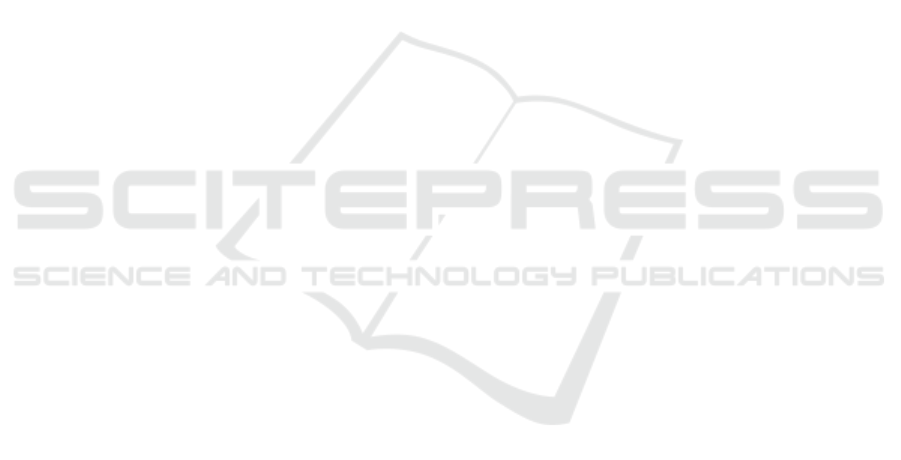
tool and our system will help to overcome the latter
limitation.
REFERENCES
Bein, M., Havemann, S., Stork, A., and Fellner, D. (2009).
Sketching subdivision surfaces. Sketch Based Inter-
faces and Modeling, pages 61–68.
Bernhardt, A., Barthe, L., Cani, M. P., and Wyvill, B.
(2010). Implicit blending revisited. Computer Graph-
ics Forum, 29(2):367–375.
Bessmeltsev, M., Vining, N., and Sheffer, A. (2016). Ges-
ture3D: Posing 3D Characters via Gesture Drawings.
ACM Transactions on Graphics, 35(6):165:1–165:13.
Botsch, M. and Kobbelt, L. (2004). A Remeshing Approach
to Multiresolution Modeling. Proceedings of the 2004
Eurographics ACM SIGGRAPH symposium on Geom-
etry processing SGP 04, page 185.
Choi, B., i Ribera, R. B., Lewis, J. P., Seol, Y., Hong, S.,
Eom, H., Jung, S., and Noh, J. (2016). SketchiMo:
Sketch-based Motion Editing for Articulated Charac-
ters. ACM Transactions on Graphics, 35(4):1–12.
De Paoli, C. and Singh, K. (2015). SecondSkin: Sketch-
based Construction of Layered 3D Models. Acm
Transactions on Graphics, 34(4):10.
Eitz, M., Hildebrand, K., Boubekeur, T., and Alexa, M.
(2010). Sketch-based 3D shape retrieval. In ACM
SIGGRAPH 2010 Talks on - SIGGRAPH ’10, page 1,
New York, New York, USA. ACM Press.
Eitz, M., Richter, R., Boubekeur, T., Hildebrand, K., and
Alexa, M. (2012). Sketch-based shape retrieval. ACM
Transactions on Graphics, 31(4):1–10.
Fish, N., Averkiou, M., van Kaick, O., Sorkine-Hornung,
O., Cohen-Or, D., and Mitra, N. J. (2014). Meta-
representation of shape families. ACM Transactions
on Graphics, 33(4):1–11.
Getto, R., Merz, J., Kuijper, A., and Fellner, D. W. (2017).
3D meta model generation with application in 3D ob-
ject retrieval. Proceedings of the Computer Graphics
International Conference on - CGI ’17, pages 1–6.
Havemann, S. (2005). Generative mesh modeling. PhD
thesis.
Havemann, S. and Fellner, D. W. (2003). Technical Report
TUBS-CG-2003-01 Generative Mesh Modeling. On-
line.
Herman, G. T., Rozenberg, G., and Lindenmayer, A.
(1975). Developmental systems and languages.
North-Holland Pub. Co.
Igarashi, T., Matsuoka, S., and Tanaka, H. (1999). Teddy:
a sketching interface for 3D freeform design. Pro-
ceedings of the 26th annual conference on Computer
graphics and interactive techniques - SIGGRAPH ’99,
pages 409–416.
Jorge, J. and Samavati, F., editors (2011). Sketch-based In-
terfaces and Modeling. Springer London, London.
Kazmi, I. K., You, L., and Zhang, J. J. (2014). A Survey
of Sketch Based Modeling Systems. 2014 11th Inter-
national Conference on Computer Graphics, Imaging
and Visualization, pages 27–36.
Kim, V. G., Li, W., Mitra, N. J., Chaudhuri, S., DiVerdi,
S., and Funkhouser, T. (2013). Learning part-based
templates from large collections of 3D shapes. ACM
Transactions on Graphics, 32(4):1.
Lindenmayer, A. (1968). Mathematical models for cellular
interactions in development. II. Simple and branching
filaments with two-sided inputs. Journal of theoretical
biology, 18(3):300–315.
Nealen, A., Igarashi, T., Sorkine, O., and Alexa, M.
(2007). FiberMesh. ACM Transactions on Graphics,
26(99):41.
Pagano, R. R. (2013). Understanding statistics. Oxford
University Press.
Parish, Y. I. H. and M
¨
uller, P. (2001). Procedural Modeling
of Cities. 28th annual conference on Computer graph-
ics and interactive techniques, (August):301–308.
Schmidt, R. and Singh, K. (2008). Sketch-based procedural
surface modeling and compositing using surface trees.
Computer Graphics Forum, 27(2):321–330.
Schmidt, R., Wyvill, B., Sousa, M. C., and Jorge, J. a.
(2005). ShapeShop: sketch-based solid modeling with
BlobTrees. EUROGRAPHICS Workshop on Sketch-
Based Interfaces and Modeling.
Shapira, L., Shamir, A., and Cohen-Or, D. (2008). Con-
sistent mesh partitioning and skeletonisation using
the shape diameter function. Visual Computer,
24(4):249–259.
Sorkine, O. and Alexa, M. (2007). As-Rigid-As-Possible
Surface Modeling. Proceedings of the fifth Euro-
graphics symposium on Geometry processing, pages
109–116.
Tobler, R. F., Maierhofer, S., and Wilkie, A. (2002). Mesh-
Based Parametrized L-Systems and Generalized Sub-
division for Generating Complex Geometry. Interna-
tional Journal of Shape Modeling, 08(02):173–191.
Wyvill, B., Guy, A., and Galin, E. (1999). Extending the
CSG tree. Warping, blending and Boolean operations
in an implicit surface modeling system. Computer
Graphics Forum, 18(2):149–158.
Simplified Definition of Parameter Spaces of a Procedural Model using Sketch-based Interaction
231