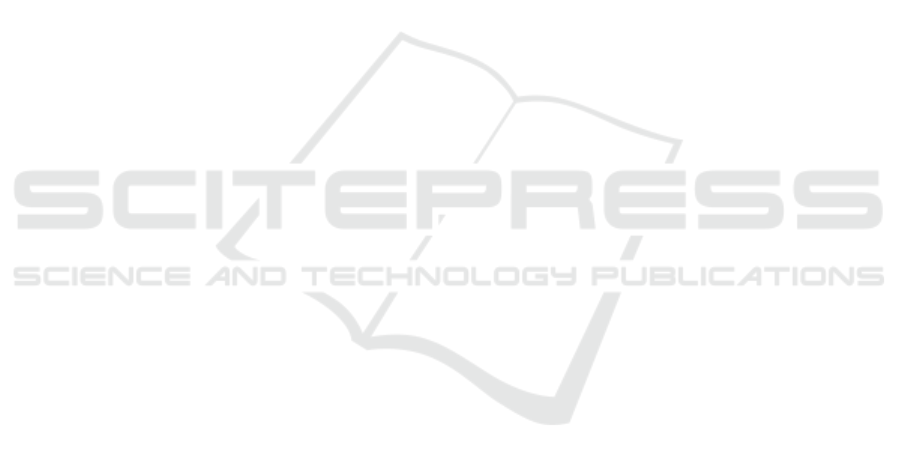
Although the presented framework for visual in-
spection is efficient and completely integrated with
the whole robotic work cell, it has certain limitations.
First, the hardware choice is suitable for inspection of
static images, but it is not suitable for video tracking.
Second, the whole software system is tied to a speci-
fic ROS version, which is not downwards compatible.
Third, the generation new processing pipelines would
require from the user some knowledge on image ana-
lysis and robotics. Fourth, new templates will have
to be generated and the parameters will have to be
re-optimized, if the robot poses or lighting conditions
change, which can be a rather time-consuming task.
8 CONCLUSIONS AND FUTURE
WORK
The computer vision framework, which is used as a
monitoring module in a highly reconfigurable robot
workcell has been presented here. The hardware as
well as software components were described and dis-
cussed. The automotive assembly use case example
was used as an application example.
As future work, we will extend the software com-
ponents to allow the user to generate processing pi-
pelines as well as test the framework on further use
cases.
ACKNOWLEDGEMENTS
The research leading to these results has received fun-
ding from the European Communitys Horizon 2020
Programme under grant agreement no. 680431, Re-
conCell(A Reconfigurable robot workCell for fast set-
up of automated assembly processes in SMEs).
REFERENCES
Bem, M., Deni
ˇ
sa, M., Ga
ˇ
spar, T., Jereb, J., Bevec, R.,
Kova
ˇ
c, I., and Ude, A. (2017). Reconfigurable fix-
ture evaluation for use in automotive light assembly.
In Advanced Robotics (ICAR), 2017 18th Internatio-
nal Conference on, pages 61–67. IEEE.
Bi, Z. M., Lang, S. Y., Shen, W., and Wang, L. (2008).
Reconfigurable manufacturing systems: the state of
the art. International Journal of Production Research,
46(4):967–992.
Bradski, G. (2000). The opencv library. Dr. Dobb’s Jour-
nal: Software Tools for the Professional Programmer,
25(11):120–123.
Duro, R. J., Gra
˜
na, M., and de Lope, J. (2010). On the po-
tential contributions of hybrid intelligent approaches
to multicomponent robotic system development. In-
formation Sciences, 180(14):2635–2648.
Eckstein, W. and Steger, C. (1999). The halcon vision sy-
stem: an example for flexible software architecture.
In Proceedings of 3rd Japanese Conference on Practi-
cal Applications of Real-Time Image Processing, pa-
ges 18–23.
European commission (2013). Factories of the future:
Multi-annual roadmap for the contractual ppp under
horizon 2020. Publications office of the European
Union: Brussels, Belgium.
Fulea, M., Popescu, S., Brad, E., Mocan, B., and Murar,
M. (2015). A literature survey on reconfigurable in-
dustrial robotic work cells. Applied Mechanics and
Materials, 762:233.
Gaspar, T., Ridge, B., Bevec, R., Bem, M., Kova
ˇ
c, I., Ude,
A., and Gosar,
ˇ
Z. (2017). Rapid hardware and soft-
ware reconfiguration in a robotic workcell. In Advan-
ced Robotics (ICAR), 2017 18th International Confe-
rence on, pages 229–236. IEEE.
Hanselman, D. C. and Littlefield, B. (2005). Mastering mat-
lab 7. Pearson/Prentice Hall.
Hartley, R. and Zisserman, A. (2003). Multiple view geome-
try in computer vision. Cambridge university press.
Kosmopoulos, D. I., Doulamis, N. D., and Voulodimos,
A. S. (2012). Bayesian filter based behavior recog-
nition in workflows allowing for user feedback. Com-
puter Vision and Image Understanding, 116(3):422–
434.
Kr
¨
uger, N., Ude, A., Petersen, H. G., Nemec, B., Ellekilde,
L.-P., Savarimuthu, T. R., Rytz, J. A., Fischer, K.,
Buch, A. G., Kraft, D., et al. (2014). Technologies
for the fast set-up of automated assembly processes.
KI-K
¨
unstliche Intelligenz, 28(4):305–313.
Liu, Z., Ukida, H., Ramuhalli, P., and Niel, K. (2015). In-
tegrated Imaging and Vision Techniques for Industrial
Inspection. Springer.
Masters, B. R., Gonzalez, R. C., and Woods, R. (2009). Di-
gital image processing. Journal of biomedical optics,
14(2):029901.
M
¨
orzinger, R., Sardis, M., Rosenberg, I., Grabner, H., Ve-
res, G., Bouchrika, I., Thaler, M., Schuster, R., Hof-
mann, A., Thallinger, G., et al. (2010). Tools for semi-
automatic monitoring of industrial workflows. In Pro-
ceedings of the first ACM international workshop on
Analysis and retrieval of tracked events and motion in
imagery streams, pages 81–86. ACM.
Quigley, M., Conley, K., Gerkey, B., Faust, J., Foote, T.,
Leibs, J., Wheeler, R., and Ng, A. Y. (2009). Ros: an
open-source robot operating system. In ICRA works-
hop on open source software, volume 3, page 5. Kobe.
Reinhard, E., Adhikhmin, M., Gooch, B., and Shirley, P.
(2001). Color transfer between images. IEEE Com-
puter graphics and applications, 21(5):34–41.
Reza, A. M. (2004). Realization of the contrast limited
adaptive histogram equalization (clahe) for real-time
image enhancement. The Journal of VLSI Signal Pro-
cessing, 38(1):35–44.