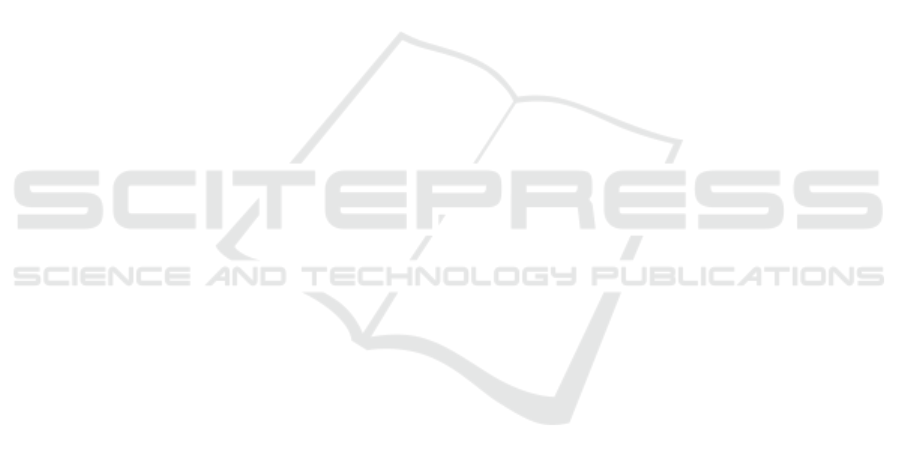
ziness, that makes the adjustment more natural. In
addition, an occupancy predictive component extends
the MPC unit in order to endow our system with an
additional proactive behavior and further enhance the
overall outcome.
The remainder of this paper is organized as fol-
lows. Section 2 provides an overview of the rela-
ted work in this area. Section 3 gives insight into
the theory behind our framework, followed by section
4, which outlines in detail our control approach. In
section 5, we describe first the user study we carried
out in order to evaluate our approach, and the corre-
sponding experimental setup. Then we present and
discuss the evaluation’s outcomes. Finally, section 6
summarizes our work and provides our final conclu-
sions.
2 RELATED WORK
Comfort, as an experience, represents a subjective
sensation of individual people (Nikolopoulou and
Steemers, 2003). Not everyone shares the same view
about whether a certain experience is comfortable or
not. Furthermore, comfort is highly relative and de-
pends strongly on the current situation. In (Ahmad-
pour, 2017) for instance, Ahmadpour confirms a high
correlation between humans’ concerns, like control,
privacy, accessibility, style, etc., the situation in which
they find themselves, and their general comfort expe-
rience. Lan et al. focus in (Lan et al., 2012) solely on
thermal comfort and investigate how high or low tem-
peratures affect human performance in an office envi-
ronment. They came to the conclusion that deviations
from the thermal comfort optimum produce a clear
negativ impact on the overall performance. Further-
more, they establish a relation between energy saving
system designs and a reduced performance of office
workers. Analyzing the behavior of people in diffe-
rent thermal environments confirms that determining
and setting the optimal thermal comfort is essential.
Amasuomo et al. in (Amasuomo and Amasuomo,
2016) tested the stress behavior of students in lecture
rooms. Their results indicate that discomfort leads
to less concentration, more tiredness and irritation.
A similar project was conducted by Steinmetz et al.
(Steinmetz and Posten, 2017), where he showed that
the response behavior differs in cold and warm envi-
ronments.
In order to determine and describe the thermal
comfort, Fanger defined in the 1970s’ the Predicted
Mean Vote (PMV) (Fanger, 1970). The PMV is a
model, which considers indoor temperature, humidity
and clothing level among others to calculate a thermal
comfort index. Section 3.1 gives a brief insight into
the theory behind the PMV model. However, Mors
et al. proved in practice that the PMV is not perfect.
Particularly, he showed that the PMV was not accu-
rate enough to set the optimal comfort for primary
school children (Mors et al., 2011). Yao et al. (Yao
et al., 2009) created the adaptive PMV (aPMV) that
uses additional seasonal differences to overcome the
PMV’s inaccuracies. The aPMV defines among ot-
hers a much lower optimal indoor temperature in cold
seasons than in hot ones. There are different studies
regarding thermal comfort. Tham et al. (Tham and
Willem, 2010) set up three test rooms, each with a dif-
ferent room temperature (20
◦
C, 23
◦
C, and 26
◦
C). The
study participants stayed in each room for 4 hours.
Sensors on the forehead, lower arm, back, hand and
foot measured the skin temperature. The research
showed that for most people, 23
◦
C reflects the opti-
mal comfort. Barrios et al. (Barrios and Kleimin-
ger, 2017) developed a framework called Comfstat to
predict the users’ comfort in an unsupervised way.
They used body sensors to measure the heart rate of
each person and showed inter alia that it is important
to train the system on each user individually to get
more accurate comfort settings. Beside that, a hea-
ting control system based on Comfstat would rely for
the most part on the heart rate sensing technology that
has to be as accurate as possible. Modern smartwat-
ches and other wearables do provide the feature of
heart rate measurement, but only very few of them,
if any, would be good enough to set a HVAC system
accurately enough.
There exists a great variety of indoor climate con-
trol approaches. Karatzoglou et al. presented in
(Karatzoglou et al., 2017) a climate control approach
based on both a Support Vector Regression (SVR)-
driven occupancy prediction model, as well as a re-
spective rule base, on top of a PID controller. Their
approach was able to enhance the thermal comfort,
while keeping the energy consumption low at the
same time. Shi et al. in (Shi et al., 2017) use an
occupancy prediction model as well to improve their
MPC controller achieving a similar high comfort and
energy efficiency. Vesely et al. (Vesel
`
y and Zeiler,
2014) propose an extension of HVAC systems in order
to be able to control microclimates and promote that
way both personalized air conditioning and energy
performance.
Many researchers apply Model Predictive Cont-
rol (MPC) in their work with promising results. The
work of Martincevic et al. support this decision (Mar-
tin
ˇ
cevi
´
c et al., 2016). They compared a conventional
temperature controller to a MPC-based one. Their in-
vestigation showed that even the simplest variant of
SMARTGREENS 2018 - 7th International Conference on Smart Cities and Green ICT Systems
90