automated assembly processes.
KI-K
¨
unstliche Intelligenz, 28(4):305–313.
Mavrinac, A., Chen, X., and Alarcon-Herrera, J. L. (2015).
Semiautomatic model-based view planning for active
triangulation 3-d inspection systems. IEEE/ASME
Transactions on Mechatronics, 20(2):799–811.
Medeiros, E., Doraiswamy, H., Berger, M., and Silva, C. T.
(2014). Using physically based rendering to bench-
mark structured light scanners. In Computer Graphics
Forum, volume 33, pages 71–80. Wiley Online Li-
brary.
Nilsson, J., Ericsson, M., and Danielsson, F. (2009). Virtual
machine vision in computer aided robotics. In 2009
IEEE Conference on Emerging Technologies & Fac-
tory Automation, pages 1–8. IEEE.
Papazov, C. and Burschka, D. (2010). An efficient ransac
for 3d object recognition in noisy and occluded sce-
nes. In Asian Conference on Computer Vision, pages
135–148. Springer.
Rios, L. M. and Sahinidis, N. V. (2013). Derivative-free op-
timization: a review of algorithms and comparison of
software implementations. Journal of Global Optimi-
zation, 56(3):1247–1293.
Rossmann, J., Steil, T., and Springer, M. (2012). Valida-
ting the camera and light simulation of a virtual space
robotics testbed by means of physical mockup data.
In International symposium on artificial intelligence,
robotics and automation in space (i-SAIRAS), pages
1–6.
Rozantsev, A., Lepetit, V., and Fua, P. (2015). On rendering
synthetic images for training an object detector. Com-
puter Vision and Image Understanding, 137:24–37.
Schluse, M., Schlette, C., Waspe, R., and Roßmann, J.
(2013). Advanced 3d simulation technology for ero-
botics: Techniques, trends, and chances. In 2013 Sixth
International Conference on Developments in eSys-
tems Engineering, pages 151–156.
Takei, S., Akizuki, S., and Hashimoto, M. (2014). 3d object
recognition using effective features selected by evalu-
ating performance of discrimination. In Control Au-
tomation Robotics & Vision (ICARCV), 2014 13th In-
ternational Conference on, pages 70–75. IEEE.
Ye, M., Wang, X., Yang, R., Ren, L., and Pollefeys, M.
(2011). Accurate 3d pose estimation from a single
depth image. In Computer Vision (ICCV), 2011 IEEE
International Conference on, pages 731–738. IEEE.
Simulation-based Optimization of Camera Placement in the Context of Industrial Pose Estimation
533