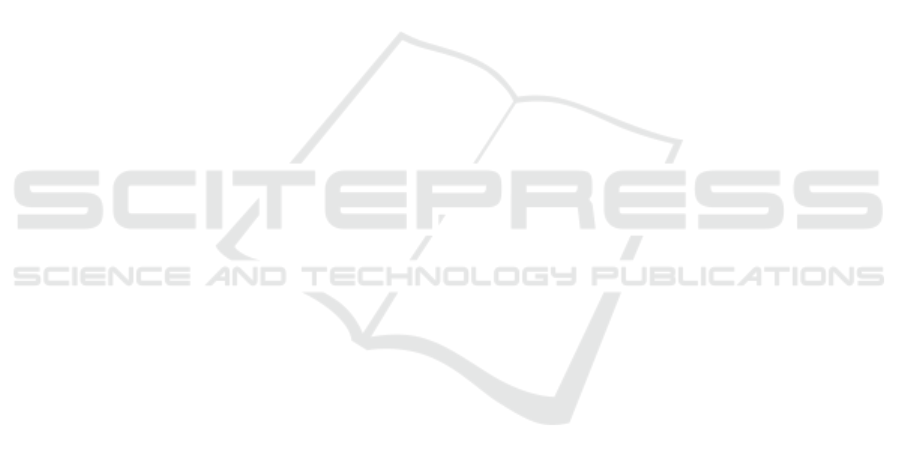
REFERENCES
Allard, J., Marchal, M. and Cotin, S., 2009. Fiber-based
fracture model for simulating soft tissue tearing. Studies
in health technology and informatics, 142, pp.13-18.
Becker, M., Ihmsen, M. and Teschner, M., 2009, March.
Corotated SPH for Deformable Solids. In NPH (pp. 27-
34).
Belytschko, T., Chen, H., Xu, J. and Zi, G., 2003. Dynamic
crack propagation based on loss of hyperbolicity and a
new discontinuous enrichment. International Journal
for Numerical Methods in Engineering, 58(12),
pp.1873-1905.
Chen, Z., Yao, M., Feng, R. and Wang, H., 2014. Physics-
inspired adaptive fracture refinement. ACM
Transactions on Graphics (TOG), 33(4), p.113.
Gingold, R.A. and Monaghan, J.J., 1977. Smoothed particle
hydrodynamics: theory and application to non-spherical
stars. Monthly notices of the royal astronomical society,
181(3), pp.375-389.
Hahn, D. and Wojtan, C., 2016. Fast approximations for
boundary element based brittle fracture simulation.
ACM Transactions on Graphics (TOG), 35(4), p.104.
Hesham, O., 2011. Fast Meshless Simulation of
Anisotropic Tearing in Elastic Solids (Thesis, Carleton
University Ottawa).
Hoetzlein, R.C. and Höllerer, T., 2008. Analyzing
Performance and Efficiency of Smoothed Particle
Hydrodynamics.
Irving, G., Teran, J. and Fedkiw, R., 2004, August.
Invertible finite elements for robust simulation of large
deformation. In Proceedings of the 2004 ACM
SIGGRAPH/Eurographics symposium on Computer
animation (pp. 131-140).
Koschier, D., Bender, J. and Thuerey, N., 2017. Robust
eXtended finite elements for complex cutting of
deformables. ACM Transactions on Graphics (TOG),
36(4), p.55.
Liu, N., He, X., Li, S. and Wang, G., 2011. Meshless
simulation of brittle fracture. Computer Animation and
Virtual Worlds, 22(2‐3), pp.115-124.
Meier, U., López, O., Monserrat, C., Juan, M.C. and
Alcaniz, M., 2005. Real-time deformable models for
surgery simulation: a survey. Computer methods and
programs in biomedicine, 77(3), pp.183-197.
Müller, M. and Gross, M., 2004, May. Interactive virtual
materials. In Proceedings of Graphics Interface 2004
(pp. 239-246).
Müller, M., Charypar, D. and Gross, M., 2003, July.
Particle-based fluid simulation for interactive
applications. In Proceedings of the 2003 ACM
SIGGRAPH/Eurographics symposium on Computer
animation (pp. 154-159).
Müller, M., Keiser, R., Nealen, A., Pauly, M., Gross, M.
and Alexa, M., 2004, August. Point based animation of
elastic, plastic and melting objects. In Proceedings of
the 2004 ACM SIGGRAPH/Eurographics symposium
on Computer animation (pp. 141-151).
Nealen, A., Müller, M., Keiser, R., Boxerman, E. and
Carlson, M., 2006, December. Physically based
deformable models in computer graphics. In Computer
graphics forum (Vol. 25, No. 4, pp. 809-836).
O'Brien, J.F. and Hodgins, J.K., 1999, July. Graphical
modeling and animation of brittle fracture. In
Proceedings of the 26th annual conference on
Computer graphics and interactive techniques (pp.
137-146).
O'Brien, J.F., Bargteil, A.W. and Hodgins, J.K., 2002.
Graphical modeling and animation of ductile fracture.
ACM transactions on graphics (TOG), 21(3), pp.291-
294.
Organ, D., Fleming, M., Terry, T. and Belytschko, T., 1996.
Continuous meshless approximations for nonconvex
bodies by diffraction and transparency. Computational
mechanics, 18(3), pp.225-235.
Parker, E.G. and O'Brien, J.F., 2009, August. Real-time
deformation and fracture in a game environment. In
Proceedings of the 2009 ACM SIGGRAPH/
Eurographics Symposium on Computer Animation (pp.
165-175).
Pfaff, T., Narain, R., de Joya, J.M. and O'Brien, J.F., 2014.
Adaptive tearing and cracking of thin sheets. ACM
Transactions on Graphics (TOG), 33(4), p.110.
Solenthaler, B., Schläfli, J. and Pajarola, R., 2007. A unified
particle model for fluid–solid interactions. Computer
Animation and Virtual Worlds, 18(1), pp.69-82.
Tan, J. and Yang, X., 2009. Physically-based fluid
animation: A survey. Science in China Series F:
Information Sciences, 52(5), pp.723-740.
Terzopoulos, D. and Fleischer, K., 1988, August. Modeling
inelastic deformation: viscolelasticity, plasticity,
fracture. In ACM Siggraph Computer Graphics (Vol.
22, No. 4, pp. 269-278).
Viccione, G., Bovolin, V. and Carratelli, E.P., 2008.
Defining and optimizing algorithms for neighbouring
particle identification in SPH fluid simulations.
International Journal for Numerical Methods in Fluids,
58(6), pp.625-638.
Zohdi, T.I., 2007. A computational framework for network
modeling of fibrous biological tissue deformation and
rupture. Computer Methods in Applied Mechanics and
Engineering, 196(31), pp.2972-2980.
Interactive Anisotropic Tearing of Elastic Solids
263