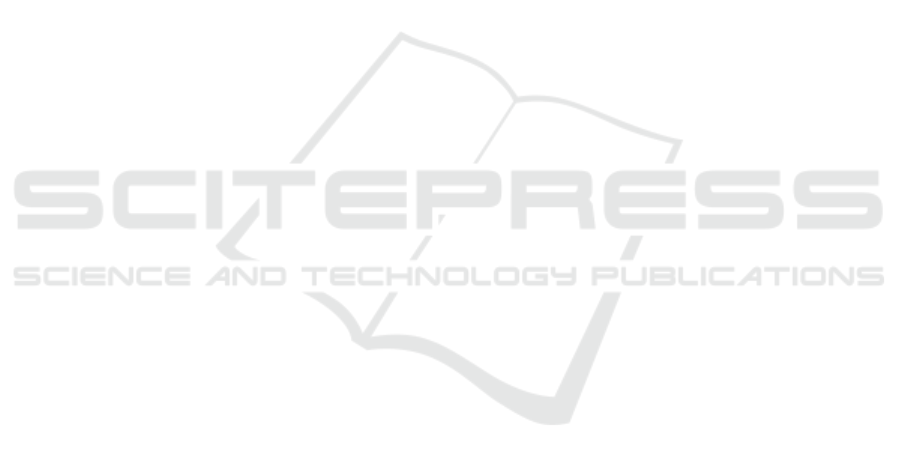
REFERENCES
Allen, J. (2007). Photoplethysmography and its application
in clinical physiological measurement. Physiological
measurement, 28(3), R1-R39. doi:10.1088/0967-
3334/28/3/R01
Andersson, L. M., Okada, H., Miura, R., Zhang, Y.,
Yoshioka, K., Aso, H., and Itoh, T. (2016). Wearable
wireless estrus detection sensor for cows. Computers
and Electronics in Agriculture, 127, 101-108. doi:
10.1016/j.compag.2016.06.007
Asada, H. H., Shaltis, P., Reisner, A., Rhee, S., and
Hutchinson, R. C. (2003). Mobile monitoring with
wearable photoplethysmographic biosensors. IEEE
engineering in medicine and biology magazine, 22(3),
28-40. doi: 10.1109/MEMB.2003.1213624
Díaz, S. E., Pérez, J. C., Mateos, A. C., Marinescu, M. C.,
and Guerra, B. B. (2011). A novel methodology for the
monitoring of the agricultural production process based
on wireless sensor networks. Computers and
Electronics in Agriculture, 76(2), 252-265. doi:
10.1016/j.compag.2011.02.004
Ishikawa, I., Sawada, R., Higurashi, E., Sanada, S., and
Chino, D. (2007). Integrated micro-displacement sen-
sor that measures tilting angle and linear movement of
an external mirror. Sensors and Actuators A: Physical,
138(2), 269-275. doi: 10.1016/j.sna.2007.03.027
Iwasaki, T., Takeshita, T., Arinaga, Y., Uemura, K., Ando,
H., Takeuchi, S., ... and Sawada, R. (2015). Shearing
force measurement device with a built-in integrated
micro displacement sensor. Sensors and Actuators A:
Physical, 221, 1-8. doi: 10.1016/j.sna.2014.09.029
Iwasaki, W., Sathuluri, R. R., Niwa, O., & Miyazaki, M.
(2015). Influence of Contact Force on Electrochemical
Responses of Redox Species Flowing in Nitrocellulose
Membrane at Micropyramid Array Electrode.
Analytical Sciences, 31(7), 729-732. doi: 10.2116/
analsci.31.729
Nishihara, K., Iwasaki, W., Nakamura, M., Higurashi, E.,
Soh, T., Itoh, T., ... and Sawada, R. (2013).
Development of a wireless sensor for the measurement
of chicken blood flow using the laser Doppler blood
flow meter technique. IEEE Transactions on
Biomedical Engineering, 60(6), 1645-1653. doi:
10.1109/TBME.2013.2241062
Nogami, H., Okada, H., Takamatsu, S., Kobayashi, T.,
Maeda, R., & Itoh, T. (2013). Unique activity-meter
with piezoelectric poly (vinylidene difluoride) films
and self weight of the sensor nodes. Japanese Journal of
Applied Physics, 52(9S1), 09KD15. doi: 10.7567/
JJAP.52.09KD15
Okada, H., Itoh, T., Suzuki, K., and Tsukamoto, K. (2009,
October). Wireless sensor system for detection of avian
influenza outbreak farms at an early stage. In Sensors,
2009 IEEE (pp. 1374-1377). IEEE. doi: 10.1109/
ICSENS.2009.5398422
Olivares, A., Olivares, G., Mula, F., Górriz, J. M., and
Ramírez, J. (2011). Wagyromag: Wireless sensor
network for monitoring and processing human body
movement in healthcare applications. Journal of
systems architecture, 57(10), 905-915. doi: 10.1016/
j.sysarc.2011.04.001
Spencer, B. F., Park, J. W., Mechitov, K. A., Jo, H., and
Agha, G. (2017). Next Generation Wireless Smart
Sensors Toward Sustainable Civil Infrastructure.
Procedia Engineering, 171, 5-13. doi: 10.1016/
j.proeng.2017.01.304
Suzuki, K., Okada, H., Itoh, T., Tada, T., Mase, M.,
Nakamura, K., ... and Tsukamoto, K. (2009).
Association of increased pathogenicity of Asian H5N1
highly pathogenic avian influenza viruses in chickens
with highly efficient viral replication accompanied by
early destruction of innate immune responses. Journal
of virology, 83(15), 7475-7486. doi: 10.1128/
JVI.01434-08
Takeshita, T., Harisaki, K., Ando, H., Higurashi, E.,
Nogami, H., and Sawada, R. (2016). Development and
evaluation of a two-axial shearing force sensor
consisting of an optical sensor chip and elastic gum
frame. Precision Engineering, 45, 136-142. doi:
10.1016/j.precisioneng.2016.02.004
Yamashita, T., Okada, H., Kobayashi, T., Togashi, K.,
Zymelka, D., Takamatsu, S., and Itoh, T. (2016). Ultra-
thin piezoelectric strain sensor array integrated on
flexible printed circuit for structural health monitoring.
In SENSORS, 2016 IEEE (pp. 1-3). IEEE. doi:
10.1109/ICSENS.2016.7808972
BIODEVICES 2018 - 11th International Conference on Biomedical Electronics and Devices
76